TOP 10 Most Frequently Asked Questions About Safety Systems in a Packaging Line
Safety in packaging lines is a fundamental aspect to protect technical personnel.
At Innova, the integration of safety systems at the end of the line is not limited to complying with current safety regulations; rather, it is integrated from the design phase to adapt to any environment and meet the client’s needs.
In this article, we present the 10 most frequently asked questions we receive as a packaging systems manufacturer, regarding safety elements in a line, from the essential and mandatory ones to those that are optional but help improve line productivity.
TOP 10 Most Frequently Asked Questions About Safety Systems
- What safety systems are essential in a packaging line?
- What type of signaling can packaging systems include?
- How does the control panel help ensure safety?
- What happens if an operator enters the work area while the machine is operating?
- How is protection ensured during maintenance tasks?
- What happens if a breakdown or safety failure occurs during production?
- Can the level of safety be adapted to the working environment?
- How are safety systems adapted to comply with each country’s regulations?
- What training is required for personnel regarding safety systems?
- How does safety contribute to improving productivity in a packaging line?
1. What safety systems are essential in a packaging line?
According to international workplace safety regulations, a packaging line or any type of automatic machinery must include a safety perimeter (usually defined by physical or photoelectric barriers), an emergency stop system, and alarm and signaling systems. To meet these requirements, specific elements must be included in a packaging line.
Safety area:
- Perimeter fencing: A metal fence that restricts physical access to the machinery during operation. Access is only possible through safety entry doors.
- Safety barriers with photocells: Used as a complement to fencing or as an alternative. Typically used in areas that need to be accessible at certain times when the machinery is not in operation. If someone enters a photocell area during the wrapping cycle, an alarm will sound, and the system will stop for safety reasons.
- Accessible emergency stops: Buttons located at different points on the machine that allow for an immediate stop in case of any unforeseen event.
- Access systems with keys or authorized buttons: Access control mechanisms that prevent the use of the machine or entry into certain zones without prior authorization.
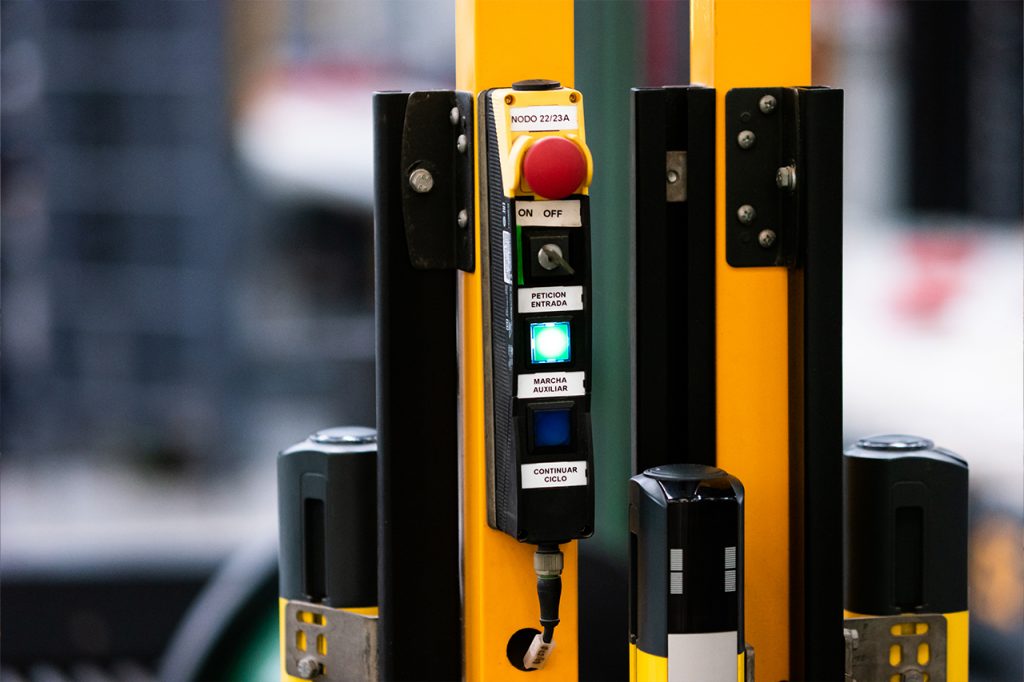
Safety control:
- Safety PLC (Programmable Logic Controller): Monitors and controls all devices related to safety, such as emergency stops, photoelectric barriers, door sensors, etc. It is programmed to ensure a quick and controlled response to any incident.
