Which are the essential Safety Accessories in an Automatic Pallet Packaging Line?
An automatic packaging line is not only composed of the packaging systems with their respective conveyors but also includes numerous automatic safety elements and communication accessories, such as perimeter barriers, signaling, measuring systems, etc. These safety elements and accessories not only serve to comply with regulations but are key to improving machine performance, avoiding accidents and stoppages, and providing a more fluid packaging process.
In today’s article, according to Innova’s experience in a multitude of packaging lines, we will outline the components, accessories, safety, and communication elements that an automatic packaging line must incorporate as well as others that are usually recommended.
Which safety accessories are required in an automatic line?
We refer to safety accessories concerning those mandatory or optional elements that ensure the communication of errors and prevent accidents. This is the case with perimeter safety barriers and of the machinery itself, safety signaling, but also of other electronic communication systems.
In Innova’s packaging projects, some of these systems are automatically incorporated into the automatic packaging line, after defining the type and location with the customer. While others are proposed or recommended according to the client’s objectives in the packaging project.
Mandatory safety elements
According to international work safety regulations, certain elements must be included in a packaging line or machinery installation:
1. Safety barriers
At Innova we offer two types of security barriers: in fenced format or with photocells:
- Perimeter Fencing: All of our automatic packaging machinery is enclosed within an enclosure of physical security fencing with security access gates.
