Technical Comparison: Innova Automatic Wrapping Machines, Ring vs Rotary Arm
Which automatic wrapping system is best suited for my product and load? Do I need a ring, arm, or turntable wrapping system? Which one offers higher productivity? When choosing a type of automatic wrapper, customers often ask many questions, as differences in wrapping technology can be key to the final packaging result. Undoubtedly, automatic stretch wrapping systems are among the most widely used and popular packaging solutions, but few people truly understand the differences between the various types of wrapping machines.
Today on the blog, we’ll analyze the most commonly used wrappers on the market, specifically comparing Innova’s systems: the automatic ring wrapper and the automatic rotary arm wrapper. Below, we review their features, advantages, and key differences to help you make the best decision based on your logistical needs.
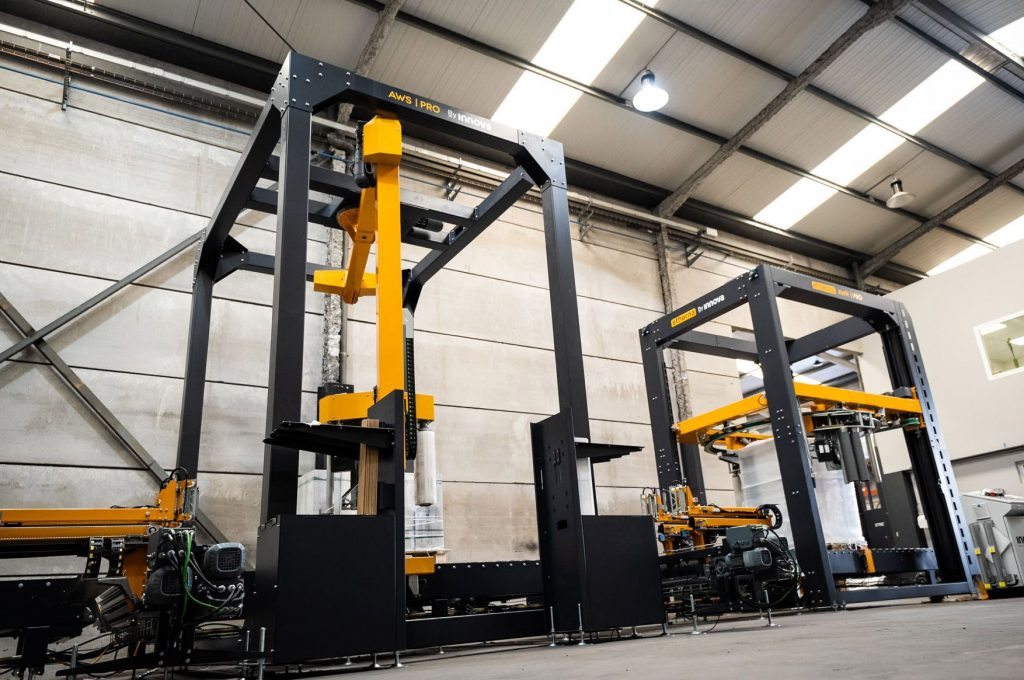
Rotary arm or ring wrapping?
The result may look the same, but the method is not. Even though both wrapping systems aim for the same outcome, the technologies are quite different. In broad terms:
- With the rotary arm wrapper: The film is applied by a rotating arm that moves around a stationary load. This arm can be mounted on a two- or four-column structure and can even be used in semi-automatic systems.
- With the ring wrapper: The film is also applied in a rotary motion, but in this case, the ring itself applies the film. As with the rotary arm, the structure can be either two or four columns. When installed on a four-column frame, the assembly (ring + film carriage) is mechanically more stable, allowing for greater robustness, safety, and the ability to reach higher speeds, as we’ll see later.
Common features between the rotary arm and ring systems
Although both wrapping systems are technically different, they share several characteristics that make them highly efficient and adaptable to a wide range of industrial needs:
- Fully automated: Both machines are designed to be integrated into automated production lines, enabling efficient and continuous wrapping without manual intervention.
- Compatible with multiple industries: Thanks to their adaptability, these wrappers are the ideal solution for industries such as food, pharmaceuticals, chemicals, ceramics, logistics, and more.
- Elastic cord system: The wrappers include a reinforcement cord system that provides additional load containment, similar to strapping, improving load stability during transport and storage.
