How to get the most out of your Packaging Systems with the Preventive Maintenance Plan by Innova
How to avoid production downtime? How to reduce and eliminate possible breakdowns of machines that are constantly in operation? The answer lies without doubt in having a sound Preventive Maintenance Plan. At Innova Group, as expert manufacturers of industrial packaging systems, we offer a specialized Preventive Maintenance Plan optimized for the needs of each of our customers, so that the performance of your installation goes from being a concern to a peace of mind.
How does the Innova Maintenance Plan work?
A preventive maintenance program is carried out throughout the year at each of our facilities at the different customers to check the condition of our machinery and prevent future wear and tear or unexpected breakdowns. The customer obtains total control and safety of the operation of their equipment, while achieving greater profitability and performance of the installation.
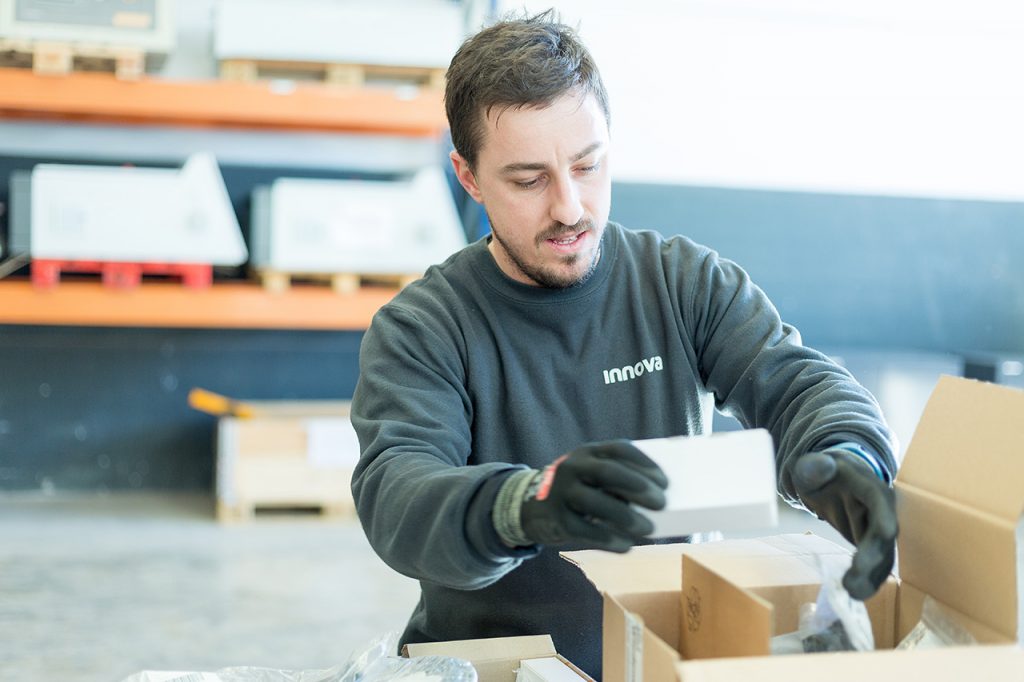
Keys to the Innova Group Maintenance Plan:
The Maintenance Plan includes a number of essential points to ensure its success:
1. Definition of the Maintenance Plan according to the customer and installation
Our technical team designs the Maintenance Plan that best suits the customer’s needs and installation. Each packaging line has a maintenance plan that takes into account the specifications of the machines that make up the line, the years of operation and use of the machines, the history of previous failures and worn out parts… among many other aspects.
2. Maintenance planning with the customer
Once the details of the maintenance plan have been agreed with the customer, we determine the best dates to carry it out. These are planned throughout the year so as to affect each customer’s production as little as possible.
For this purpose, we offer the maintenance service from our Head Office in Spain and subsidiaries in Mexico, Brazil and other delegations.
3. Diagnostic report on the condition of the machinery
Once the maintenance has been scheduled and planned, our technicians carry out a visit in which they prepare a diagnostic report (Annual Technical Report) on the state of the machinery. This report consists of the identification of preventive actions and replacement of parts that may have incidents due to wear and tear or a replacement scheduled by the client’s production parameters.