- Safety barriers with photocell sensors: All our packaging systems include photoelectric sensors in certain areas that need to be accessible to ensure maximum protection for people. For example, in the Stretch Hood system, the film reel area is equipped with a photoelectric sensor for easy access. If a safety zone with a photoelectric signal is accessed during machine operation, it will trigger an alarm and stop the machine for safety reasons.
Photocell barriers can also be used as a substitute for perimeter fencing depending on the packaging project and customer requirements.
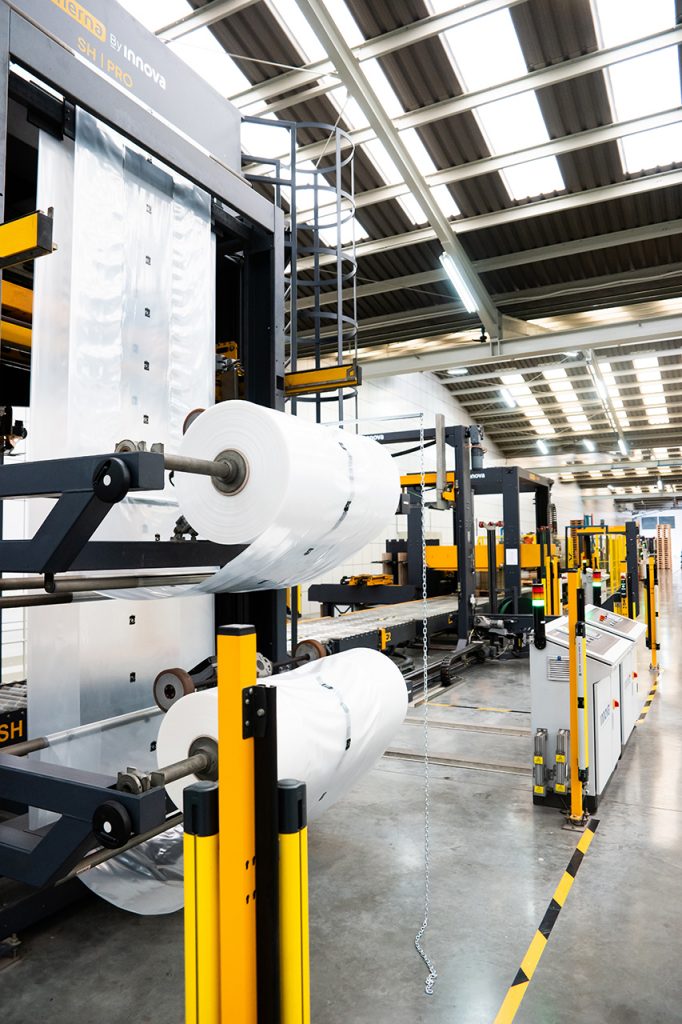
2. Security perimeter access:
Innova’s installations include secure access systems to the safety zone of each of the machines that are part of the line. These access control systems include a keypad device with:
- Emergency stop safety pushbutton
- Access request key
- Reset luminous push button
- Cycle start luminous push button
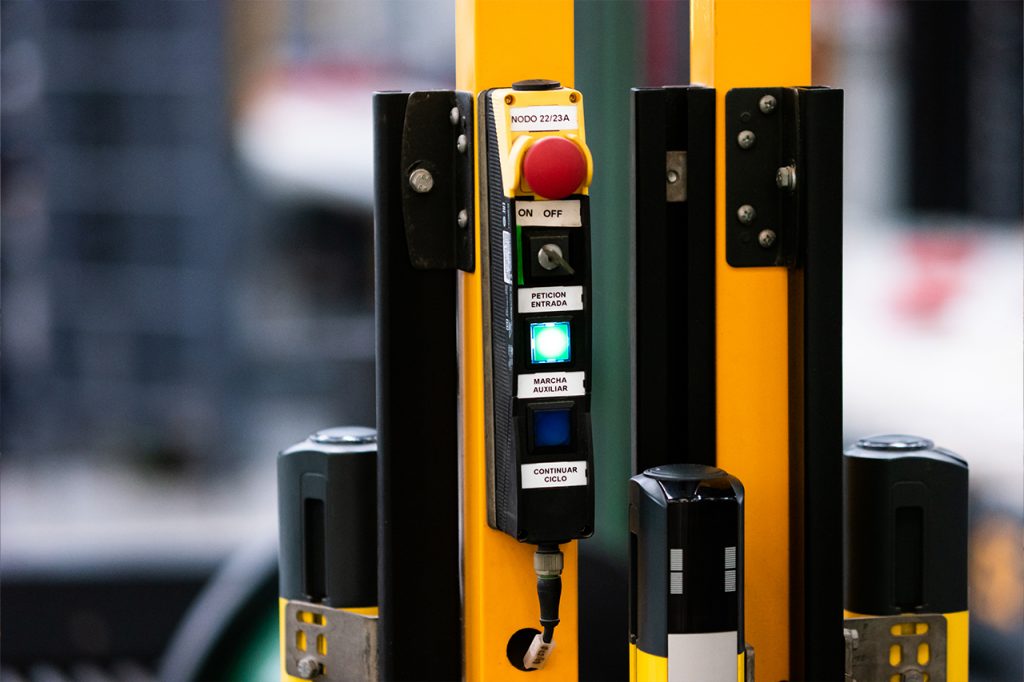
3. Safety signage
Another mandatory and essential element in an automatic machinery installation is acoustic and optionally luminous signaling. Any technical emergency anomaly is signaled acoustically and optionally luminously using luminous emergency beacons, to prevent danger to the physical integrity of the worker. Therefore, the most common signaling systems are:
- Acoustic signal
- Luminous beacon (optional)
4. Safety shutdown system
Our automatic systems include a safety PLC that simplifies the installation, avoids manipulation in the safety, and achieves a more versatile system. This special safety system is in charge of shutting down the power of the active elements in case of failure or emergency.