- Option to include two carriages: Both wrappers allow for increased wrapping speed by incorporating a dual carriage system in their structure.
- Load protection and securing accessories: For protection purposes, they can include an automatic top cover applicator system to prevent damage from external elements. Innova’s wrapping machines also include a corner protector applicator system to secure and standardize loads—an accessory few manufacturers offer. For load securing, they are equipped with a top press to stabilize light or unstable loads, offering greater safety and stability during wrapping.
- Wrapping of ultra-high loads: The modular structure of these wrappers allows them to adapt to different load heights, ranging from 500 mm to 2,400 mm.
- Automatic pallet height detection: Automatic wrappers include a height detection or pallet reading system using a photocell, which allows them to wrap loads of different sizes and formats without requiring pre-programming. This system is already included in Innova’s standard models.
- Lower stretch film consumption: Both machines are designed to reduce consumable usage thanks to their electronic packaging technology with torque control, advanced wrapping programming, and a film pre-stretch system of up to 300%, allowing for optimal use of the material.
An important point to highlight is that both solutions are part of a modular and scalable machinery range, which can be integrated with other end-of-line systems such as Stretch Hood or strapping systems.
Advantages of Innova’s Ring Wrapper vs Rotary Arm Wrapper
1. Increased pallet/hour productivity
One of the most notable advantages of the ring wrapper compared to the rotary arm wrapper is its higher wrapping speed, thanks to the ring’s structure and technology. The rotary arm wrapper can process up to 80 pallets/hour, while the ring wrapper can wrap up to 100 pallets/hour with two film carriages, thanks to the stability provided by its belt-driven traction system.
The option to include two film carriages allows production to continue without interruption if one film roll runs out or breaks. In such cases, the system can keep running with a single carriage, avoiding a complete production stop. Additionally, if a wrapper is purchased with future productivity growth in mind, it is easier to add an extra film carriage to a ring system than to add a second arm to a rotary arm wrapper.
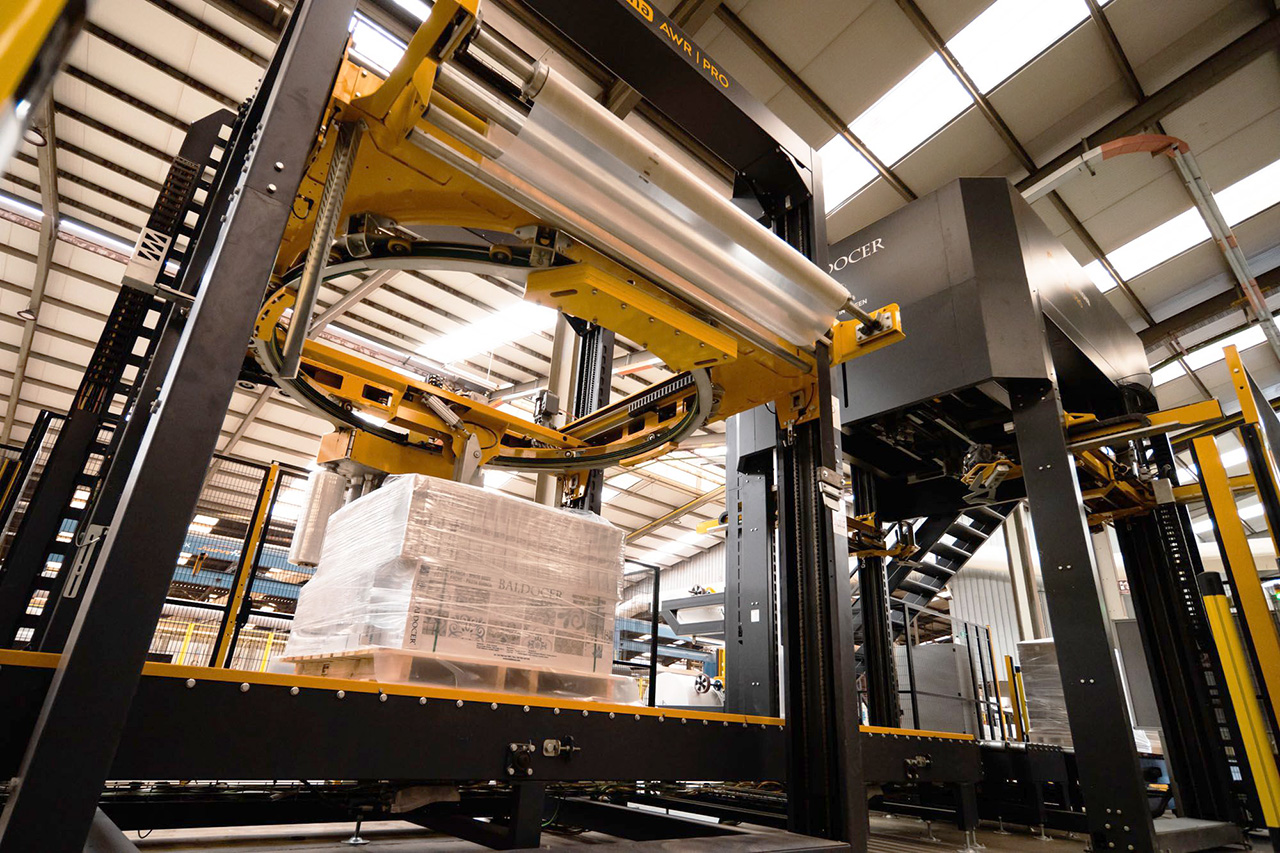
Moreover, the ring wrapper maintains production speed even when accessories are added. In the rotary arm wrapper, each operation requires a pause to reposition the arm safely before continuing the wrapping cycle. In contrast, the ring wrapper is much less affected by these pauses. When accessories like the top cover applicator or corner post applicator are included, the ring system allows coordinated movements with other elements entering and exiting the wrapping zone, without the need to pause the cycle.
2. Independent start and end points for the wrapping cycle
