Comparative: Stretch Wrapping Vs Strapping Systems for pallet securing
Is it better to stretch wrap or strap the pallet? Which one guarantees better load securing for long distance shipping? In today’s article we dare to compare two pallet securing systems that can be both substitutes and complementary depending on the type of product, packaging purpose and palletizing method.
Why compare these two packaging systems?
While strapping and pallet wrapping are totally different systems, they are comparable in that they both pursue the same objective of unifying and securing the palletized load. In many automated end-of-line systems with lightweight or medium weight loads, either one or the other solution is used: if we strap, we do not stretch wrap, and vice versa. With heavy weight loads, vertical strapping of pallets is also replaced by the pallet wrapping machine, since it offers a slightly different hold than strapping.
Let’s see then, each packaging type and its respective advantages.
Strapping vs. Wrapping packaging processes
Pallet Strapping Systems
Pallet strapping systems are one of the most versatile solutions for load securing. From manual to semi-automatic and automatic end-of-line applications, they are used to unify and secure boxes, bags, uniform packages and palletized loads. In the case of palletized loads such as boxes or bags, industrial strapping allows the goods to be secured using horizontal and vertical forces, depending on the system used:
- The Horizontal Strapping for pallets is used to compact the load and secure it horizontally at different heights. This automatic pallet strapping is used to avoid shifting of boxes during handling and shipping.
- The Vertical Strapping for pallets is used to join the load to the base of the pallet, offering greater stability in the shipping and also avoiding product shifting during transport.
Are horizontal and vertical strapping substitutable for each other?
In the case of light load securing, or with very stable palletizing, both strapping systems could be substitutes or alternatives. This is the case of lightweight boxes that only need horizontal securing and then have to be shrink wrapped or stretch wrapped. In the case of heavy, fragile or high-value boxes such as ceramic tiles, which combine all three characteristics, both horizontal and vertical holding forces are necessary, which is why they are usually combined at the end of the line.
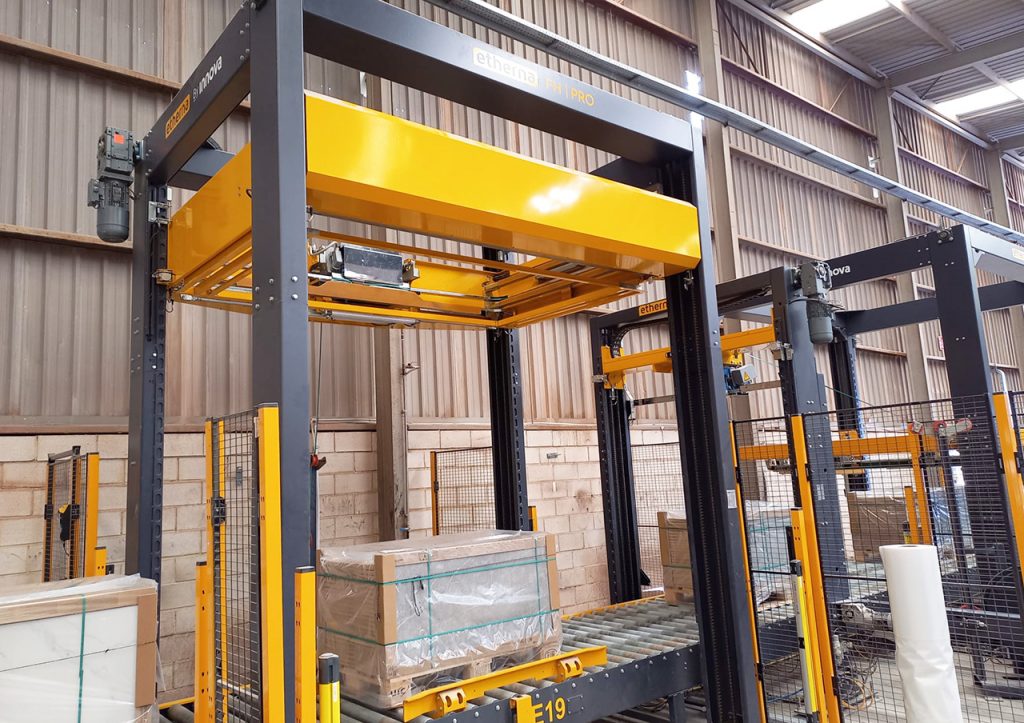
Pallet Stretch Wrapping Systems
The stretch wrapping system is also a very versatile solution used not only to secure but also to protect the pallet. In the automatic pallet stretch wrapping (non-manual) application, it enables the load to be held tightly horizontally and protected on its sides. With a wrapping cycle from the base of the pallet, it also ensures that the load is securely attached to the pallet. It is such a widespread solution for securing that it works on all types of loads, even if they are not always uniform.