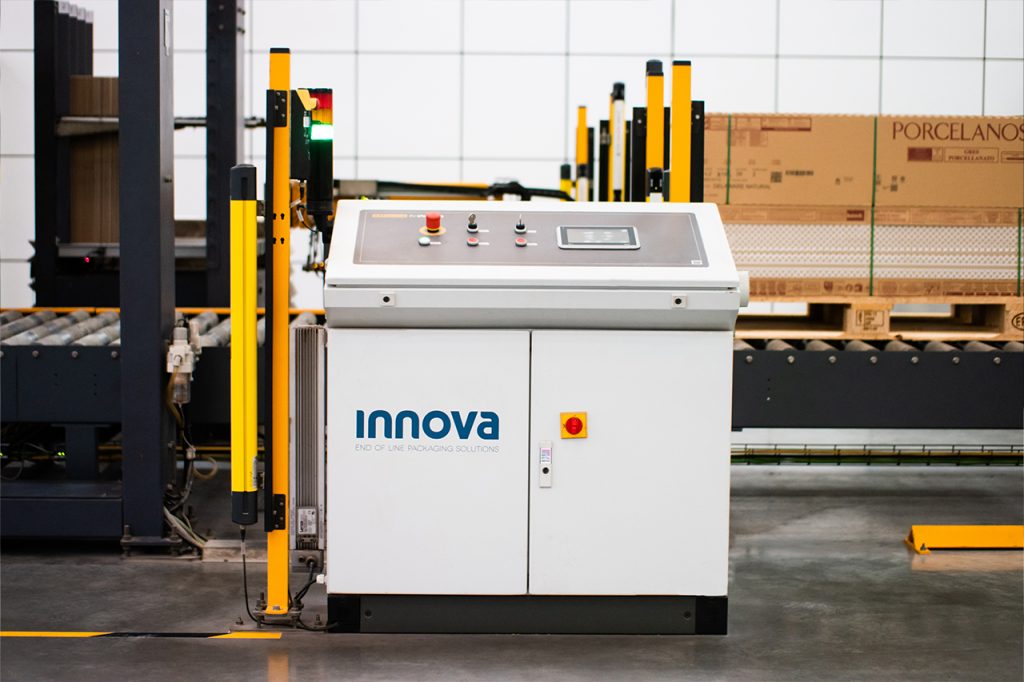
Safety elements of the machinery
The packaging machinery has its safety systems that prevent that certain actions do not constitute a danger to personnel or the installation itself. In the case of Innova, we have a safety PLC dedicated to this purpose, in addition to internal safety systems to prevent moving parts from falling.
Innova’s internal machinery safety system
Innova’s packaging machinery has internal anti-fall safety systems for moving parts of the machine that are activated in the event of an emergency, electrical failure, or power failure. When the anti-fall system is activated, mechanical safety cylinders are locked to the guide attached to the machine chassis. This is a very useful system not only in case of failure or accident but also to perform the maintenance of the machine safely.
Alarms and warnings communication
The control panels of the packaging lines display machine alarms and warnings for resolution by the factory staff or contact to Innova’s technical service. Thanks to Innova’s remote access, breakdowns can be viewed and resolved on screen. Our team can remotely access the alarm log to perform troubleshooting and generate machine performance reports.
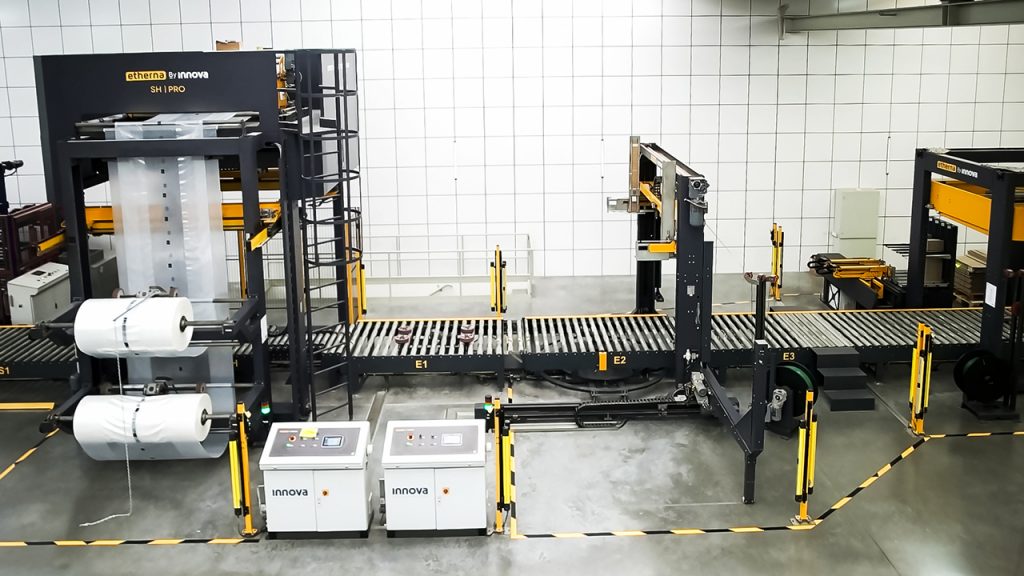
Optional communication systems
In addition to the safety systems as such, we also recommend, depending on the project, other communication accessories that provide additional data about the merchandise being packaged (such as the type of format, measurements, weight, etc.) to improve the packaging process.
