Baldocer commits to the latest packaging automation technology with Innova Group
The best protection for their ceramic pallet, improved transport stability and a customized packaging for their palletizing needs. These were some of the objectives that Baldocer was seeking in their automation project for their packaging line. Innova Group supplied the answer with a Stretch Hood automated packaging line with machinery specially designed for Baldocer’s safety requirements.
The new pallet packaging line came into operation at the beginning of 2022 in Baldocer’s Factory 1 in Villafamés. Baldocer is one of the leading ceramic firms in the sector, consolidating its position as a benchmark in growth and international presence in more than 130 countries. Its commitment to design, innovation and new technologies has led it to the current end-of-line automation project with Innova Group.
Automation objective: Increased protection and security
The automation project for Baldocer was designed with the premise of achieving greater protection and safety for its palletized product. To meet this objective and overcome problems caused by inclement conditions, Innova proposed an automated packaging line with double protection provided by the combination of the Stretch Hooder and the pallet Stretch Wrapper.
They also required a system that was fully automated, and a line prepared for access by different pallet vehicles (pallet truck, forklift and eventually in the future AGV).
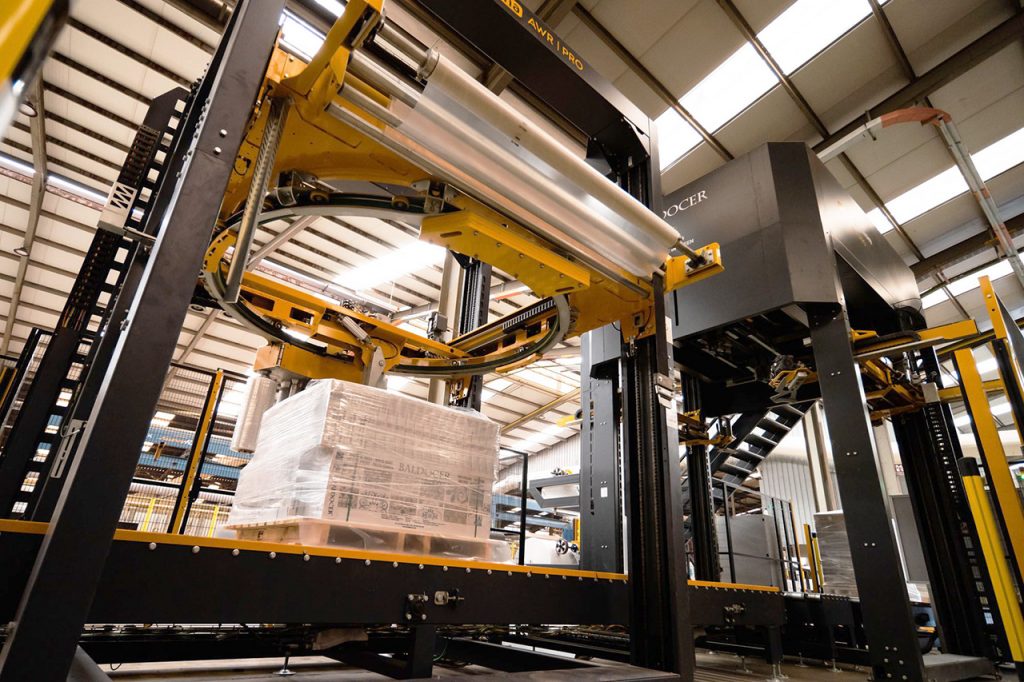
Baldocer’s project: One of the safest packaging lines
The ceramic company’s packaging line consists of the following systems with a focus on the safety of the product and the installation itself:
Stretch Wrapping System AWR | Pro with automatic cover dispenser:
The Automatic Ring pallet Wrapping system is the ideal solution to provide support and stability to Baldocer’s production, with very different pallet formats. Stretch pallet wrapping by ring provides better industrial wrapping of non-uniform palletized loads, offering a more customized hold to the load shape of the pallet than a pallet strapping system. In addition, Baldocer’s pallet stretch wrapper automatically applies a top cover for extra protection and the reinforcement roping system over the entire surface of the load to offer greater stability.
Baldocer’s automatic stretch wrapper is also prepared to include the high production accessory to accommodate future plans to increase production at the plant.
The industrial wrapping process of Baldocer’s loads proceeds with the following steps:
- Cover application: provides extra protection in storage, cargo handling and film removal.
- Wrapping cycle: automatic pallet wrapping is performed with precision by focusing on attaching the cover to the load, and attaching the base of the product to the pallet.
