Keys to the success of an Automatic Packaging Line project
How will my packaging project be carried out? How do I define packaging formats and types? Which consumables should I choose? How does the FAT test work? There are many issues related to an industrial project, specifically one of an automatic packaging line in which many aspects, different packaging systems, customer requirements, regulations, etc. are involved. From our experience with hundreds of end-of-line projects over the world, in today’s article, we will describe all the phases and aspects of a large-scale project such as an automatic packaging line.
We will analyze stage 1 of the packaging project, from its definition, through design, testing, manufacturing, and up to its installation and beyond.
Phases of the Packaging Line Project
- Packaging solution needs
- Packaging Project Evaluation
- Innova Lab: Packaging testing and Cost Analysis
- Packaging Line Engineering
- Packaging Systems Assembly
- Final tests and FAT (Factory Assembly Test)
- Installation and commissioning
- Support and Maintenance Services
1 Packaging solution needs
Whether it is a packaging system renovation, a new production plant project, or an end-of-line expansion, often a company contacts the end-of-line machinery manufacturer or integrator to define a new packaging project. At this stage, the customer may have a very clear idea of what is required for his line project or he may need the manufacturer’s consultancy.
2 Packaging Project Evaluation
The first stage is vital in the definition of the project since it is where all the aspects that the project requires are placed on the table. At Innova, for example, we carry out an exhaustive interview to gather all the main data of the project, such as, for instance:
- Project objectives (renewal, addition, new installation, etc.)
- Objectives of packaging systems (increased stability, savings in consumables, load protection, etc.)
- Information about current packaging systems (whether manual, semi-automatic, automatic or the types of systems used).
- Current consumable usage data
- Product type and load measures
- Technical data of existing production
- Facility data (factory measurements, connections and workflows, PLC system, etc.)
With the data provided by the customer, the first proposal of packaging systems proposed by Innova or requested by the customer can be made, which may already include a layout drawing with the plant drawing and an economic proposal.
3 Innova Lab: Packaging testing and Cost Analysis
Within the study of the automatic packaging line project, Innova includes two key services for the customer that few manufacturers offer:
Innova Lab: Stretch Hood and other packaging systems testing
On the one hand, we offer our Innova Lab test area to assess the suitability of the Stretch Hood system for the customer’s loads. Within this service, the customer can see the tests in person, or a video is made with the results.
The test is also used to define which type of Stretch Hood film is best suited to the product, as well as to include other additional systems if necessary (for example, if the product characteristics require additional strapping).
It is a test with a similar set of methods to those proposed by the EUMOS stability association: load impact test, tilt test, and lateral and frontal oscillation movement tests. These are simulations of the performance of the load during transport by land and sea.
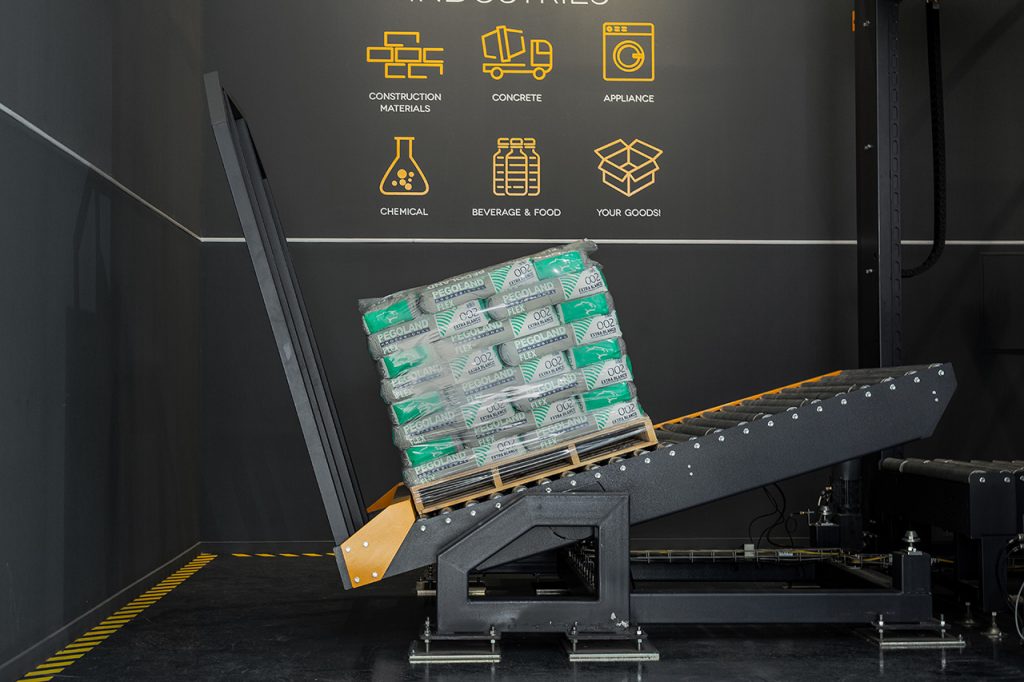
Savings and consumption analysis
Whether Innova Lab tests have been performed or not, our technical team determines which consumable would best suit the product to compare it with the consumables previously used. In this type of study not only the prices of consumables and amounts used per pallet are taken into account, but also other aspects such as energy used (in the case of systems that require gas), the labor force (in the case of manual packaging), etc.