Another advantage of the ring wrapper is the flexibility in the start and end positions of the wrapping cycle. The start of the cycle in a ring wrapper is more versatile and customizable than in a rotary arm wrapper, which must always begin and end at the base of the pallet. In contrast, the ring wrapper can start and finish the cycle at the base, top, or even the middle of the pallet.
3. Wireless technology for a better wrapping process
Innova’s ring wrapper features an industrial Wireless communication system, a technology rarely used by other manufacturers, which enables connection between the machine’s fixed and rotating components (such as the PLC and rotating film carriages) without the need for physical wiring.
This system offers greater communication reliability by eliminating failures caused by cable or conductor rail wear, reducing downtime and stoppages, enabling faster and easier setup, and providing high efficiency and precision. These advantages position Innova’s wrapper as one of the most advanced, safest, and most sustainable on the market, ready for high-demand environments and aligned with Industry 4.0 standards.
Advantages of the Rotary Arm Wrapper vs Ring Wrapper
1. Lower maintenance
One of the most valued aspects in the industry is the reliability and durability of equipment. In this regard, the automatic rotary arm wrapper stands out for its reduced number of moving parts, which directly translates into easier maintenance.
Since it has fewer wear-prone components compared to the ring system, maintenance is simpler, less frequent, and therefore more cost-effective due to lower operating expenses. This mechanical simplicity also results in a lower risk of breakdowns, increased uptime, and a longer service life for the machine.
2. Wrapping with a firm, clean finish and no thermal risks
Another major advantage of the rotary arm wrapper is its ability to complete the wrapping cycle without using heat-sealing or gluing systems. Through a tying system, such as Innova’s patented ROPE GRIPPING finish, the rotary arm wrapper can complete the cycle without the need for heat application. It also avoids the ongoing maintenance typically required by thermal sealing systems.
3. The most energy-efficient automatic wrapper
Innova’s rotary arm wrapper is one of the most energy-efficient and sustainable machines on the market, as it incorporates low-energy consumption components and motors, along with the previously mentioned pre-stretch technology to reduce film usage.
4. Techlite version
In terms of both efficiency and sustainability, Innova also meets market demand with the new Techlite model, a lighter and more efficient rotary arm wrapper that reduces the machine’s carbon footprint and saves space on the production floor.
In conclusion, both the automatic ring wrapper and the rotary arm wrapper offer highly efficient solutions adaptable to different industrial needs. The choice between the two will depend on the type of load, required production speed, and the specific conditions of the packaging line.
With over 20 years of experience and hundreds of packaging installations worldwide, Innova offers personalized guidance to support your project. Contact our technical team to evaluate which type of wrapper and features best suit your product and business.