- Roping System application: during stretch wrapping, the reinforcement rope is applied extensively over the entire surface to achieve total pallet stability.
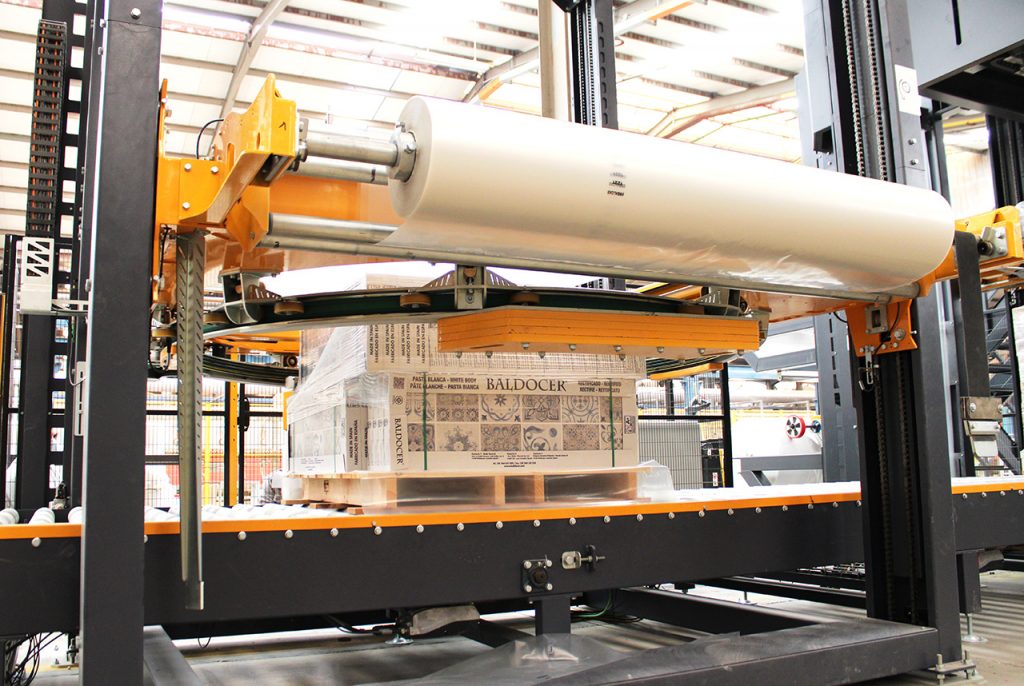
As we have discussed in previous articles, the wrapping system often replaces automatic strapping due to its advantages of adaptability to the shape of the goods.
LEARN MORE:
Comparative: Stretch Wrapping Vs Strapping Systems for pallet securing
Stretch Hood System SH Pro | S2
The Stretch Hood wrapping system installed at Baldocer has been designed and manufactured according to the customer’s safety requirements, with access by means of a ladder with safety handrails. The hooding system has two reels to adapt to the customer’s different formats, thus offering maximum protection in combination with the stretch wrapping system.
With the Stretch Hood system, Baldocer is also committed to this new packaging technology, which is more energy efficient and sustainable as it reduces CO2 emissions.
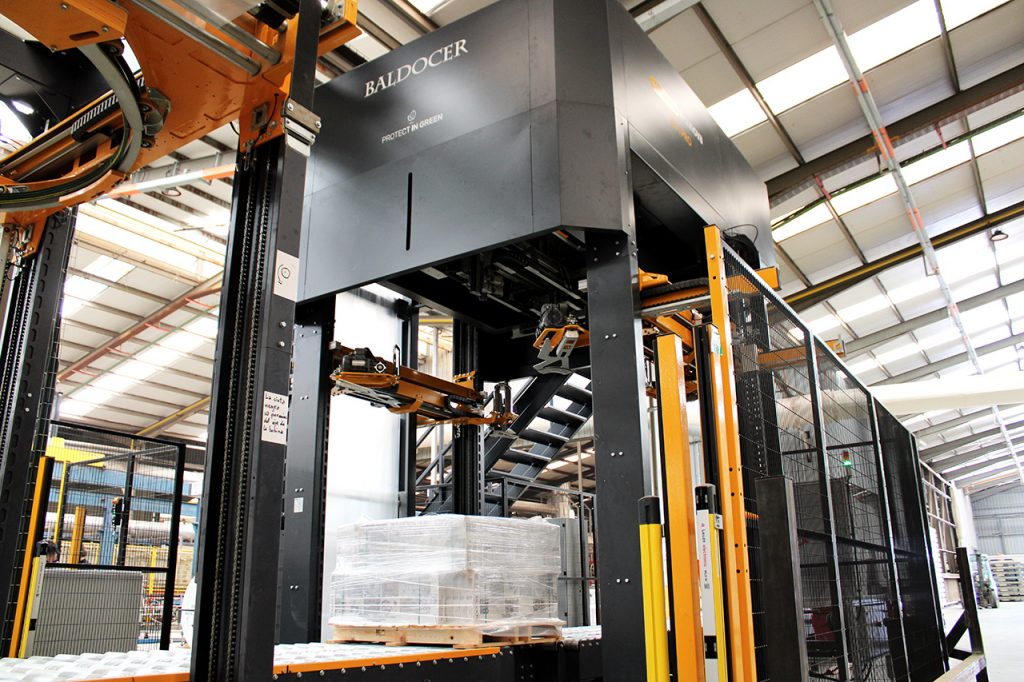
Pallet Conveyor line
The packaging line is connected by a conveyor line with an entry adapted to the three types of vehicles: pallet trucks, forklifts and AGVs. The actual entry to the line is provided by an elevator with chain plate conveyor for pallet truck access from ground level.
