Reasons to change from pallet Heat Shrink to Stretch Hooding
In the context of the energy crisis, rising prices, high market demands, regulations, and sustainability objectives… it is increasingly important to review our end-of-line processes. While many manufacturing industries are looking for energy alternatives, others are choosing to renew their systems and rely on more advanced technology with more efficient packaging systems with lower consumption.
At this point, many manufacturers consider switching from shrink wrapping technology to more efficient alternatives such as the Stretch Wrapping or Stretch Hood system. In fact, the pallet shrink wrapping system is less and less demanded being only requested by industries in which the shrink wrapping of their pallets is necessary. At Innova, for example, customer requests for this technology now represent only 2%.
In today’s article, we look at the reasons for changing the shrink hood system, and the advantages of its current replacement, the Stretch Hood system.
5 reasons for the change of system
The heat shrink system has fallen into disuse due to aspects related to its energy use and the installation of the machinery itself:
1. High energy consumption
The main argument for the change is the high energy usage, as it usually uses a gas oven to shrink-wrap the film on the pallet. Even with electric shrink wrapping models, the power consumption is higher compared to systems such as the Stretch Hood, which employs highly efficient motors, specifically in the case of Innova’s Stretch Hood.
2. Higher maintenance
Due to the installation of the shrink oven itself (either gas or electric), the shrink-hooding system requires more maintenance for safety reasons. Because it handles very high temperatures, the oven requires periodic inspections and more spare parts than a simpler electrical system such as Stretch Hood. In addition, many manufacturers provide this system separated into two stations which translates into two components or even separate machines for hooding and shrink hooding, leading to more mechanical maintenance.
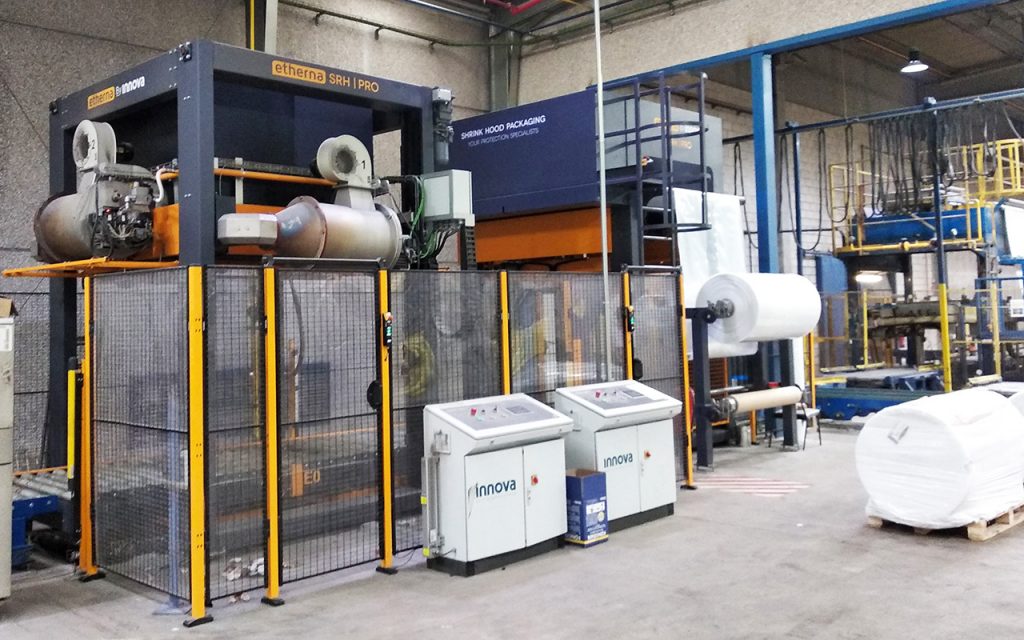
3. Gas installation
In most heat shrink systems it is necessary to have a gas installation and supply in the factory. In many industries, such as ceramics, this is not a problem, but in other manufacturing industries, installation and maintenance is required exclusively for the pallet packaging system.
4. Installation safety
The gas component also leads to reduced machine safety, as small combustions can occur on the goods being wrapped. Depending on the characteristics of the product (e.g. chemical composition), it can even be a fire and explosion hazard in the factory. It can also be a safety hazard to the staff that works on the line and has to do maintenance on it.
5. Damages to the product
Eventually, this packaging system may cause occasional damage to the product itself. Some of these may be tears where rain or humidity can seep in, plastic sticking to the shrink film, or even deformations due to the application of heat.
Why change from Heat Shrink to Stretch Hood?
While the reasons for the change may be clear, how to choose which technology to go for? There is a trend in the factories to replace Heat Shrink with the new Stretch Hood wrapping system, as it provides greater advantages with an improved finish:
Lower energy consumption and sustainability
Stretch Hood not only consumes less, as it does not use gas but also incorporates more efficient motors and electrical technology. It also reduces film consumption, as the Stretch Hood film is usually much smaller and lighter in size and weight than the Heat Shrink film. The Stretch Hood is therefore a more sustainable system, as it reduces CO2 emissions, uses less energy, and reduces the amount of plastic used in wrapping.
Increased productivity
By avoiding the stage of shrinking, the Stretch Hood is twice as fast in the hooding process. It also has ultra-fast forming and hood application systems for high production rates. In the case of Innova’s systems, for example, a Stretch Hood typically wraps between 80-120 pallets/hour while shrink hoods can wrap between 40-50 pallets/hour.
