Why automate the end-of-line packaging? Solving the problems of manual end-of-line processes
Is it necessary for the entire end-of-line packaging to be automated? What kind of companies should automate their pallet packaging? From which production levels is automation essential? Although the advantages of automating the end-of-line packaging may seem obvious, in today’s article we will discuss the main keys to doing so and the main problems caused by manual processes.
When is it necessary to automate the end of line packaging?
The answer may depend on many factors, but in principle a medium-sized company with a production of more than 15-20 pallets per hour should already have automatic or semi-automatic systems for palletizing and packaging. Even so, the definition of when to automate or not, is not so clear since it depends on many factors of the company and its production. For example, according to our experience in the end of line, companies that consider automating take the leap when:
- The company has little production but has had problems such as loss or damage in the transportation of its products.
- The slow manual palletizing and packaging processes are affecting customer deliveries.
- The company plans to increase its production and therefore needs an automated end-of-line to meet the production flow.
- The manual processes (palletizing and/or packaging) are affecting several areas of the company: logistics, production, human resources, etc.
- And the most critical, when manual processes cause accidents and incidents in the factory, and even danger to the health of its workers.
As we can see, even with reduced production, there are many reasons that influence the need to automate.
Most common problems with manual processes
Let us now look at the most common problems that can be caused by manual systems at the end of the line, starting with palletizing and ending with packaging the pallet.
1. Problems with manual palletizing:
Automated palletizing is the key to ensuring load stability and even correct application of the subsequent pallet packaging. Therefore, even if it is possible to palletize manually, an error in just one of the palletizing elements can affect the overall safety of the load:
- Unstable loads: Due to improperly secured cargo, protruding packages, unstable palletizing mosaics or misaligned loads, among others.
- Detachment and shifting of cargo: In addition to the problems of poor cargo securing, there are also problems due to inadequate sizes palletizing , such as the load being bigger or smaller than the pallet base or having different sizes between packages, which can cause shifting of the goods.
- Loss or damage of product: An unsecured or unstable load can damage the product or even cause loss of part of the palletized package.
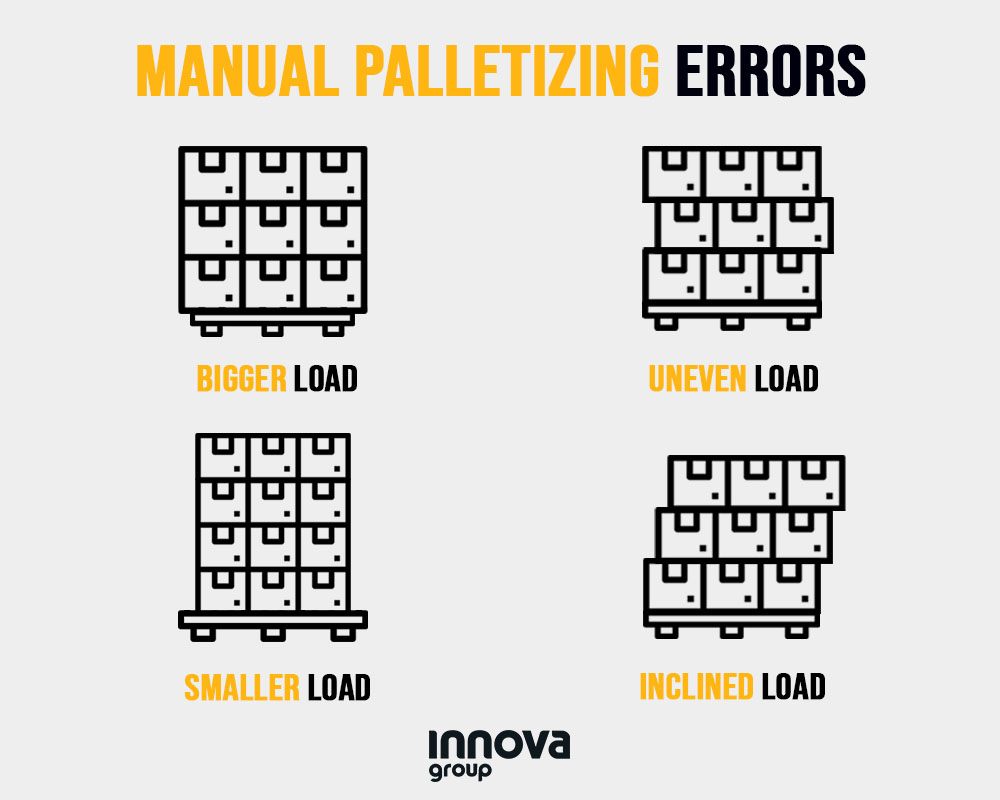
2. Incorrect application of consumables:
The next stage where manual processes are affected is in the packaging itself. The most common cause is the incorrect application of consumables such as film or pallet strapping and therefore problems in the pallet packaging.