- Automatic Stretch Wrapping System: Automatic and semi-automatic pallet wrapping machine systems provide greater speed in the wrapping process. In addition, by using a wrapping that reinforces specific areas of the load and the supplement of the reinforcement rope that acts as a strap, the pallet’s total stability is achieved.
If my pallets are wrapped, do I need to strap them as well?
Sometimes yes. A very tight wrap serves goes a long way to stabilize the load on a pallet, but for extra security and stability we also apply strapping to aid in keeping heavy loads firmly on the pallet. Unusual shaped packages and hand-wrapped items would also need strapping reinforcement.
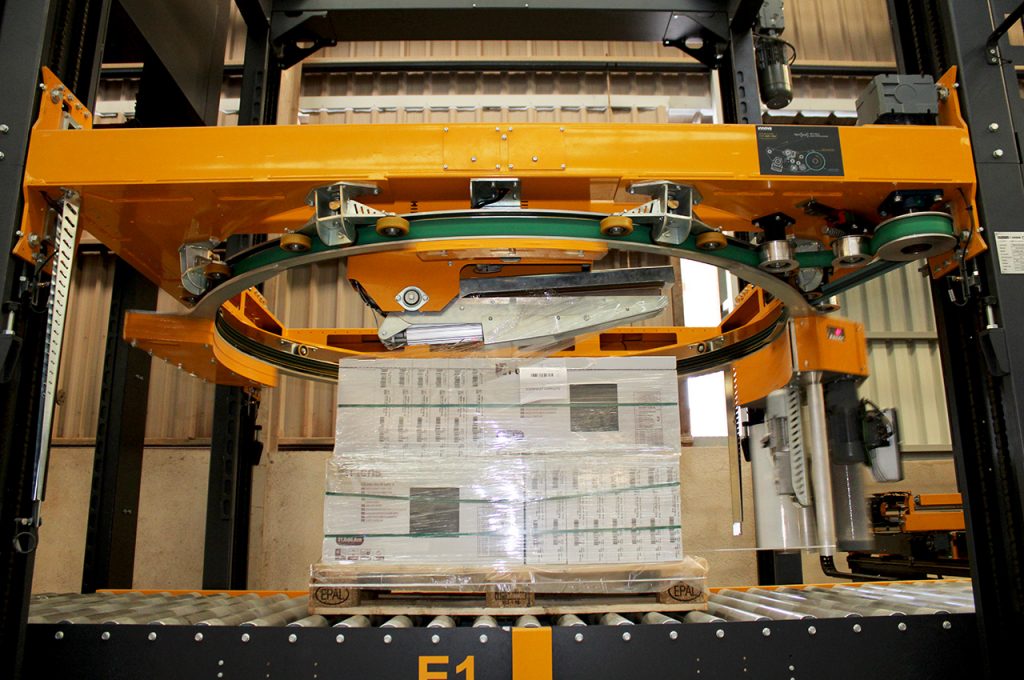
Advantages of Strapping vs. Wrapping
Let’s go back to pallet strapping to compare it with automatic stretch wrapping, in terms of securing advantages and objectives.
- Greater stability for heavy loads: the pallet strapping machine provides a better containment of the heavy load. In addition, the strapping consumable itself has greater resistance than stretch film.
- Higher packaging tension: Strapping can adjust the tension it exerts on the load so that on a heavy product (e.g. construction) it can be applied with greater force than on a lighter one (e.g. fruit crates).
- Fast process with minimal strapping: If we compare a load that only needs to be strapped in two or three levels with the entire cycle of a automatic pallet wrapper, the pallet strapping process will always be faster. Even so, there are high efficiency automatic wrappers on the market with double film carts that perform the cycle faster than an automatic pallet strapping system.
- Safety when removing the strap: When strapping at various heights, it provides safer access to the product than breaking a wrapping or stretch hooding to gain access to it.
- Cheaper consumable material: Strapping the industrial pallet is more economical in terms of purchase and use of consumable material than wrapping it with film. There is a wide range of PET and Polypropylene strapping materials available, providing high performance strapping at a very affordable cost.
- Less waste and more recyclability: A pallet strapping machine uses less consumables and therefore generates less plastic waste per pallet. There is an increasing amount of recyclable strapping on the market, thus contributing to improve sustainability in packaging.
- Neater product presentation: Finally, for a product that does not need to be stretch wrapped for protection, strapping provides a better presentation with only the visible strapping bands.
Advantages of pallet Stretch Wrapping over Strapping
The pallet wrapping system, and especially its automatic version, offers different benefits to be considered depending on the product and securing objectives:
- More respectful wrapping: As it does not exert as much tension as industrial strapping, wrapping is more respectful to the product. Therefore, for certain fragile products or materials that could break (such as bags), it is preferable to secure the load with a stretch wrapper.
