Stainless steel: the key for packaging refrigerated and frozen loads
What are the logistical challenges that the refrigerated food industry encounters? Which are the best packaging systems that for this type of cargo? Staining steel finishing has become an indispensable solution for companies that require efficient packaging processes and machinery that lasts over time. In this article, we will be answering some of the questions about this particular steel material that has become highly sought-after for packaging various products. We will be discussing the advantages this material offers and how we apply it to our range of packaging systems.
Why stainless steel in packaging systems?
Perishable products require extra care compared to non-perishable items. The manufacturers of refrigerated and frozen goods must take into account not only the protection of the product itself, but also the packaging that preserves the cold chain and shields the products from external elements which can negatively impact their taste, smell, and appearance, such as high temperatures, humidity, and mold. These manufacturers must also consider all machinery and systems of their packaging line.
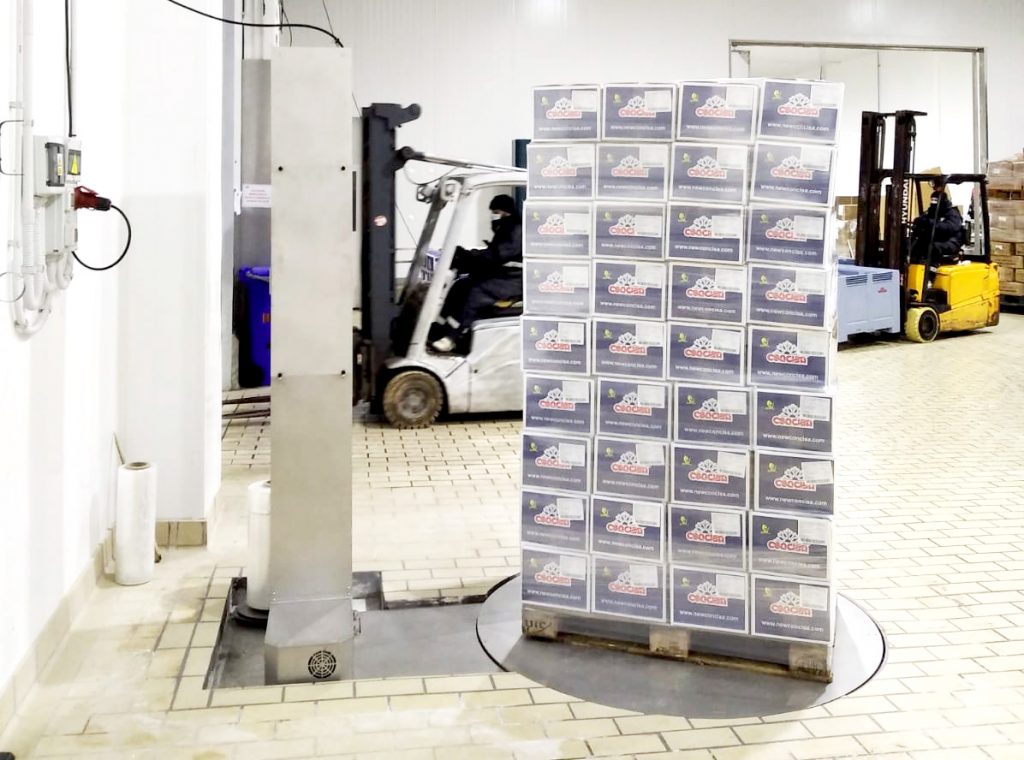
When setting up a production line, it’s important to analyze which systems will come in direct contact with the products being produced. This will help determine if those systems are susceptible to corrosion from humidity or other environmental factors. By drawing on previous factory experience, it’s possible to identify machinery that is more prone to wearing down or experiencing component deterioration. Even in cases where the packaging process involves palletized cargo, the packaging system (whether it’s strapping, wrapping, or stretch hooding) may have little direct contact with the product. However, it could still be impacted by the factory environment.
To prevent this type of damage to the machinery, the best solution is to always include stainless steel components.
Advantages of stainless steel machinery
Packaging machinery with stainless steel have become an indispensable solution for Food & Beverage companies that require a more efficient packaging process and longer machinery life. Some of the specific advantages provided by this material:
- 1. Durability and corrosion resistance
This type of steel is a robust and corrosion-resistant material, making it an ideal choice for humid, wet, and cold environments such as those found in the refrigerated goods industries. This material can withstand daily use and contact with a variety of materials, including liquids and chemicals, without significant damage or wear.
Moreover, machines with a stainless steel finish have a longer service life than those made of other materials, which translates into lower maintenance and replacement costs.