Safety signaling:
- Audible and visual signaling: A line must include some form of signaling in the event of faults, accidents, or stops, which can be carried out through various devices detailed below.
2. What type of safety signaling can packaging systems include?
In addition to the safety systems mentioned in the previous point, another important element in a machinery installation is audible and visual signaling. Each type of signal serves a specific function, and in most cases, they operate complementarily.
- Audible signaling: Sound alarms that warn of an action in progress, such as the start of a wrapping cycle, a mechanical system failure, or improper door opening.
- Visual signaling: Light beacons to indicate the machine’s status. For example, Red indicates an alarm or emergency stop, Yellow alerts to an abnormal situation or one requiring attention, Green shows that everything is functioning properly, and Blue indicates a specific action to be taken. At Innova, we usually work with only two (green-red) or three (green-yellow-red) colors, as requested by our clients.
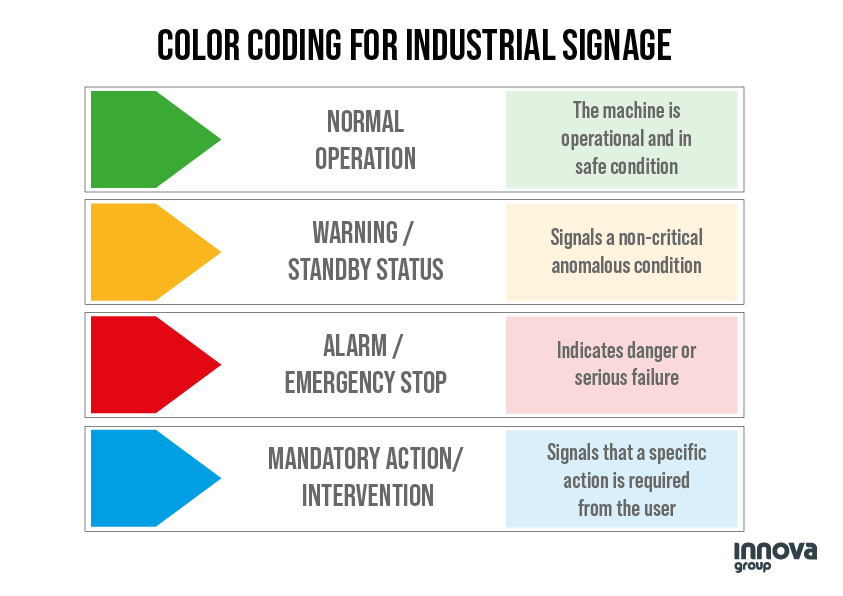
3. How does the control panel help guarantee safety?
The HMI control panel included in packaging systems is a fundamental tool for guaranteeing safety. The HMI allows:
- Real-time monitoring of all safety devices
- Display of alarms and incidents in a clear and prioritized manner
- Restriction of access to certain functions through passwords or electronic keys, preventing unauthorized use
- Activation of safe modes, such as maintenance or emergency stop
