Innova Group installs a state-of-the-art packaging line for chemical compounds in Younexa
Innova Group has successfully deployed a Stretch Hood packaging system for ceramic chemical compounds at Younexa’s Castellón facility in Spain. This implementation forms a critical component of a comprehensive plant-wide automation initiative involving multiple technology partners, including Innova Group and Chumillas Technology. The fully automated installation integrates storage solutions, dosing, and packaging of solids, provided by Chumillas Technology and it culminates in the final wrapping of loads in the Automatic Packaging Line, using the Stretch Hood system by Innova Group.
Challenge: A Packaging Line Connected to the Dosing Plant
The project’s goal was to modernize and fully automate the processing plant, thereby improving production efficiency. Among the company’s engineering requirements was the complete renovation of the packaging system and end-of-line processes. Innova Group provided added value to the project by supplying packaging and conveying systems tailored to Younexa’s needs.
Innova proposed a Stretch Hood system for its superior cargo protection, waterproof capabilities, and enhanced safety during both international and domestic transport, outdoor storage, and distribution center handling. The Stretch Hood technology offers distinct advantages over alternative packaging methods that fail to provide complete load sealing and protection. Moreover, it demonstrates significant resource efficiency, consuming substantially less film and energy than comparable solutions such as stretch wrapping. The Stretch Hood system can reduce film consumption by up to 50% per pallet when compared to conventional alternatives.
The installation also included a Bag Press System and an innovative automatic Pallet Dispenser System connected to the flow of incoming pallets on the line.
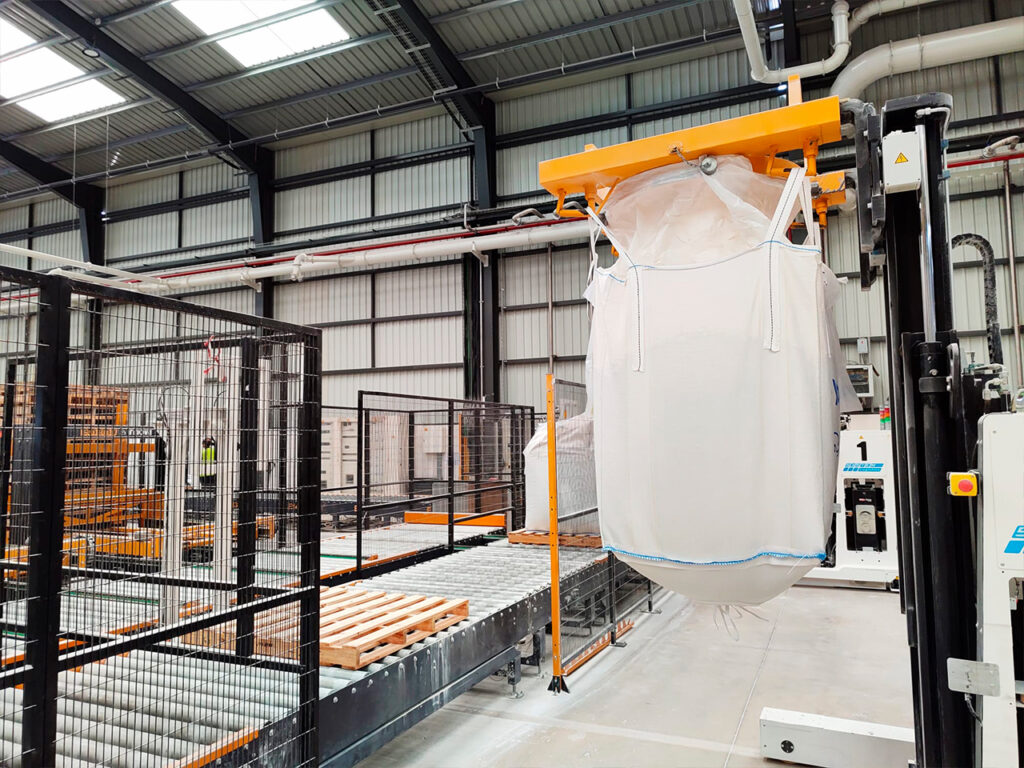
Innova’s Solution: Smart Packaging Line
In this industrial automation project, Innova Group installed the packaging line and integrated it with the dosing and bagging systems. Furthermore, the project involves coordinating intelligent Automated Guided Vehicles (AGVs) that autonomously and efficiently transport FIBC bags to the packaging area.
