Fritta relies on the latest packaging technology with Innova’s Stretch Hooder
How to achieve maximum protection for the chemical product with the highest quality logistics packaging? Companies in the chemical sector, and specifically in the frits and enamels sector, have clear that the Stretch Hood System is one of the most advanced packaging technologies for the protection of their pallets. Today we present one clear example of this trend, with the company Fritta, whom have opted for Innova’s Stretch Hood system with their recent installation to automate their end of line and achieve a high quality packaging for their packaged product.
Fritta, a member of Altadia Group, is a benchmark company in the sector, specialized in the manufacture of frits, glazes, digital standard inks and ceramic colours. The new project of a Stretch Hood line with Innova was recently installed in its main production plant in Onda, which offers service to the national and export markets. With this new installation in Fritta, Innova Group becomes already one of the habitual packaging machinery suppliers for Altadia Group, with whom it already has several installations.
Fritta’s challenge: full automation and packaging improvement
Fritta required a project to renovate its final packaging station in order to fully automate its end of line. At the time they were using semi-automatic pallet wrapping systems, and required a line to centralize and automate this process.
They were also looking for a system that would offer better protection and impermeability to their palletised product of FIBC and bags, something they could not achieve 100% with the wrapping system, which was causing moisture and water seepage.
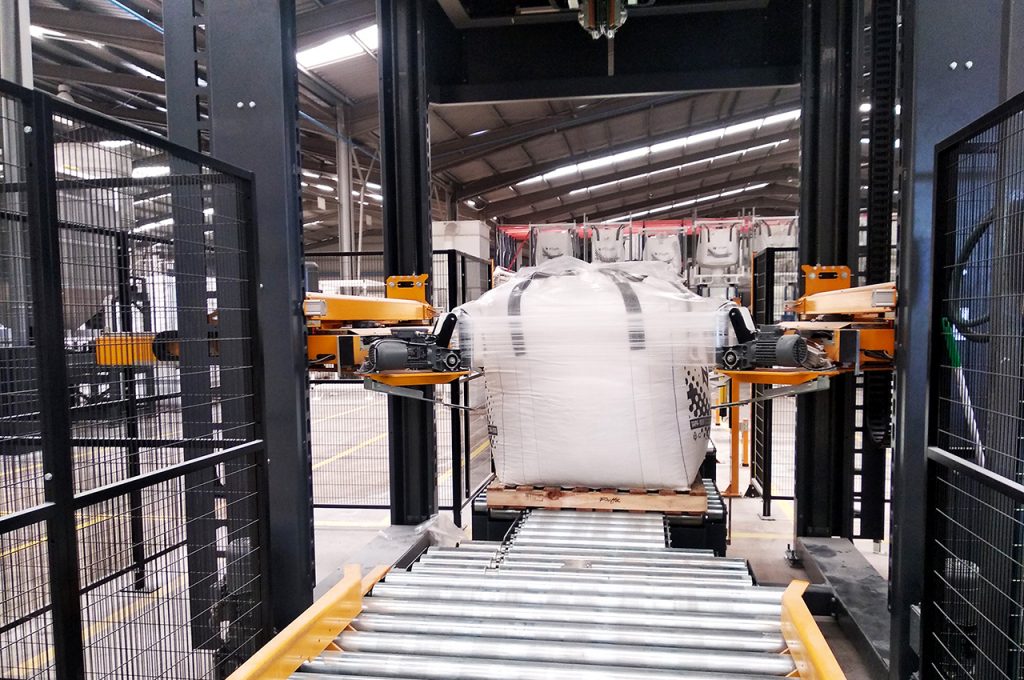
The Stretch Hood system was an optimal solution to automate Fritta’s final packaging while providing total protection and safety in the transport of its loads.
The packaging line project at Fritta
Fritta’s packaging line has been designed to fully adapt to the present and future needs of its production plant. Therefore, in this first phase, the project consisted of:
– Stretch Hood Pro1 S2 System: The Stretch Hood System adapts to the different Fritta pallet formats with FIBC and bags. In addition, this model has a double film reel that provides greater packaging autonomy.
– Conveyor line with weighing: The installation has an infeed and outfeed conveyor line adapted to Fritta’s load transport vehicles. In addition, the infeed line also includes a pallet weighing system that provides Fritta with digital information of the final weight of each pallet, for subsequent logistical processing in its ERP.