- Recording of fault history, facilitating incident traceability, and preventive maintenance
- Remote connection for technical support, which also enables safe diagnosis and resolution of faults
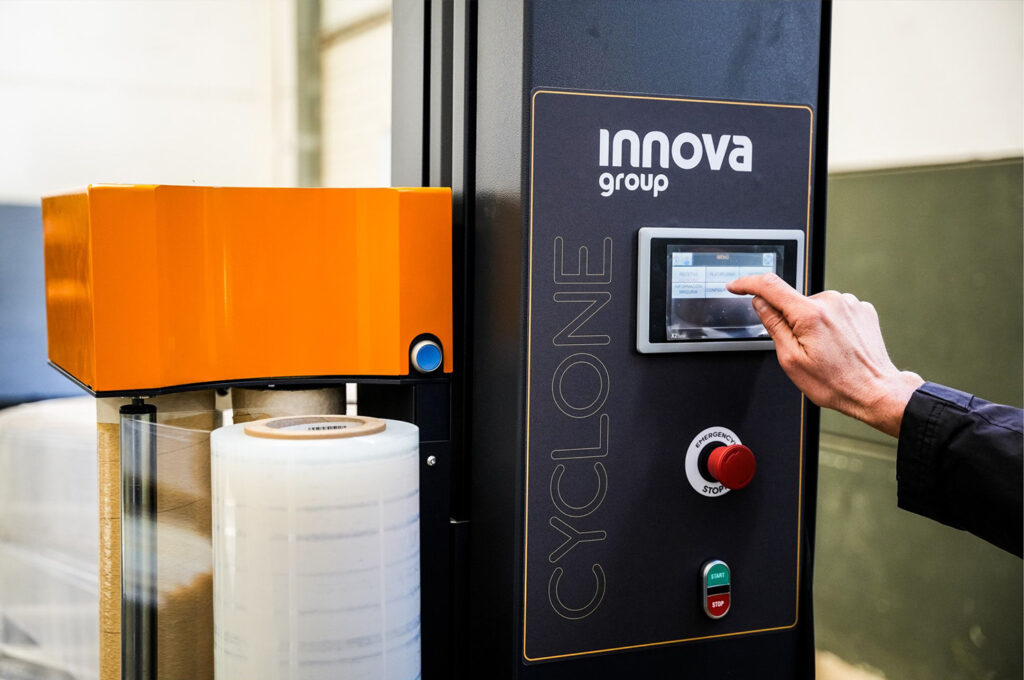
4. What happens if an operator enters the work zone while the machine is operating?
If an operator enters the work area while the machine is in operation, the safety systems react immediately to stop the process and prevent any accidents.
This automatic response is achieved through different devices previously mentioned, such as safety barriers with photocells that detect the intrusion and stop the cycle, access systems that prevent doors from opening during operation, and a safety PLC that supervises the entire system and stops the machine if an incident is detected.
5. How is operator protection ensured during maintenance tasks?
To carry out maintenance work safely, the machine must first be disabled with a key, the main disconnect switch must be turned off, and a lockout tag must be applied.
When the system is shut down, Innova’s packaging machinery includes internal fall protection systems on its moving parts, so that all systems automatically lock. Once activated, mechanical safety cylinders engage on the guide attached to the machine frame, preventing any movement or collapse of moving components and protecting technical staff.
These systems are also triggered in emergencies, electrical failures, or when someone crosses the safety barriers (whether the machine is stopped or not).