The new packaging line consisted of the following systems:
1. Pallet dispenser:
Innova has developed the innovative Automatic Pallet Dispenser PD | PRO by Innova to ensure a continuous, automated supply of pallets, which are intelligently requested from the AGV area.
This system is a new development designed to adapt to the constant load flow according to Younexa’s requirements at the plant.
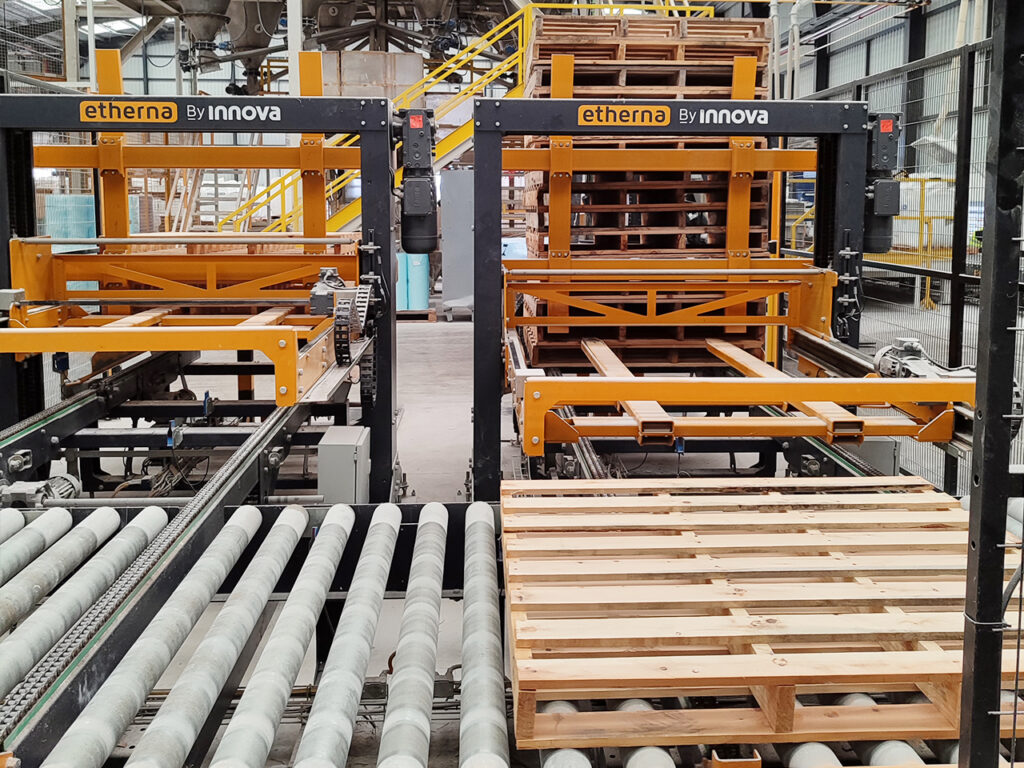
2. Hydraulic Compactor Press:
Next, the Hydraulic press system PR | PRO by Innova is in charge of compacting the load of FIBC bags, providing greater stability and volume reduction for easier handling.
Innova’s hydraulic press offers several benefits for packaging and logistics when dealing with chemical loads. It allows for significant savings on packaging materials by reducing the overall volume of the load and optimizing film usage in systems such as Stretch Hood and Stretch Wrapping machines. Additionally, it helps lower transportation costs, particularly for exports, by decreasing package dimensions. The press’s compacting capability enhances storage efficiency, making it easier to stack bulk bags for better handling. Finally, using hydraulic force through pistons, ensures lower energy consumption, making it a sustainable and efficient solution.