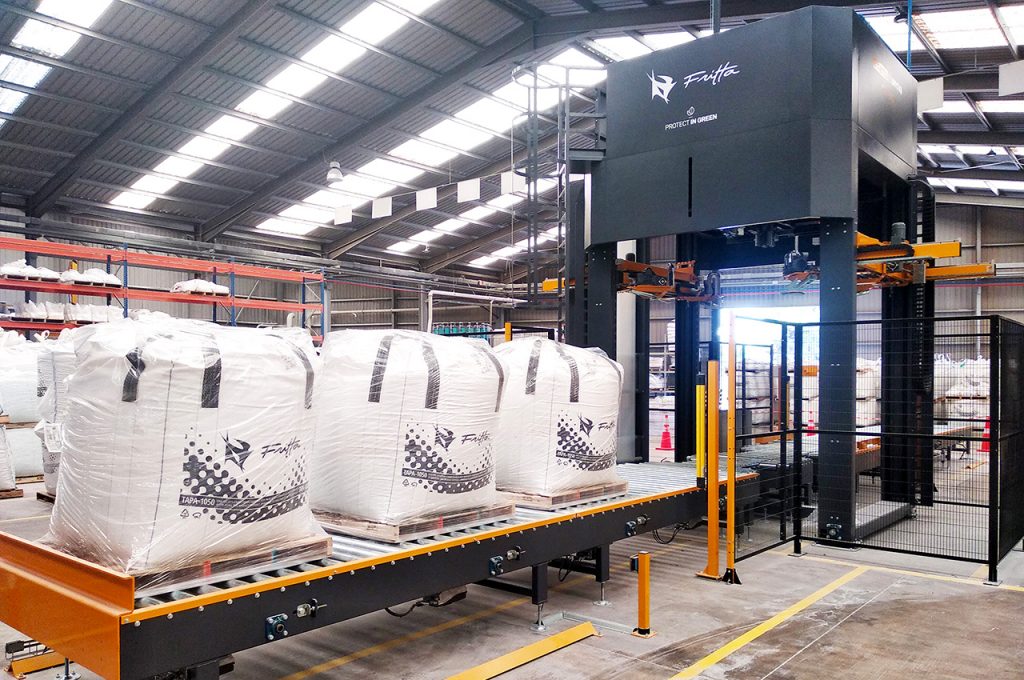
Improved protection results
Stretch Hood not only offers a wrapping result similar to shrink hooding but improves it: With only one hood (using less film than stretch wrapper and termo shrink) it fully protects the product. The Stretch Hood film is a highly stretchable film with puncture and tear-resistant properties that fully adapts to the load. Thus, there are no tears from the heat or stretch wrapping layers, leaving the stretch hooded load completely sealed.
More advanced and secure technology
The Stretch Hood system is a newer technology that saw the light of day some 25-30 years ago and is therefore in continuous development to adapt to the needs of the market. The new Stretch Hood systems are already being developed with modular and simpler mechanics, decentralized electronics, high-efficiency motors, and 4.0 communication components for a safer process. Investing in Stretch Hood is undoubtedly a commitment to new packaging technologies.
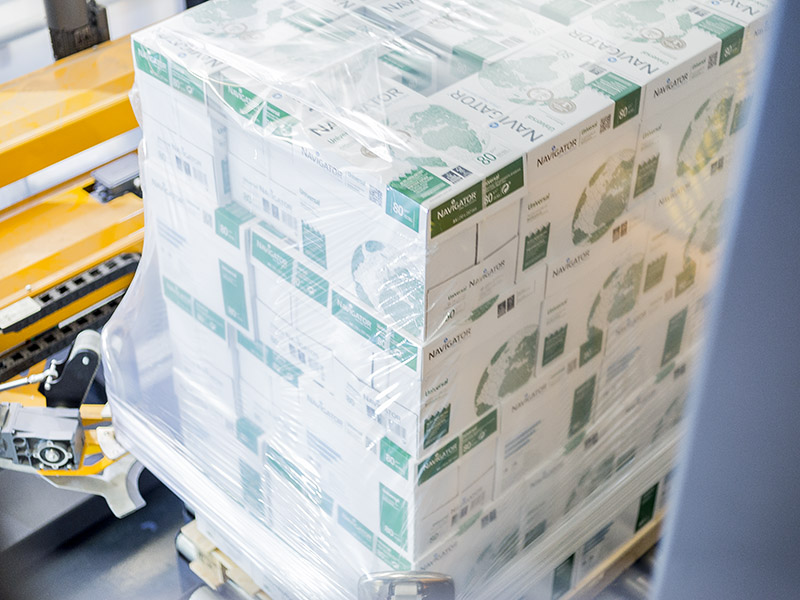
Higher quality of wrapping
Last but not least, Stretch Hood provides an excellent, flawless presentation of the stretch-hooded load. No creases or wrinkles typical of shrink wrapping and a more transparent packaging because it uses films with a lower thickness than shrink film. The presentation finish is an advantage sought by many companies with palletized products at the point of sale, as it offers high added value.
Paying off the change in less than 1 year
It seems that replacing a complete machinery installation may be costly, but considering a change from Heat Shrink to Stretch Hood, the energy and consumable savings are so high that the investment could be paid off in less than 1 year. According to the calculation made by Innova based on the type of product, production, cost of consumables, and other secondary expenses, the change of system can be amortized in an interval of 6 months (in cases of high energy consumption and shrink film) and up to 2 years.
This is without taking into account the many maintenance requirements of an old heat shrink hood system that can be avoided with a new system.
This aspect is a decisive argument for many companies that hesitate to change the system, which, although it works and fulfills the packaging objectives, is too costly and inefficient.
At Innova, we have extensive experience in packaging system changeover projects, with hundreds of end-of-line installations that have replaced Heat Shrink with Stretch Hood. We also offer film usage and amortization studies to prove the benefits of opting for a more efficient technology such as Stretch Hood. Do not hesitate to contact our Technical Sales Team for specialized advice on your product without any obligation. We will be pleased to assist you.
Ready for the change?