Gauge control system
This is a pallet load height detection system for real-time format detection on the packaging line. The gauge control measures the load and sends the collected information to the corresponding packaging system, which based on the information will perform the packaging cycle according to the detected format. The information collected by the gauge control can also be sent to the customer’s logistics management system for its control.
This type of control also serves to detect possible protruding packaging or defective finish of the cargo, which also turns it into a safety communication system.
Pallet weighing system
It consists of a load weighing measurement system that can be included before and after the packaging process. In Innova’s line projects, the weighing accessory consists of a scale with 4 weigh cells installed on the legs of the line’s roller conveyor.
The pallet scale system transmits the weight information in real-time to all systems to which the packaging line is connected, such as the logistics ERP and/or the labeling system for logistics management label printing.
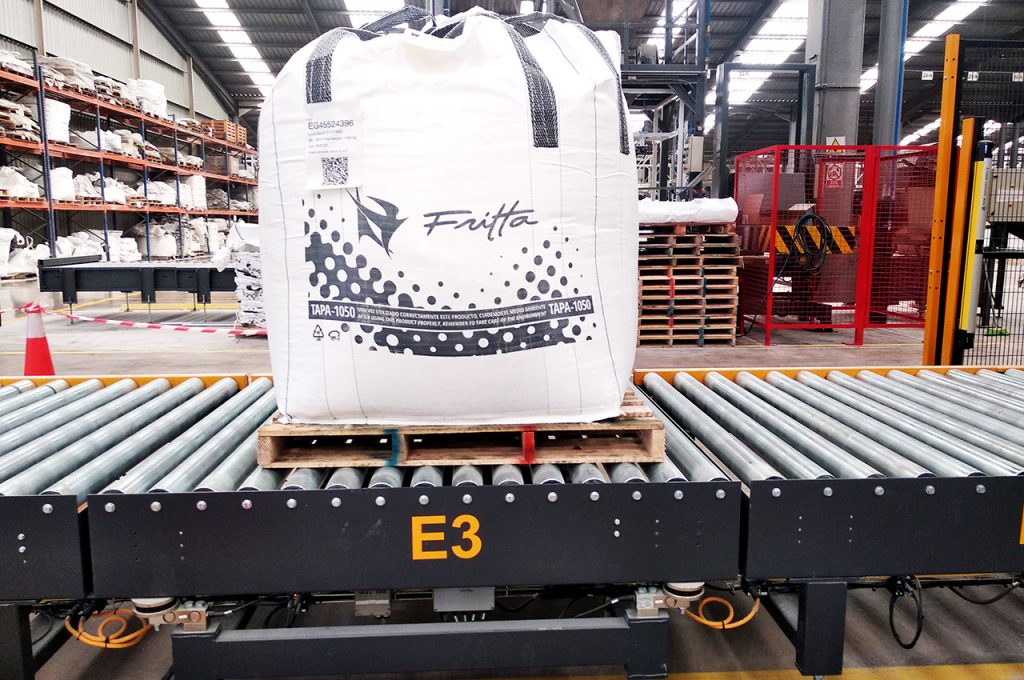
The location of the weighing system is determined according to the customer’s objectives to know this information before and/or after packaging. This is a very useful accessory to comply with container weighing logistics regulations, helping to provide accurate information about the load in an automated way.
Ultimately, it is important to know all the elements and safety systems that integrate a packaging line. At Innova, we adapt the safety systems and measuring components that your packaging line needs. In addition, our technical team helps you to comply with international regulations, such as the Safety at Work Act, Freight Transport Regulations, etc. Do not hesitate to consult with our team for any technical questions or packaging projects without obligation.