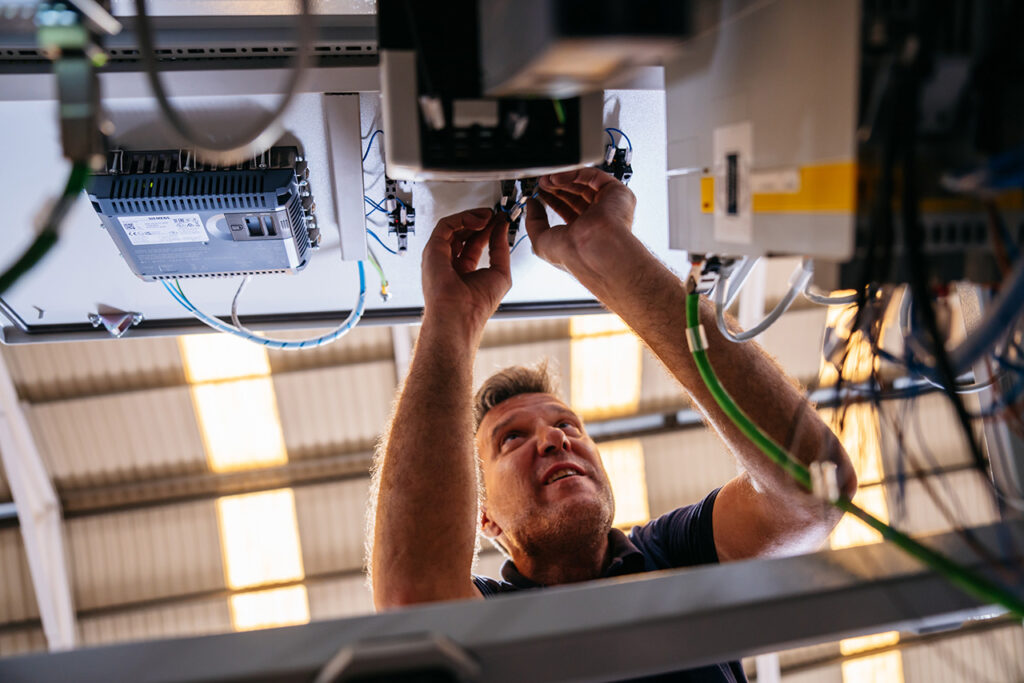
6. What happens if a fault or safety failure occurs during production?
When a fault is detected, the system stops automatically and safely via the safety PLC. At the same time, audible or visual alarms are activated; multiple system functions are blocked, including the fall protection system; and an alarm is displayed on the HMI panel.
The operator can see on the HMI panel what the exact cause of the failure or error is, enabling a quick and safe intervention that reduces downtime and avoids additional risks. Remote diagnostics are also possible, allowing for even faster resolution.
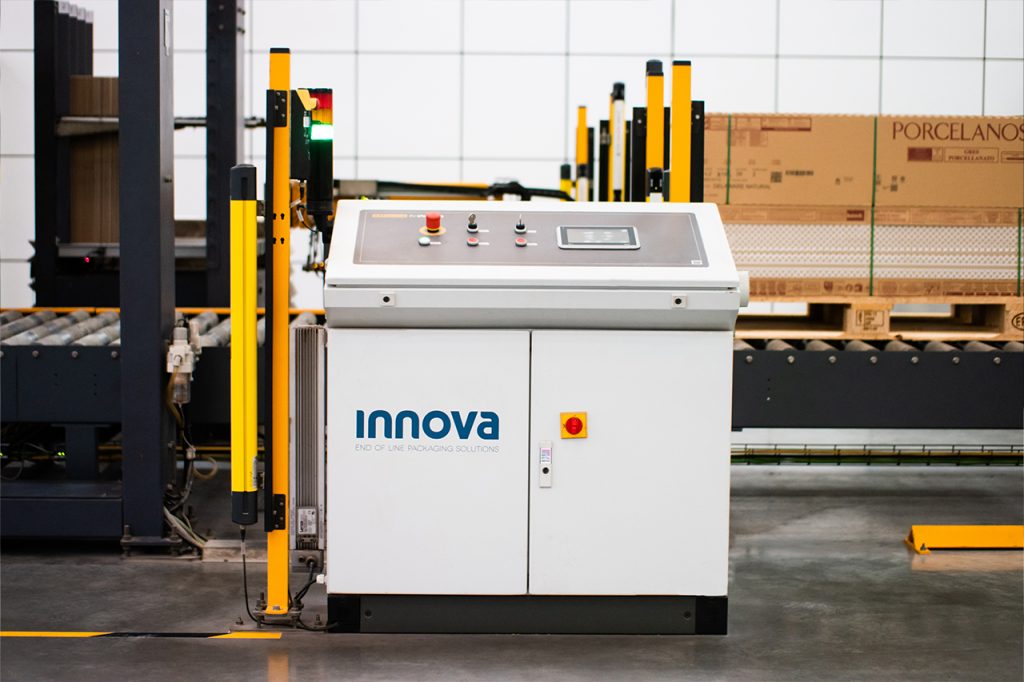
7. Can the level of safety be adapted to the working environment?
Yes, the level of safety can be adapted to the specific conditions of the work environment where the packaging system will be installed. During the project design phase, the technical team studies both production needs and environmental conditions (presence of moisture, dust, extreme temperatures, or limited space) to implement appropriate safety solutions.
8. What are the most common adaptations for special environments or requirements?
Some of the most common safety adaptations include:
- Reduced space or special packaging line layout: Photoelectric barriers in tight spaces or per customer request. Enclosures and perimeter protections can be modified when other machinery is nearby or space is limited, ensuring operator access and proper risk zone separation.
