PACKAGING LINE GUIDE: How to Prepare an End-of-Line Packaging Project
Installing a pallet packaging line in a factory is a complex project that requires thorough planning for its success. It is essential for the technical manager or technical director of the factory to understand the key aspects and the necessary preparations to ensure that the packaging project meets the expectations and the installation proceeds smoothly.
In this post, we will provide a step-by-step guide on how to define and execute a packaging project, as well as the preparations you need to make before and during the installation of the line. It is crucial to consider several aspects before embarking on a pallet packaging line installation to achieve the desired success.
Essentials to consider before defining the line project
For a customer who is considering installing an automatic pallet packaging line in his factory, it is essential to take into account a number of aspects to ensure the success of the project.
1. Analysis of packaging requirements and goals
In order to begin any packaging project, it is essential for the client to carry out a comprehensive analysis of their requirements and goals. This includes identifying the anticipated production volume, the nature of the products to be packaged, the necessary quality standards, and any other pertinent specifications. Some key aspects to consider:
- Products to be packaged: Identify the characteristics of the products to be packaged, such as size, weight, shape, and material.
- Production volume: Determine the number of pallets to be packaged per day, week, or month.
- Type of packaging: Choose the type of packaging and necessary systems, such as pallet wrapping, pallet strapping, Stretch Hood, etc.
- Integration with existing systems: Consider compatibility with existing load transportation, storage, or distribution systems.
2. Analysis and choice of machinery supplier
It is essential to conduct a thorough search and comparison of various pallet packaging line suppliers. We recommend selecting a reliable and experienced supplier who can provide tailored solutions to meet our specific requirements. Furthermore, it is crucial to compare prices, equipment features, and after-sales services to make an informed and wise decision.
Keys to choosing the supplier and packaging systems offered:
- Research: Investigate and compare different pallet packaging line suppliers, considering their experience, reputation, and customer service.
- Equipment selection: Select packaging equipment suitable for your needs, considering capacity, speed, features, and compatibility with your products.
- Testing and training: Request tests of the packaging systems with your products and ensure adequate training for the operating personnel.
3. Evaluation of space and existing machinery:
Before installing the pallet packaging line, it is important to evaluate the existing infrastructure in your factory. This includes considering available space, electrical capacity, environmental conditions, and any additional infrastructure requirements necessary for the installation and operation of the equipment.
For example, some technical aspects related to installation in your factory:
- Dimensions: Measure the available area for the packaging line, including ceiling height.
- Workflow: Evaluate the current workflow and the ideal location for the line without affecting other operations.
- Accessibility: Ensure adequate access for pallet entry and exit, as well as for the supply of packaging materials.
4. Design and layout planning
Once the pallet packaging line supplier has been selected and the existing infrastructure evaluated, it is important to design and plan the layout of the installation. This involves determining the optimal location for the equipment, as well as planning the material flow and layout of other areas of the factory to ensure efficient and safe operation.

5. Financial and budget planning:
Lastly, but not least, careful financial planning is essential, establishing a realistic budget for the packaging project. This involves considering not only the initial cost of equipment acquisition and installation but also operating, maintenance, and any other associated costs throughout the lifespan of the pallet packaging line.
What to consider when preparing the project budget?:
- Initial investment: Obtain quotes from different packaging line suppliers to compare prices and features.
- Operating costs: Consider maintenance, energy, packaging materials, and labor costs.
- Return on investment (ROI): Evaluate the return on investment time based on savings in labor costs, efficiency, and logistics improvement.
Preparations for the installation of the packaging line
After clarifying the project’s objectives, budget, and other details, the technical manager should consider various aspects and preparations to ensure a flawless installation. Some of the recommended preparations include:
- Project documentation:
In addition to collecting basic technical specifications, it is essential to consider all necessary documents:
- Technical specifications: Prepare a document with the technical specifications of the products, production volume, type of packaging, and available space.
- Area plans: Obtain detailed plans of the area where the packaging line will be installed, including dimensions, access points, and electrical connections.
- Detailed budget: Prepare a detailed budget that includes initial investment, operating, and maintenance costs.
2. Permits and approvals:
It is important to ensure compliance with current permits and other safety approvals in the factory:
- Construction permits: Obtain the necessary permits for the installation of the packaging line if required by local regulations.
- Safety approvals: Ensure compliance with industrial safety standards and obtain the necessary approvals from the appropriate authorities.
- Coordination with personnel: Coordinate the installation with the factory personnel to minimize the impact on existing operations.