- Poor fastening: Both in the case of wrapping film or strapping, it is very difficult to ensure the same hold that can be achieved with automatic packaging equipment. The cases we find in manual processes are poorly applied strapping, for example diagonally, or unstretched strapping due to manual wrapping.
- Use of excessive amount of consumables per pallet: In manual processes more consumables are usually used than with a system that determines the exact amount of film or strap to be used. This can cause losses for the company that could amortize the investment in automatic or semi-automatic packaging equipment just by the savings in consumables.
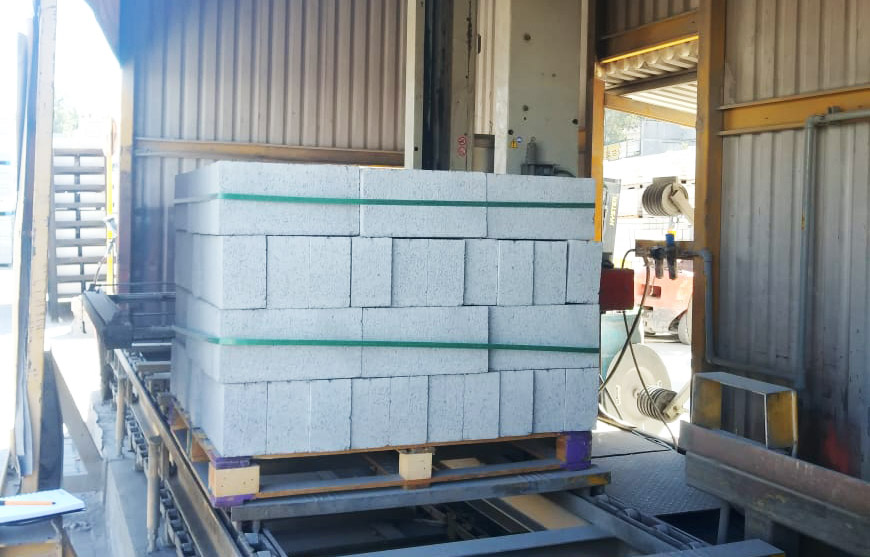
3. Workplace accidents and labor risks
Finally, the most serious consequence of manual pallet packaging is the workplace accidents and labor health risks they can cause.
- Accident prevention in the factory: Automatic and semi-automatic packaging systems always include safety systems to avoid possible accidents during packaging or palletizing. One of the problems of the manual process is precisely the human error and accidents in the factory that can occur when handling heavy loads (e.g. with manual palletizing) or manual packaging machinery (e.g. a battery pallet strapping machine that fails).
- Health risks to the worker: In addition to workplace accidents (with or without consequences for the worker), manual processes have a strong impact on the worker’s health due to the handling of heavy loads, repetitive work movements (e.g. in pallet wrapping machine) or harmful effects on workers (e.g. due to combustion in manual shrink wrapping).
- Regulatory compliance: Last but not least, companies are not only faced with solving manual problems and avoiding accidents, but must also respond to increasingly demanding safety regulations at work. A fully automated packaging system, as in the case of Innova’s packaging systems, already complies with the safety regulations required at EU level.