- Special safety accesses: Based on customer safety requirements, special maintenance access solutions can be designed, such as the maintenance ladder with custom steps and railing on our Stretch Hood system.
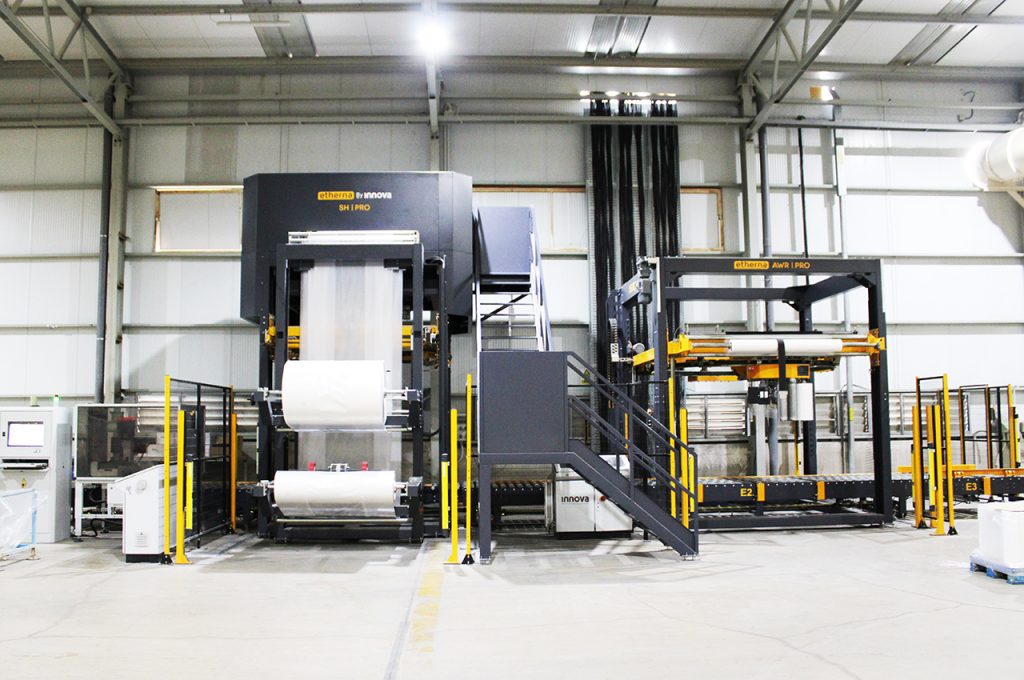
- Protection for special environments: For humid environments, electrical components with IP65 or IP67 protection ratings can be added to ensure safe insulation against particles or splashes. In dusty or drafty environments, protective covers can be installed on the machine chassis to safeguard components and the wrapping/hooding system.
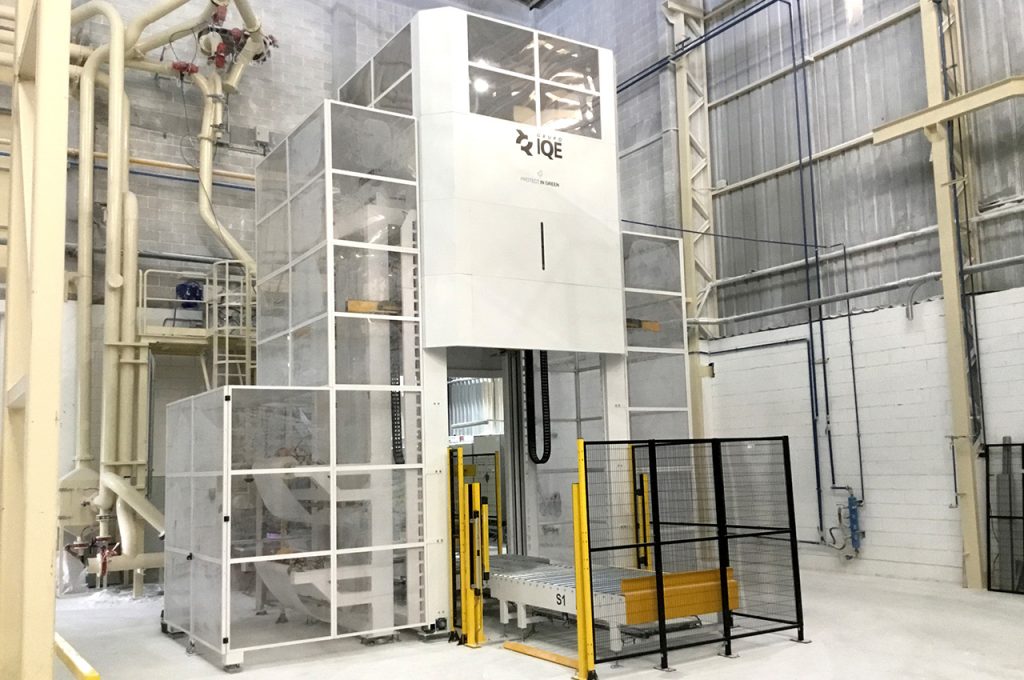
- Refrigeration or corrosive environments: For frozen or corrosive products (such as salt or chemicals), stainless steel (INOX) machinery is recommended, offering corrosion resistance and compliance with the most demanding hygiene standards.