In addition to the preventive review, our service also includes a predictive diagnosis on certain components of the machinery, such as in the case of strapping heads. Our technicians analyze the data of the head usage in order to predict the need for replacement of the parts.
During the diagnosis of the machine, the technician also has the support from our Engineering Office, thanks to the remote connection of the machinery through which it is possible to access the interface and program and update the PLC if necessary.
4. Preventive maintenance actions
As soon as all the actions to be carried out have been detected in the report, we proceed to check all the components that have suffered wear and tear and need revision and replacement. The maintenance tasks are very thorough, as all the machinery is checked, including the transport and lifting systems, and the necessary parts are cleaned, greased or replaced.
At Innova Group we have our own spare parts repository Warehouse, so we can offer an immediate Parts Replacement Service in our maintenance tasks. All parts are new from the supplier and include the warranty by the manufacturer by default.
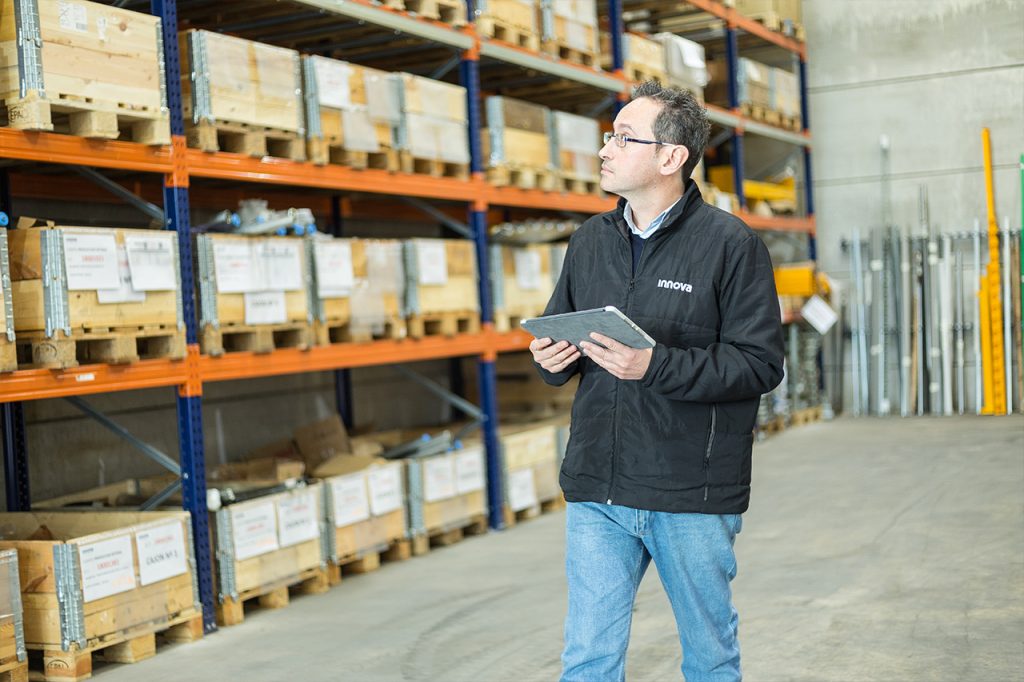
What happens after maintenance?
Once the maintenance has been carried out, the next one is pre-scheduled according to the established Plan. During the rest of the year our Support Service is operational to solve any incident that may occur in the packaging lines. Thanks to the Remote Connection Service they can detect and diagnose breakdowns in real time, anywhere in the world, helping to make the technical intervention faster than usual.
For Innova, Customer Support is one of the main pillars of our company, so we advocate for offering personalized technical services, of proximity and efficiency. The final objective is to accompany our customers throughout the life of their machinery and beyond.
Do not hesitate to contact our team for more information on our Maintenance Plan and Support Services. Do you join us?
#WeAreInnovaSupport
#WeAreYourPartner