- 2. Ease of cleaning and hygiene
Stainless steel is a non-porous material with a smooth surface, which makes it easy to clean and disinfect. The smooth surface of this alloy doesn’t allow bacteria and mold to adhere easily, which contributes to maintain machine hygiene and food safety.
- 3. Image and professionalism
This steel-type finish not only allows the machine components to have less wear and tear but also prevents visual degradation of the machine, avoiding metal corrosion and a rusty appearance. In this way, a packaging machine with stainless steel gains in presentation and brand image, both in the factory itself and for customers and visitors. Additionally, this type of finish also provides a modern, elegant, and professional look, which also helps the perception of the company’s quality and its products.
- 4. Sustainability and residual value
Stainless steel is a recyclable material with a high residual value, which makes it a sustainable option in the long term.
Being recyclable, this material contributes to reducing the amount of waste generated by obsolete packaging machinery.
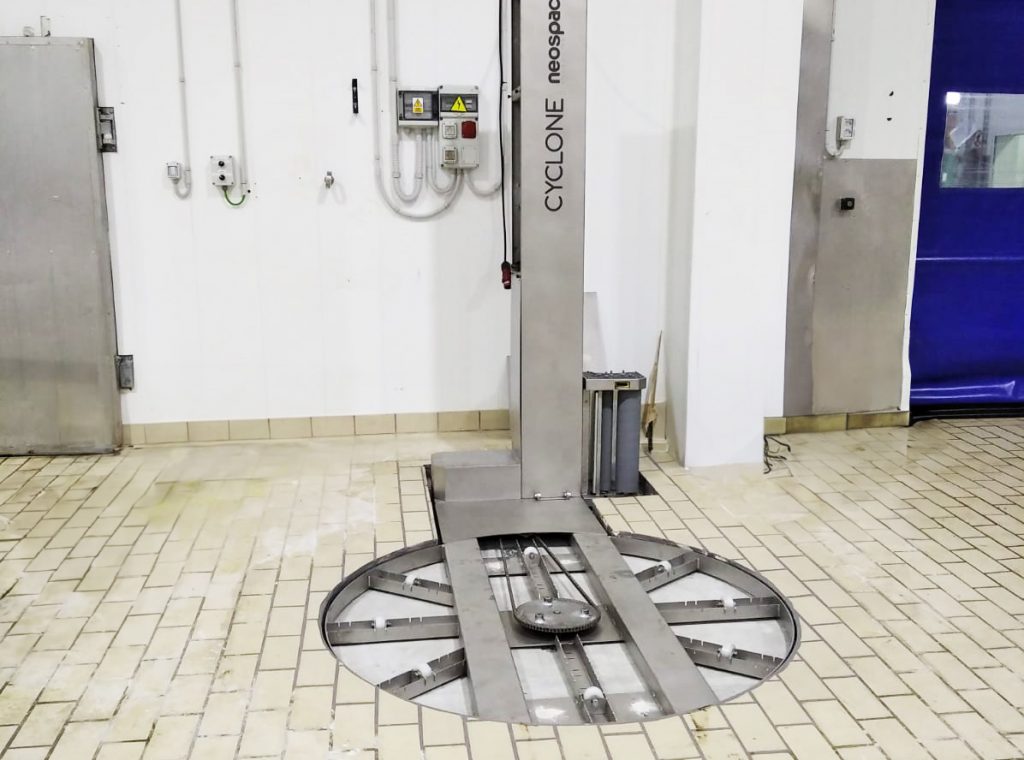
Packaging options with stainless steel
At Innova, we are specialists in packaging, so we manufacture machinery adaptable to any type of sector. In this case, we offer packaging equipment with stainless steel components in our whole range of packaging systems, incorporating these elements directly in its manufacture or adding them later. For this purpose, we carry out a study of the product specifications and packaging conditions of the factory, to fully adapt to your needs. In this study, we take into account variables such as:
- Product characteristics: if it is refrigerated, frozen, deep-frozen, moist, or contains corrosive components (salt or other food chemicals).
- Characteristics of the installation and the environment: if the packaging system must be in a cold area or if the environment is a corrosive one (such as a salt factory, for example) the components must be adapted.
- Packaging process: here we consider what other packaging systems are included in the final packaging process, or what type of primary and secondary packaging (wrapping, boxing, crating, etc.) are used to protect the product unit. For example, boxes of frozen fish or supermarket ice cream already have 2 or 3 layers of packaging before reaching the final palletizing or stretch wrapping.
How can this material be applied in packaging machinery?
As we have seen, the stainless steel finish is the best solution for packaging loads that are in cold, corrosive, or humid environments. Using this material ensures that the machine is in perfect condition to be in contact with the product. But, how can it be applied to the packaging machine?