9. How are safety systems adapted to comply with each country’s regulations?
Each project considers the client’s and country’s specific requirements. For example, in Europe, Innova designs and manufactures its systems in compliance with the Machinery Directive CE 2006/42/EC. In addition to European safety regulations, we also adapt our packaging lines and machinery to standards such as NR12 (Brazil), UL (USA), or CSA (Canada).
10. What training is required for personnel regarding safety systems?
At Innova, when a packaging line is installed, we offer training for operators and technical personnel who will be working with our systems. This includes training in preventive maintenance, safe operation, HMI panel use, alarm recognition, and more.
Technical manuals are also provided to ensure technicians avoid improper practices and extend the life of the equipment.
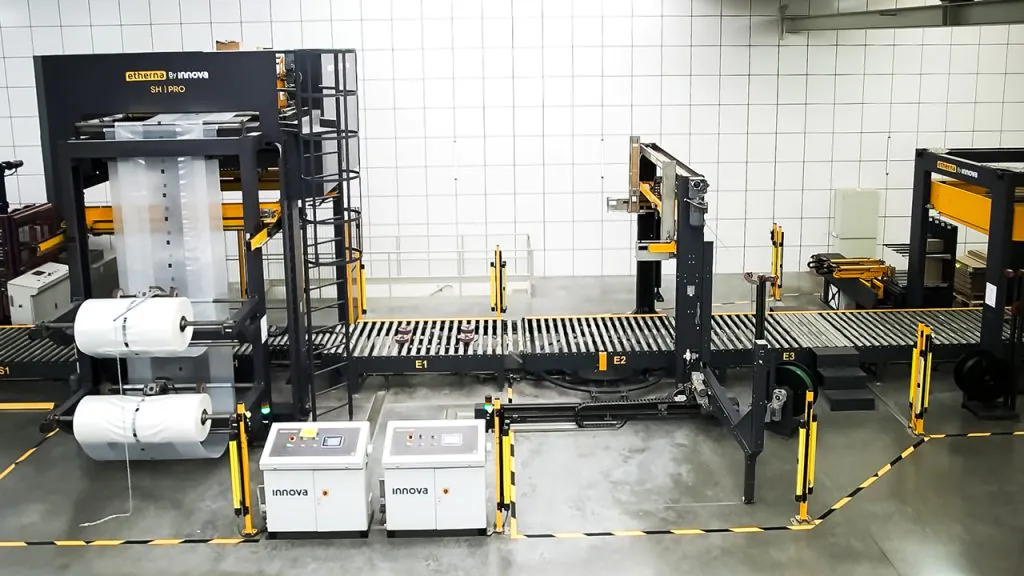
In conclusion, having a well-integrated and customized safety system not only protects technical personnel but also ensures the line operates more efficiently and productively while complying with all current safety regulations. At Innova, we manufacture solutions tailored to the specific needs of each client and industry. Contact our technical team to learn how we can help you improve the safety and performance of your end-of-line operations.