Keys to automatic pallet strapping: more than a holding solution
Pallet strapping is undoubtedly one of the preferred packaging systems for securing boxes, packages and palletised loads. For many companies it is an indispensable and irreplaceable system, but which are the advantages beyond securing the load? Today we analyse the importance of strapping in the final packaging and the advantages of the automatic strapping system at the end of the line.
Is it necessary to strap the load?
The answer always depends on the product, its primary packaging and the handling it will have. But in general, we always recommend strapping a load that is very fragile and/or heavy or that has instability problems in being handled and transported.
In a factory with boxed or bundled product, it is always recommended to strap the load at different levels to ensure maximum support for handling:
- First strapping level: when we strap the heavy and/or fragile box or package to prevent it from opening.
- Second strapping level: when we strap the palletised load, i.e. we fasten and join the palletised product to the pallet, to guarantee its stability during transport. At this point, there are two basic types of strapping: horizontal pallet strapping (which serves to compact the load into a block) and vertical pallet strapping (which serves to secure the load to the pallet).
When strapping pallet loads, there are also systems to protect the load itself from the strapping application, such as edge protectors.
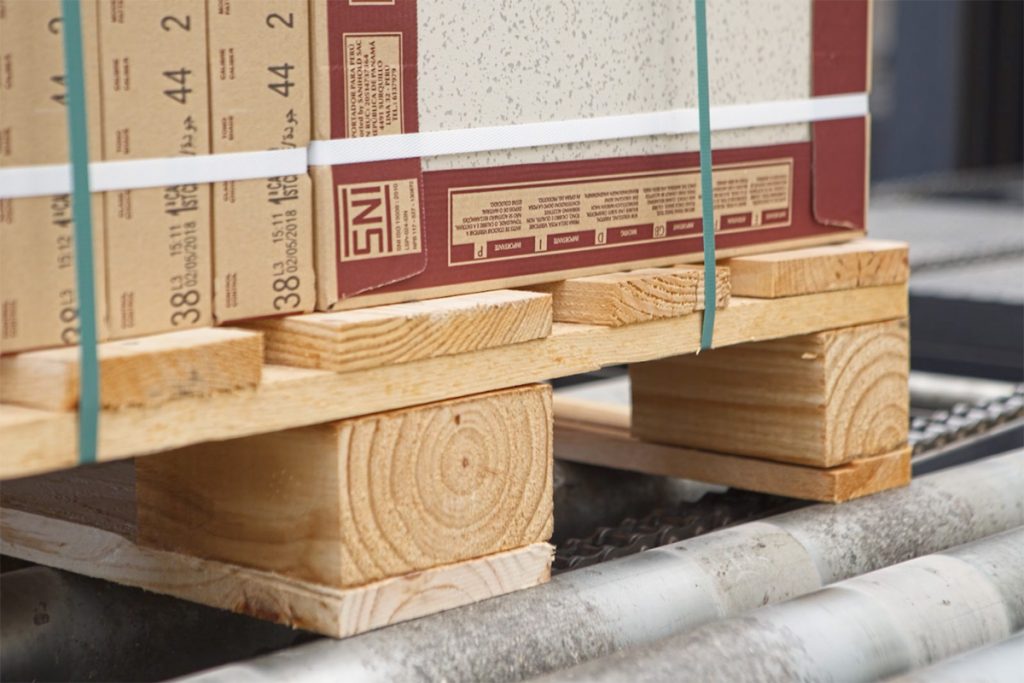
Can an automatic pallet strapping machine be replaced by other packaging systems? The generic answer is yes, although the results will not be the same as with strapping. Depending on the level of securing, it could be replaced by tape sealing (lighter loads) or film wrapping (heavier loads). Below we will explain the differences between securing a palletised load with strapping or with a pallet wrapping machine.
What are the differences in securing the load with strapping vs. wrapping?
In palletised loads, both pallet strapping and stretch wrapping systems can be used for the same securing purpose. However, depending on the product and purpose of the packaging, pallet strapping has clear advantages over the stretch pallet wrapping system.
- Wrapping System: Whether in its automatic or semi-automatic version (see our semi-automatic pallet wrapping machine), the film provides support and compaction of the lightest or most fragile loads. As a pallet wrapper, the film adapts to the contour of the load and does not exert as much pressure as strapping would. In the case of heavy loads, the application of the wrapper’s cord can also act as a substitute for strapping, providing more stability.
The big disadvantage of the stretch wrapping machine compared to the pallet strapping machine is the cost of consumables, which depending on the desired result can consume more film than the strap being used.
- Strapping system: As we have seen, automatic pallet strapping is the most recommended system for heavy loads, as it allows for a greater degree of securing. The tension of the strap can be adapted according to the type of load and dimensions of the pallet, as well as adjusting the number of straps. For long term storage, strapping is also more resistant to climatic conditions. If automatic pallet strapping is carried out by resistance welding, as in the case of Innova solutions, it also ensures a greater adherence.