- Total finishing in stainless steel: Specifically, the type 316 of this material is used for parts that are in direct contact with frozen or refrigerated products, as it is the most suitable material to avoid physical wear of the components in this type of environment.
- Finishing of certain components: the 316 stainless steel is also used but only on parts or components that are in contact and suffer from corrosion due to moisture or chemical effects.
- Anticorrosion paint: Even if the recommended material for humid or cold environments is stainless steel, anti-corrosion paint can also be used as an alternative for a budget investment.
Examples of packaging systems with Stainless Steel
At Innova, we have extensive experience in projects with stainless steel or anticorrosive finishes, not only for the food industry but also for the chemical industry and other corrosive products such as salt, bleach, etc. Some examples of packaging projects designed with this type of steel are:
- Cyclone INOX semi-automatic wrapper: Our Turntable Stretch Wrapper Cyclone is designed entirely with stainless steel components with the performance and complements of a standard wrapper. This stretch wrapper is an already installed solution for some of our customers who work with fresh or frozen products.
- Automatic arm Stretch Wrapper: The entire structure of the Stretch Wrapper, from the frame to the arm and even the conveyors, can be made of stainless steel to guarantee maximum durability and resistance to corrosion. An example of this application is the packaging of salt bags with a stainless steel stretch wrapper.
- Pallet conveyor systems: Pallet conveyors can also be made using this material . We can include INOX chains and rollers made for packaging lines installed in humid, and or cold environments.
- Stretch Hood System: Our Stretch Hood system can also be designed and assembled with stainless steel components. In this case, we can include the machinery frame and pillars, hooding arms, and other elements that are in contact with the product.
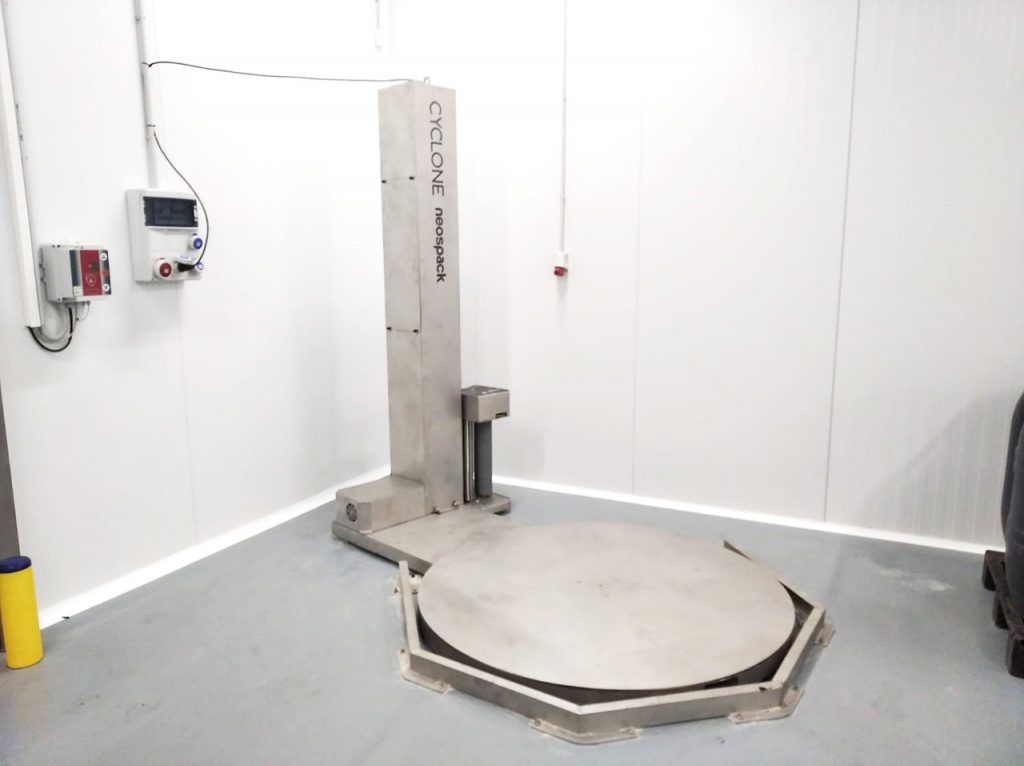
At Innova, we can adapt and implement components changes to our machinery to adapt to the manufacturing, so as not to break the cold chain. We thoroughly analyze each project to determine which components will come into contact with the product and the working environment, to provide tailored packaging solutions for each specific case.
If you are looking for high-quality packaging solutions adaptable to your specific needs, do not hesitate to contact us. Our technical sales team will be happy to advise you and help you find the perfect solution for your company.