3. Communication and monitoring:
It is absolutely crucial to ensure that there is continuous and effective communication with the packaging systems provider throughout the entire process.
- Effective communication: Maintain fluid communication with the supplier throughout the process, from equipment selection to installation and commissioning.
- Project monitoring: Establish a project monitoring plan with deadlines, milestones, and responsibilities to ensure compliance with the schedule.
- Testing and validation: Perform comprehensive testing of the packaging line once installed to ensure its proper operation and compliance with specifications.
Stages of a packaging line project
After defining the packaging line project and considering the documentation, the next step is to initiate the process of design, manufacturing, and installation. It is essential to work closely with the systems provider or manufacturer throughout this journey, as they are the experts who can guide us at each stage.
1. Project design:
To begin executing the project, it is important to develop the final project design. In this phase of machinery design, the engineering team is responsible for designing every detail of the systems and integrating them all into the final packaging line, both from a mechanical and electrical point of view.
2. Project closure and Technical Kick-Off:
At this stage of the project, all costs are finalized and documented. The final drawings and layouts are completed, and technical specifications of all packaging systems and machinery are confirmed. Finally, the order for all necessary components for the fabrication process is launched. This marks the closure of the project.
3. Manufacturing of packaging systems and other components:
The phase where the design becomes a reality is the manufacturing and assembly of the systems that make up the line. For example, at Innova, we manufacture and assemble the packaging line in detail with high-quality components and advanced technology, adapted for Industry 4.0.
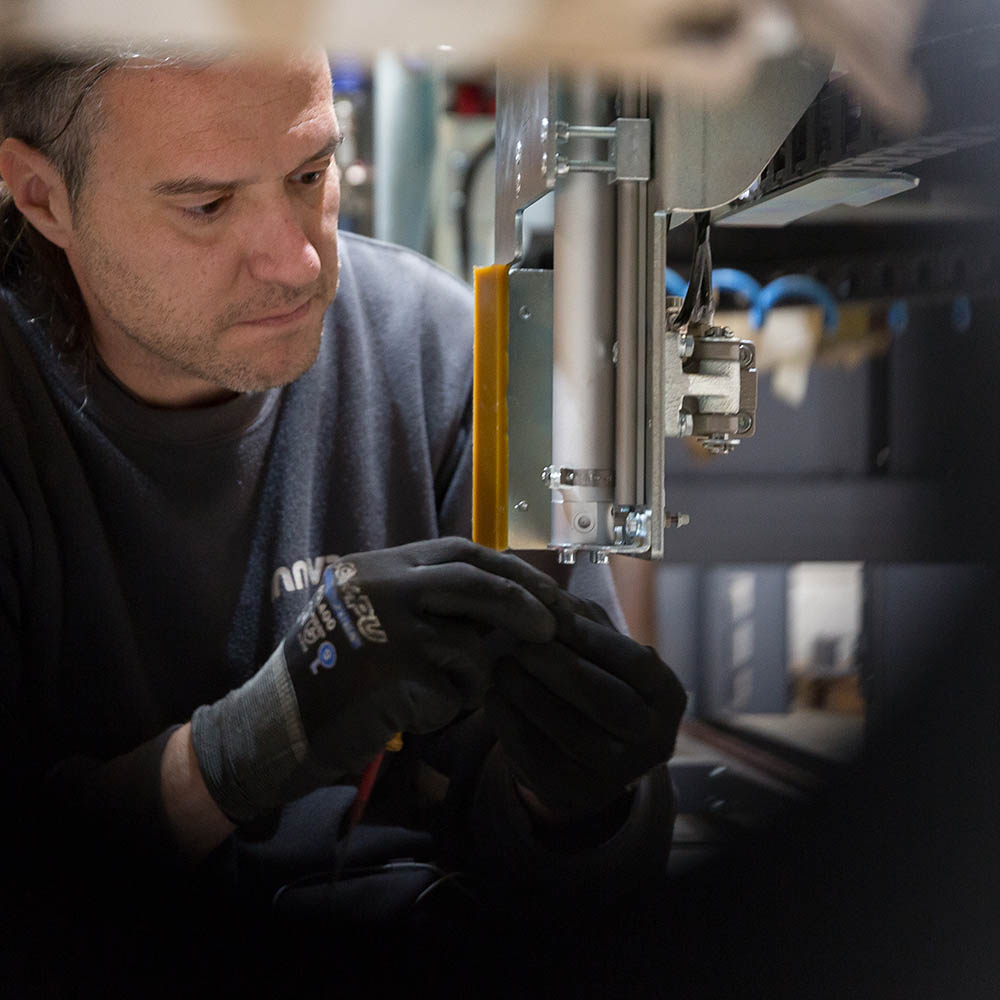
4. FAT Testing (Factory Acceptance Testing):
Before installation on-site, FAT tests are conducted to verify the proper functioning of all packaging systems and components. During these tests, real operating conditions are simulated to ensure that the packaging line meets all previously defined specifications and requirements. This includes performance, safety, and final packaging quality tests. It is crucial to carry out these tests in collaboration with the supplier to ensure that the line is ready for installation on-site.