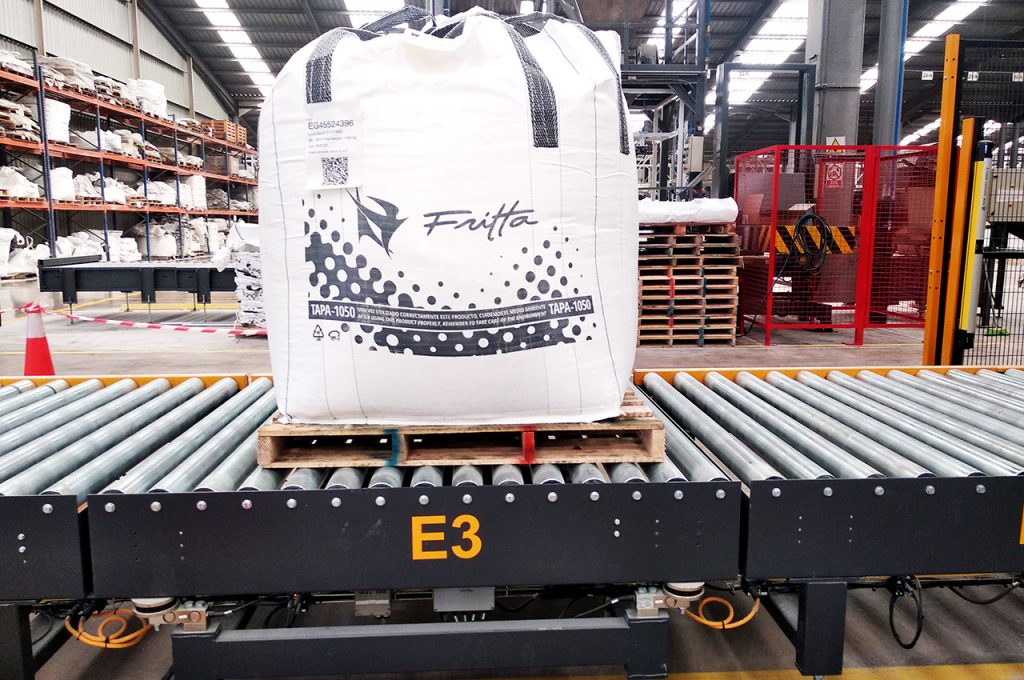
Results for Fritta: brand image, sustainability and commitment to the future
The new Stretch Hood installation has resulted in a connected, centralized and automated end-of-line. In addition to improving the quality of the packaging itself, Fritta has also improved its product presentation and brand image with a fully transparent and spotless packaging.
In line with Fritta’s Corporate Social Responsibility work, the Stretch Hood system also provides a considerable reduction in film usage, thus contributing to Fritta’s environmental actions.
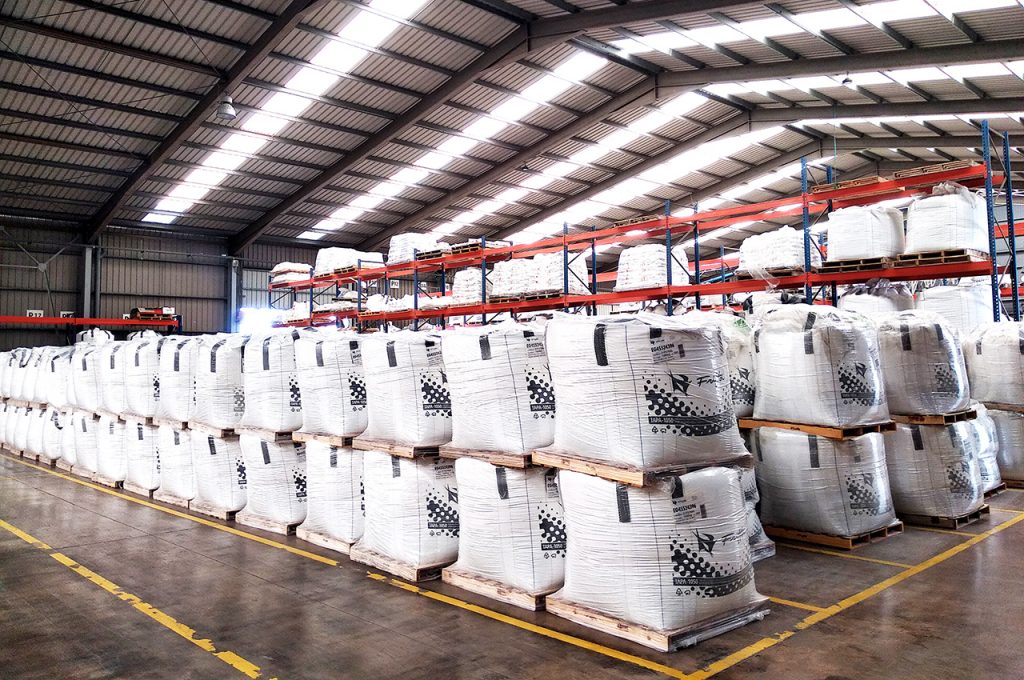
Fritta has expressed its satisfaction with the project and proof of this is its future commitment with Innova Group, with which it is already working on an extension of the packaging line in Phases 2 and 3 to connect with the rest of the production plant.
For Innova, working with Fritta has been a pleasure as it is an outstanding company in the sector with which we share values and passion for innovation, new technologies and care for the environment.
Thank you Fritta for trusting Innova Group!
#WeAreYourPartner
#WeAreInnovaGroup