More than an internship: the role of the students in the development of technological projects at Innova
One of the fundamental pillars for the growth of any company is the commitment to young talent. Contributing to the training and professional development of trainees is something that Innova has been doing for years, and it is firmly committed to their active participation in the company’s projects.
Innova works closely with educational and technological organizations, universities and institutions, such as the University Jaume I (UJI), Technical Professional Institutes, the Technological Institute of Packaging, Transport and Logistics ITENE, and ICEX Spain Export and Investments, among others. Through Innova’s participation in Workplace Training Programs, students from these centers can do their internships and become part of the company’s staff, thus starting their professional careers comprehensively.
In this article, we will see how students with work experience at Innova have helped develop an internal project relevant to our Electrical Technical Office and Programming Department. A project that has significantly improved efficiency, development, and training within the company.
The Value of Young Talent
When a company invests in young talent, the benefit is mutual. During their stay in the company, interns have the opportunity to develop their skills and knowledge in a real professional environment. For its part, the company gains a new perspective, which can lead to innovative ideas and creative solutions that had not been considered. The enthusiasm for learning and discovering all the current trends, are part of the value that a company like Innova adds by firmly believing in young talent.
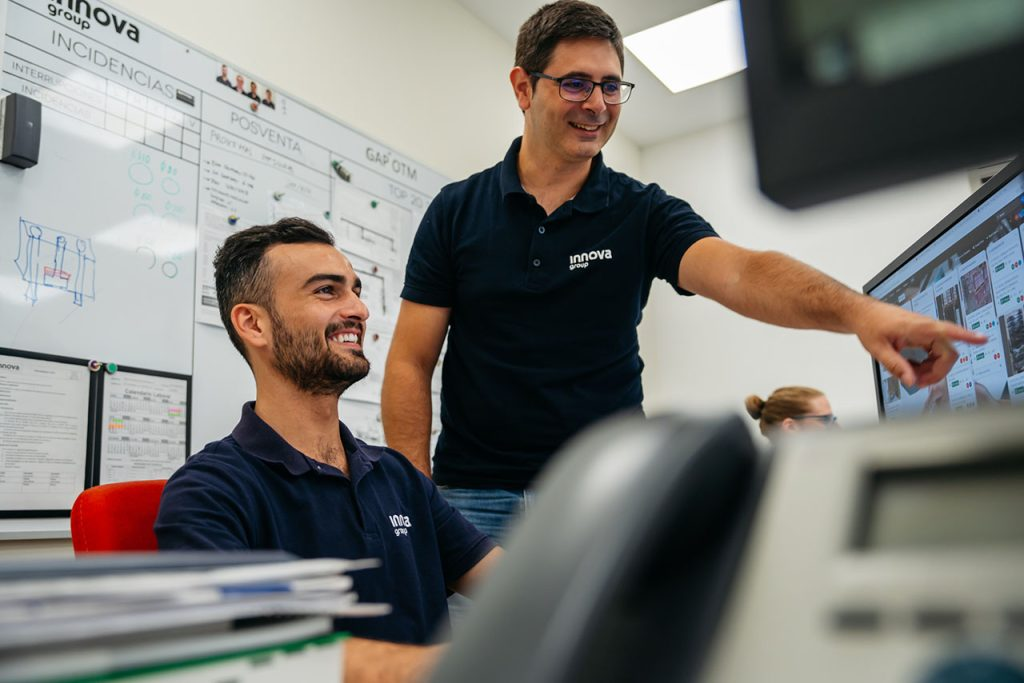
Case Study: Packaging Line Simulator
The integration of interns in the current day-to-day projects carried out by Innova can present challenges, not only because of the complexity of the project but also because of the short training time available to the students.
At Innova, we try to make the most of their short time and provide the most complete apprentice experience possible. An example of this is the internal project that our Electrical Technical Office and Programming department started to develop recently: new Packaging Line Simulator. The aim of this is to guarantee the correct operation of our machines before they are manufactured, thus making the most of time and resources and minimizing possible errors.
This department saw the need to create a packaging line programming simulator that could help discover and implement process improvements. Moreover, it decided that it would be up to the trainees to carry it out in a supervised manner.
The simulation project will allow us to:
- Improve packaging line efficiency: Electrical and Programming engineers will be able to identify and correct potential problems on packaging lines before they are manufactured, reducing downtime and increasing overall efficiency.
- Accelerate the development of new packaging systems or improvements to existing systems: The simulator will allow new packaging system designs to be tested and evaluated quickly and efficiently, speeding up the development process.
- In-house training: The simulator is also used to train employees in the use and maintenance of packaging lines, improving safety and productivity.