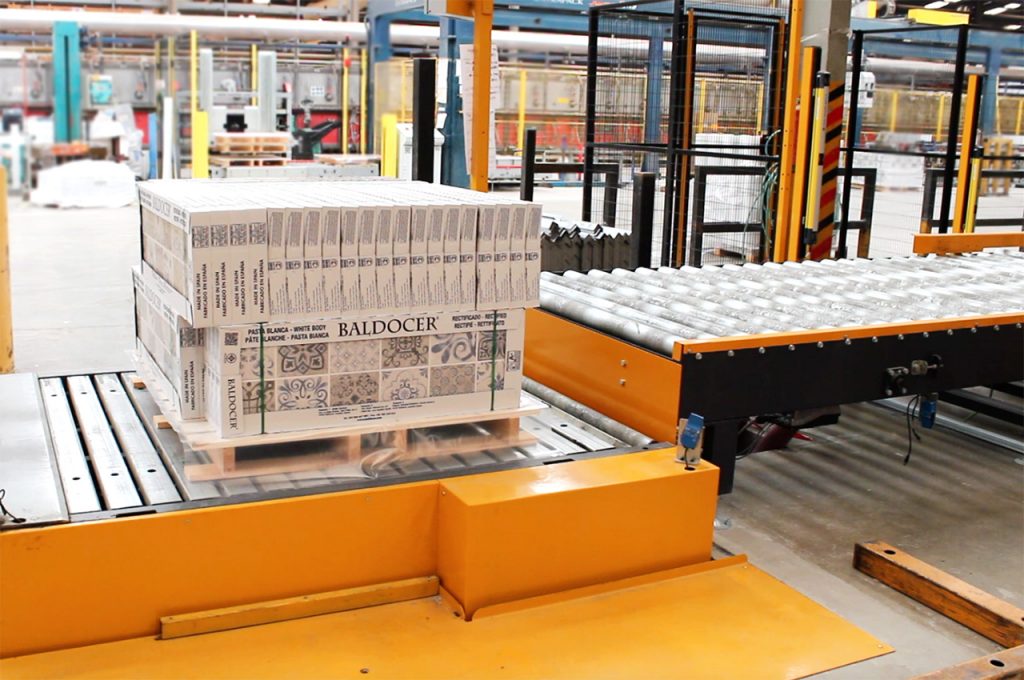
The pallet then goes through a centering device conveyor, prior to the stretch wrapper system. Finally, the end of the line has an outfeed conveyor for label printing and pallet pick-up. The outbound conveyor system includes a pallet weighing system connected to Baldocer’s ERP to provide the final pallet weight information that is already printed on-site on the logistics label.
The future: New phases of the automation project
The packaging line installed in Baldocer’s Factory 1 is prepared to include future expansions, such as a Horizontal Strapping System with edge protectors and pallet feeding by AGV. Baldocer’s packaging project also has two additional packaging lines in the pipeline, dedicated to standard and large-format production, respectively.
Baldocer has transmitted us their satisfaction with the project and the line already installed, as well as their confidence in Innova Group as a partner in packaging systems.
For Innova, working with Baldocer has been a pleasure since they are a reference company in the ceramic tile industry with whom we share a philosophy of innovation and with whom we hope to continue working for a long time.
Thank you Baldocer for trusting Innova Group!