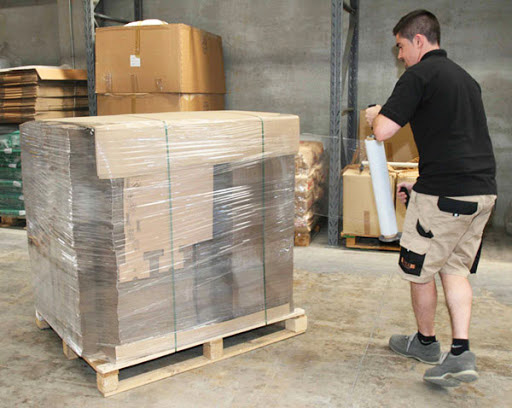
Essential packaging systems requiring automation
In view of the need to automate, there are systems that must be automatic for safety and product securing reasons. In this sense, we would highlight two essential stages of the end of line:
- Automated palletizing: To ensure load stability and avoid damage or displacement, it is essential to have an automatic palletizing system that ensures the load on the pallet. This stage is also essential in the prevention of labor risks in the factory, to avoid possible damages when handling heavy loads.
- Pallet wrapping system: Among all end-of-line packaging systems, the most commonly used is pallet wrapping in either automatic or semi-automatic versions (see semi-automatic pallet wrapping machine). Using a non-manual wrapping system secures and fixes the load with the pallet, as well as protecting it during transport and handling. There are also a multitude of stretch wrapping machine models on the market that provide not only safety for the product, but also for the final packaging process itself.
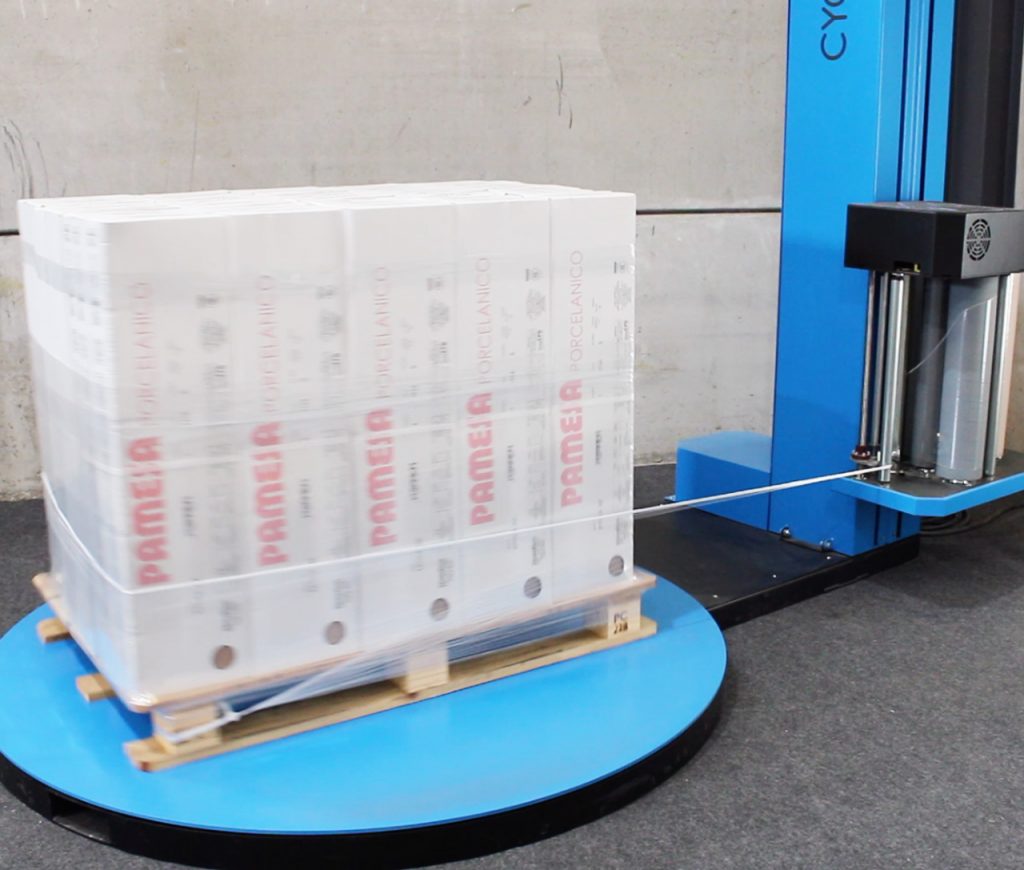
In short, although it is obvious that automating has many advantages, the disadvantages and problems caused by manual processes are even more important. Do not hesitate to consult with our technical team all the possibilities of end-of-line automation, we will be happy to assist you.