From the consumption analysis we offer a comparison of real systems according to the customer’s case, and the results of savings and possible amortization of machinery investment, if the packaging project requires it.
In this aspect we also include consultancy on consumables, concerning the optimum features for the product, such as the type of Stretch Hood wrapping film that is most suitable, considering the grammage and stretching properties. We also offer eco-consulting on the recyclability of the consumable and its composition of recyclable materials.
4 Packaging Line Engineering
Once the proposal, testing, and analysis phase has been completed, the mechanical and electrical engineering teams design the packaging line that best suits the project requirements:
- Mechanical Engineering first designs the machines required by the project, depending on whether they are standard models or require modifications (load heights and measurements, extra safety elements, accessories, etc.). It then designs all the elements of the automatic line according to the space allocated in the factory: conveyors and connections with existing line and loading vehicles, packaging systems, fencing and safety accessories, etc.
- Electrical engineering, on the other hand, designs the entire electrical scheme of the line and the communication protocols and protocols. This part is vital as it is the one that guarantees the integration with existing equipment, loading vehicles, and other elements of the line such as the label printers. Thanks to a good definition of communications, it is guaranteed that the packaging process is carried out to perfection.
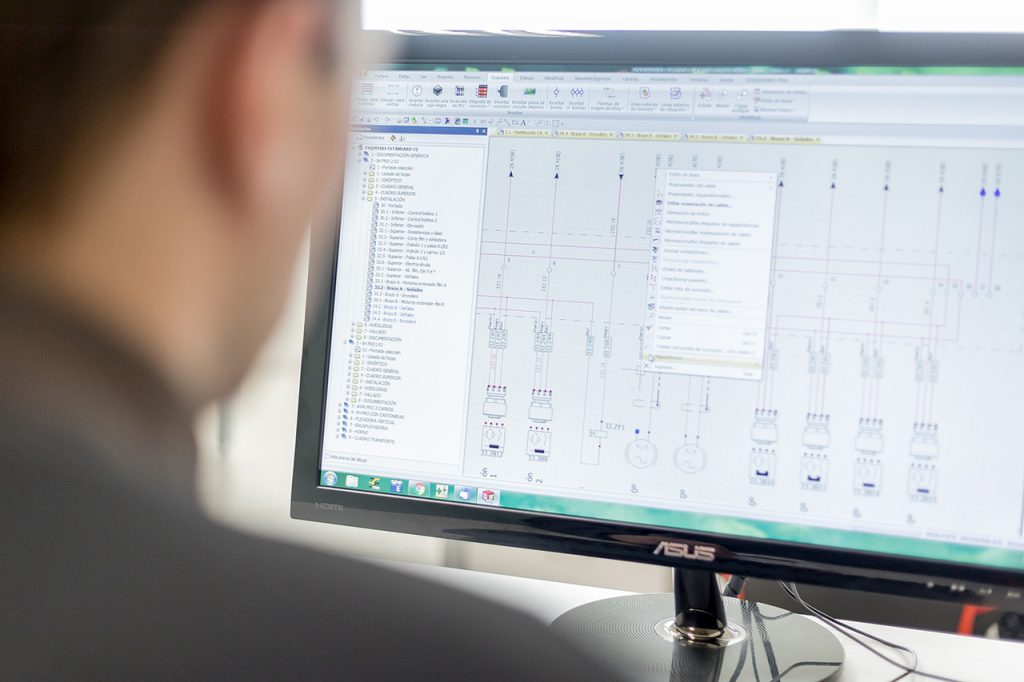
5 Packaging Systems Assembly
Once all aspects of the project have been defined and approved by the customer, the order is placed for all the elements that make up the new packaging line.
At Innova, we take care of every detail and that is why we use the Lean Manufacturing methodology for the manufacture of our machinery. Through control and quality monitoring panels, we can complete the manufacturing and assembly of the different systems and components without rework or delays.