5. Installation and commissioning:
Once the FAT tests are completed satisfactorily, the installation of the packaging line in the client’s factory begins. During this process, the installation team will work closely with the factory personnel to ensure a smooth installation. Once installed, commissioning is carried out, where final adjustments and last-minute tests are performed in the factory to ensure the optimal operation of the line.
6. Personnel technical training:
After the comissioning and start-up of the packaging line, it is essential to give a technical training to the staff. The training should include guidelines on how to operate and maintain the packaging line securely and competently. The supplier can provide tailored training programs for operators, maintenance technicians, and supervisors, ensuring that they have comprehensive knowledge of the equipment operation.
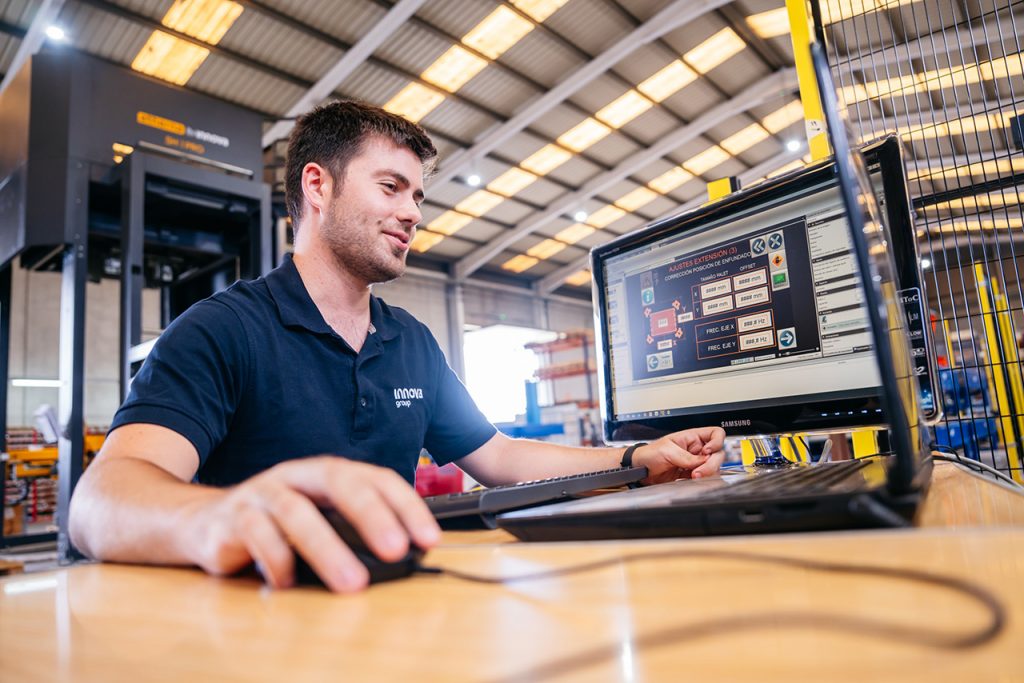
7. Technical Service and Maintenance Plans:
Finally, technical service and maintenance plans are established to ensure the continuous and optimal operation of the packaging line throughout its lifespan. These plans may include scheduled preventive maintenance services, remote technical support, and access to spare parts. It is important to maintain open and continuous communication with the supplier to resolve any issues that may arise and ensure prompt and effective technical support when needed.
By following these steps, the client can ensure that their pallet packaging line project is implemented successfully and that the line operates efficiently and reliably to meet their production and packaging objectives.
In conclusion, adequate preparation is crucial for the success of a pallet packaging project. By following this guide, you can ensure that your line is installed and operates efficiently, meeting your business needs and objectives. At Innova Group, with over 20 years of experience and hundreds of packaging line installations worldwide, we can advise you in detail on each phase of your project. Do not hesitate to contact us without obligation; we will be happy to assist you.