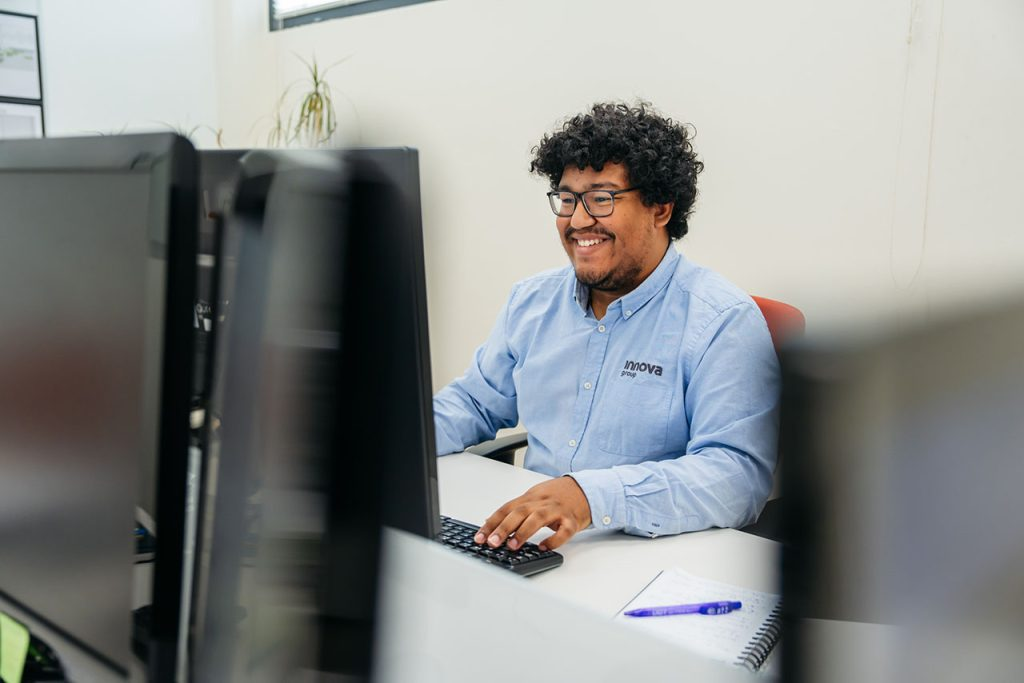
Agile and Lean methodologies: Key to the integration of trainees
One of the main challenges of student internships is that they take place in a very short time. For this reason, Innova implemented a strategy based on Agile and Lean Manufacturing work methodologies, so that the students could be part of the project in a productive and useful way. Although these two project management methodologies are different, they share the same approaches, dynamism, flexibility, and communication, which is why it is recommended to use both simultaneously.
Lean Manufacturing is a production philosophy and methodology that focuses on the continuous improvement and optimization of production systems by eliminating activities that do not add any value to the process. On the other hand, Agile is a methodology based on a set of techniques applied in short work cycles, to make the delivery process of a project more efficient.
Following both methodologies, the packaging line simulator project was broken down so that it could be done step by step, and so that it would be possible for trainees to collaborate as they joined Innova. The purpose of doing it this way is that the work carried out by the students during their stay in the company would be continued by those who joined later. In the case of the packaging line simulator, the project started with a simple roller conveyor and then developed into a complete packaging line.
This way of working with trainees has enabled them to work and apply their knowledge and skills to a common goal. The Innova-driven strategy gives students responsibility and strong experience in project management at a professional level.
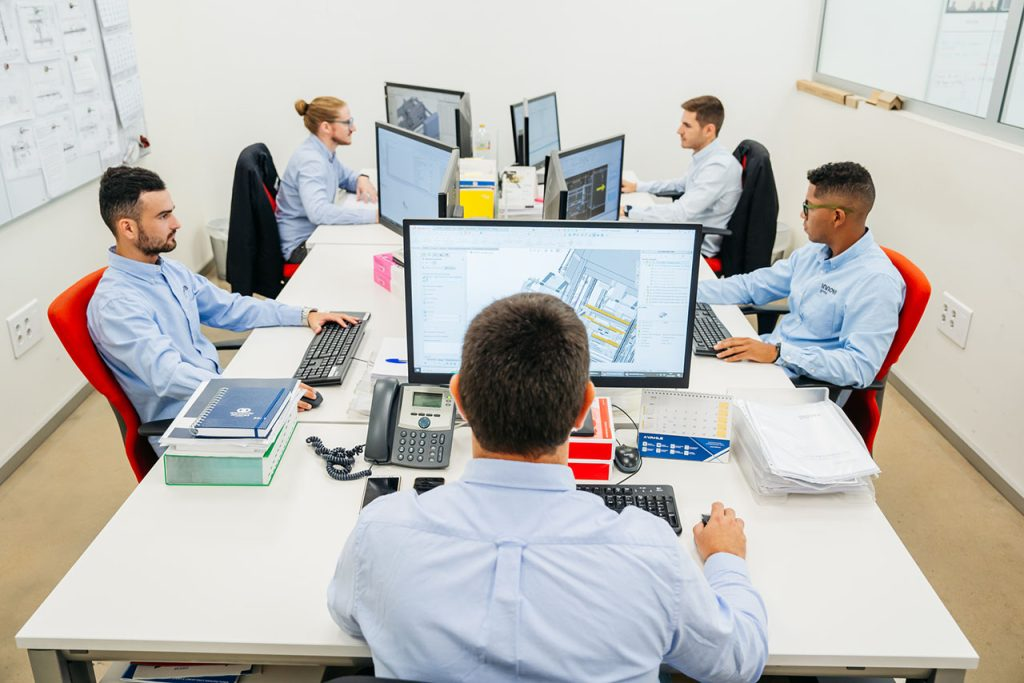
In conclusion, Innova’s commitment to young talent and its integration into highly relevant projects has proven to be a successful strategy, both for the company and for the interns. The collaboration with educational and technological institutions, and the implementation of Agile and Lean work methodologies, have not only allowed Innova to improve the efficiency and development of its packaging systems but also to train future professionals.
Do you want to be part of the Innova team and develop your talent by doing your internship here? With more than 20 years of experience as manufacturers of packaging systems and a firm commitment to the training of young professionals, at Innova, we offer you the opportunity to join relevant projects from day one. Do not hesitate to contact us without obligation.