The major advantage of pallet strapping over pallet wrapping is that it allows for the use of less consumables, thus contributing to lower costs and greater environmental sustainability.
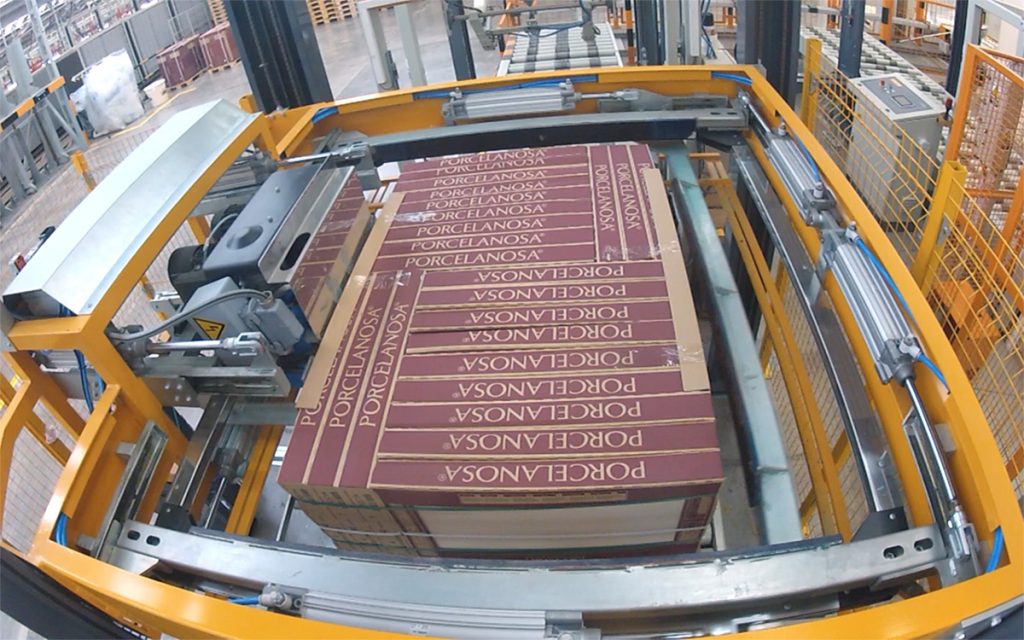
Pallet strapping systems: The advantages beyond strapping
We have talked about securing, but what other advantages does this system offer us in the packaging of our loads?
- Compaction of the heavy load:
Strapping is primarily used to form a more solid and compact load, especially for heavy and/or large loads. Good compacting with strapping will prevent the load from shifting or breaking during transport, even if it does not have additional packaging systems such as wrapping or stretch hood.
- Maximum safety and regulatory compliance:
Strapping ensures maximum cargo security during transport and handling, not only to minimise breakages and prevent losses, but also to comply with cargo stowage regulations, which require cargo to be strapped and/or wrapped.
- Better presentation of the palletised product
Automatic pallet strapping also provides an impeccable presentation of the load compared to other systems such as the pallet wrapping machine. Furthermore, the strapping can be customised according to the company’s corporate image with colours and printed logo, or even with transparent strapping to better show the contents of the product.
Our automatic strapping systems for the end of the line
Whether in the final palletizsing or packaging line, at Innova we offer automatic pallet strapping systems for the end of the line characterized by their robustness and safety in the strapping process.
Automatic horizontal strapping machine:
The Innova horizontal pallet strapping system has an anti-vibration portal frame composed of 4 pillars that offers greater robustness and safety in the strapping process than similar systems from other manufacturers. In addition, it also includes an automatic compactor to unify the load as block.
Automatic vertical strapping machine:
Compared to other manufacturers, Innova’s vertical pallet strapping system includes a 90º turning system for strapping in one or two directions, on 2 or 4 sides, to guarantee better load securing. This pallet strapping machine model also includes a displacement system to perform several strapping operations without moving the pallet, a very useful feature for unstable loads.
Automatic Box Strapping Machine
For the palletising line, we also offer a box strapping machine, which stands out for its efficiency, robustness and ease of use. Strapping is carried out by resistance welding and the strap tension can be adjusted according to the load. In addition, its robust structure with a strapping frame anchored to the floor provides greater stability in the strapping of the boxes.
In short, as we have seen, the strapping system is essential to guarantee the securing and safety of the palletised load during transport. At Innova we offer automatic, robust but versatile strapping solutions that adapt to the packaging and securing needs of our customers. Ask for more information without obligation or commitment, we will be happy to help you.
#WeAreInnovaTech
#WeAreInnova