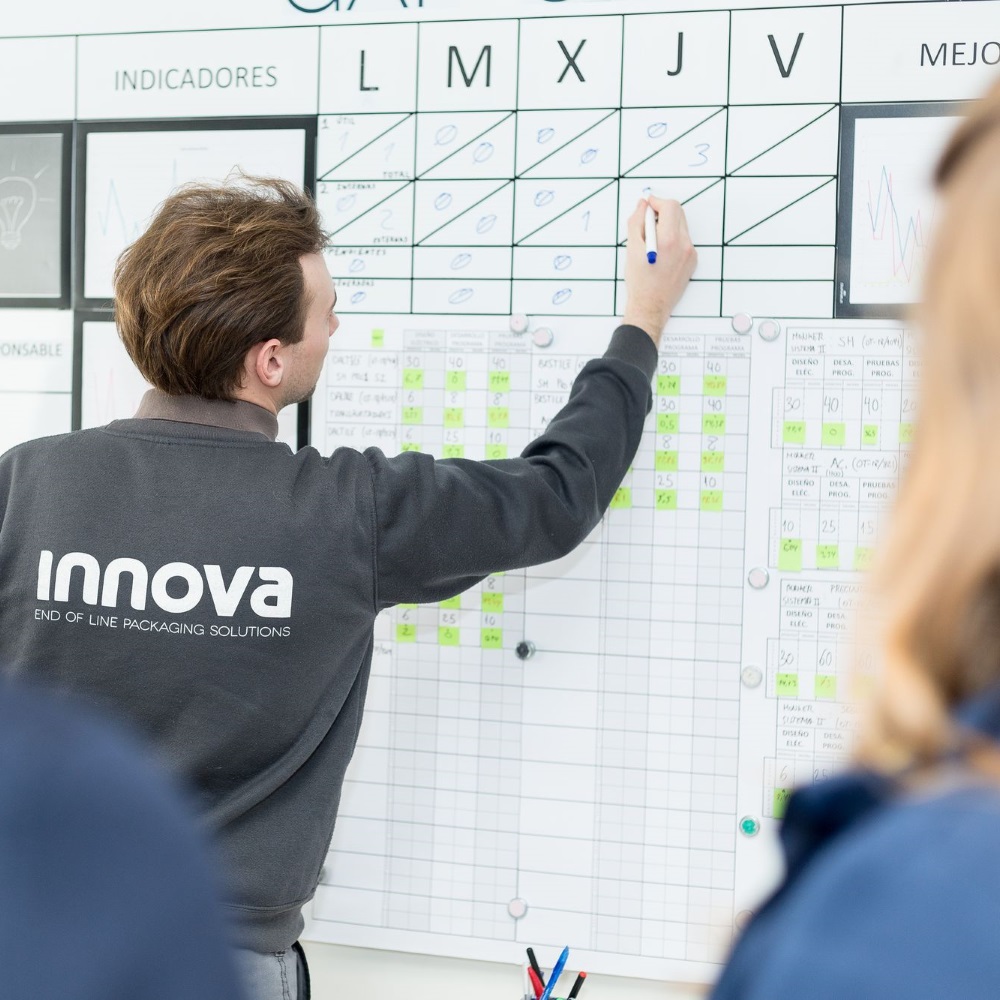
6 Final tests and FAT (Factory Assembly Test)
Once the machinery assembly is completed, it is set up in our factory to test that both the mechanical and electrical parts work perfectly. This is the moment of the final testing: usually, during several days, tests are carried out to check that the different pallet formats work correctly as designed. This test includes the so-called FAT (Factory Assembly Tests), which can be carried out internally or in the presence of the customer.
This is a vital stage and the one that guarantees a trouble-free installation at the customer’s premises.
7 Installation and commissioning
Innova’s technical team performs the installation of the machinery in the field with technicians specialized in this type of assembly. In addition to the actual installation of the machine and integration into the customer’s factory, the entire automatic line is put into operation, in which the machinery is retested with the specific load and production conditions.
Within the commissioning service of the line, a section is dedicated to the training of factory staff in charge of handling and supervising the line. At Innova, we also have training documentation in digital and printed formats.