- Extra securing with roping device: the accessory reinforcement roping system acts as a strap that can also be applied in different directions (horizontally and transversally) to provide similar securing to the two types of horizontal and vertical pallet strapping.
- Superior adherence with Stretch Film: The Stretch Film has good adhesion on its inner side to adapt much more to the load and offer greater compaction with its layers. In addition, the stretch film (without pre-stretching) enables an elasticity of up to 350-400% in pallet stretch wrappers with pre-stretching system, offering a better hold to the product.
- Adaptable to non-uniform loads: Stretch pallet wrapping can be applied to loads that are not block-shaped, unlike pallet strapping systems. This advantage is decisive for logistics, picking cargo, supermarkets or production with non-uniform palletization.
- More efficient securing with only one system: for light or stable palletized loads, only the industrial pallet wrapper is needed to provide securing, and the two types of strapping are not necessary. On the other hand, for heavy loads (as in the case of ceramic products), it is advisable to use both types of pallet strapping or strapping plus industrial wrapping machine for greater securing.
- Product protection on the lateral sides: Finally, the wrapping machine for pallets covers the sides of the load to prevent it from being damaged during transport and handling. Although total protection would require the application of a top cover, pallet stretch wrapping holds and protects the pallet.
Other pallet securing systems: Stretch Hood and Shrink Hood
There are other pallet packaging systems that also offer pallet securing and protection, such as thermo-shrink and Stretch Hood wrapping. Both systems use a tubular film that adapts to the contour of the load, covering it and securing it vertically.
- In the case of the Shrink Hood packaging system, the securing is done by heat shrinking the film over the load.
- In the Stretch Hood system, a stretch film is applied slightly smaller than the contour of the load. The Stretch hood is stretched and adapted to the load by using blades that apply the film tightly on the product.
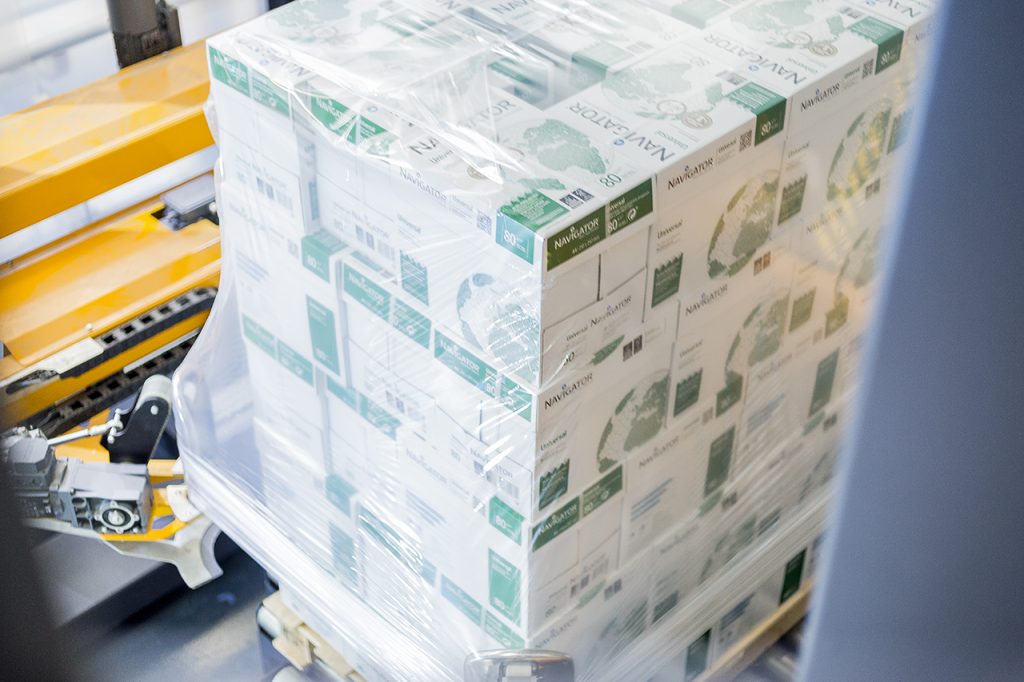
In fact, the Stretch Hood system is one of the most popular solutions for automated end-of-line packaging, due to its advantages in terms of protection, securing and speed of packaging. However, in the case of heavy loads or very fragile palletized loads, it is also recommended to use a securing system such as pallet strapping to provide extra security in the transport of the load.
Ultimately, the decision between using one system or another for pallet securing depends on many factors and objectives. Our recommendation is always to carry out previous studies and test the solution that best suits our product. At Innova Group we offer personalized consultancy and packaging tests in our Lab to determine which system is best suited for your product. Do not hesitate to contact us without obligation!