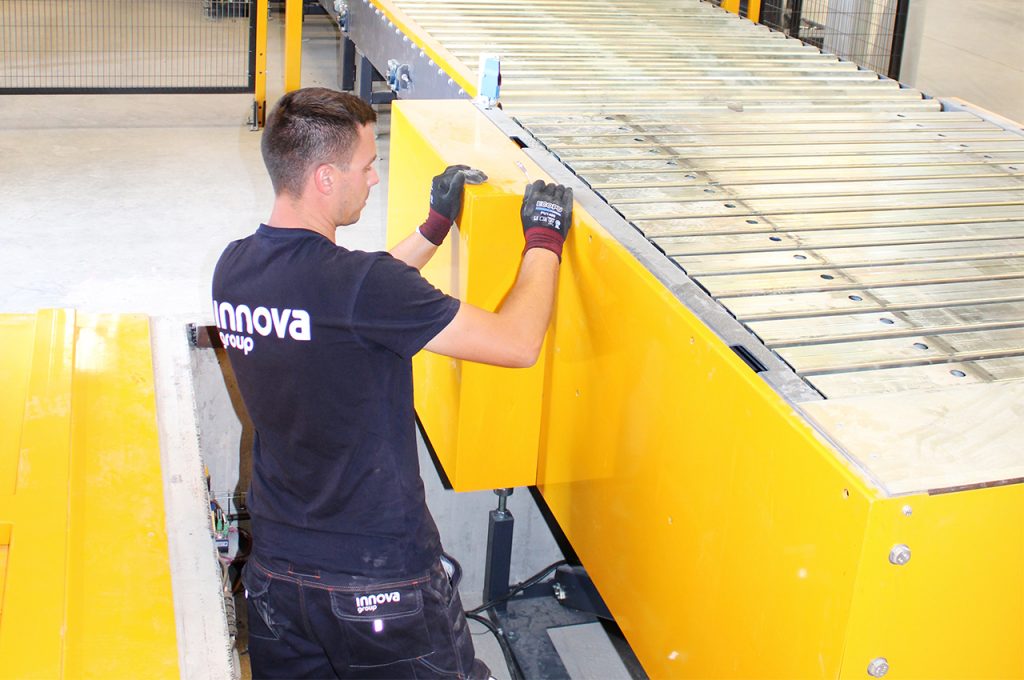
8 Support and Maintenance Services
The packaging line project does not end with its installation. For Innova is very important to accompany our customers in the life of their machines and beyond, so we strive to offer Technical Support and Maintenance Services of the highest quality. Whether in installations in Spain or around the world, we have a network of technicians specialized in support and troubleshooting. Through our central factories, subsidiaries, and official distributors we offer immediate technical service, preventive and predictive maintenance plans, spare parts service, remote access diagnostics, and much more.
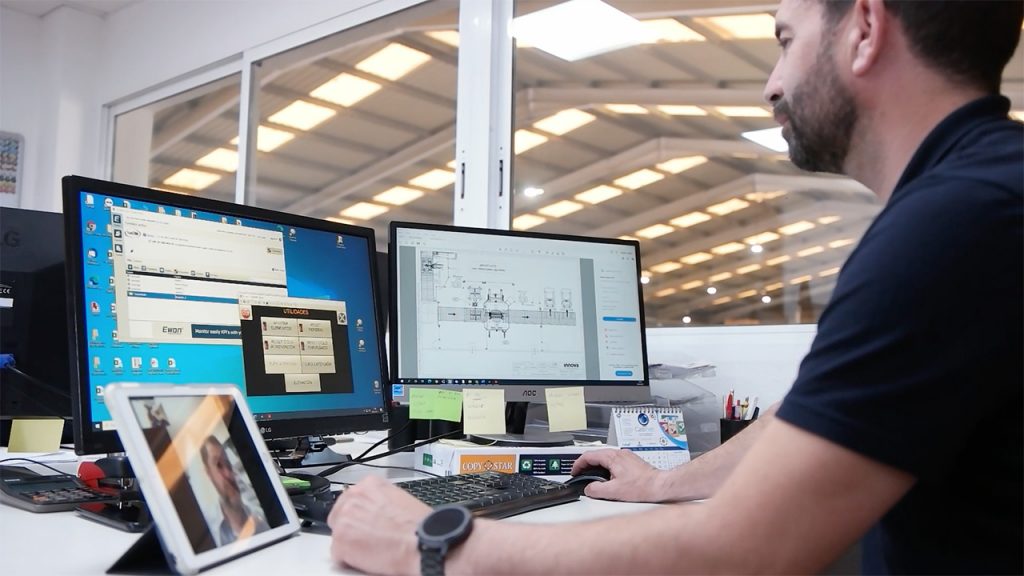
We take care of every packaging line project by offering all this support and spare parts service, but also of line expansions and renovations in the future.
As we have seen, a packaging line project requires many aspects and technical details. Having a manufacturing partner contractor specialized in the project is key for the customer not only to obtain the required results but also to exceed their expectations and objectives for the logistical improvement of their end of the line. At Innova, we can advise you in any of the stages or the whole project. Consult with our technical team without obligation, we will be happy to assist you.