3. Stretch Hood System:
Finally, the loads are completely protected with the Stretch Hood wrapping system. This system is the most advanced and sustainable packaging solution, providing total sealing and protection for the chemical cargo against external agents such as humidity, dust, or adverse weather conditions. The Stretch Hood model installed in this plant has two film reels to adapt to different formats and offer greater productivity.
The Stretch Hood system is the ideal solution for protecting chemical loads thanks to its airtight sealing and its ability to provide a superior barrier against external agents. Stretch Hood film provides complete coverage without heat, unlike traditional methods like stretch or shrink wrapping, safeguarding temperature-sensitive products, like chemical loads, from deterioration.
Additionally, its high mechanical resistance and elasticity provide a firm and stable hold, reducing the risk of spills or contamination. The complete transparency of the material allows for quick product identification and traceability, which is essential in the chemical industry, where proper handling and storage are critical. By reducing material usage and improving energy efficiency, Stretch Hood promotes sustainable and cost-effective packaging in the industry.
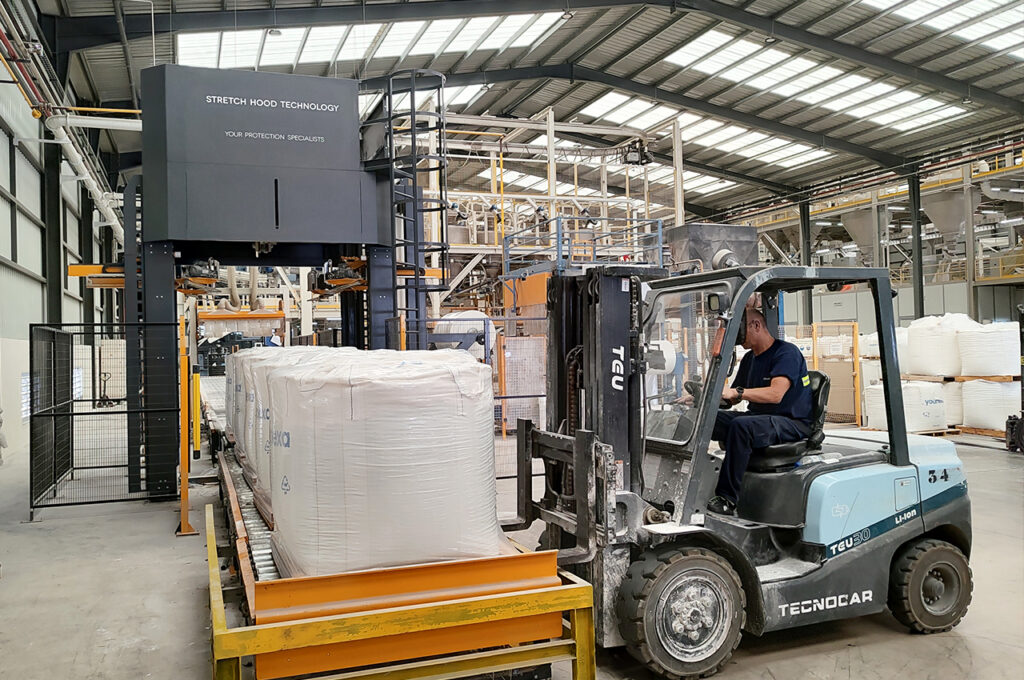
3. Conveyor line:
The entire packaging line is linked by a conveyor line that connects all the systems composed of:
- Conveyor 90º transfer system, which combines roller and chain conveyors, to move the wooden pallets at the Pallet Dispenser system
- Rotating conveyor system, to adapt to the flow of the line
- Load centering systems, to center the loads in the conveyor line before the Stretch Hood system
- Special conveyor system for stretch hooding
- Outfeed conveyor line for pallet accumulation and final pick-up
Check out in this video all the details of the packaging line carried by Innova in Younexa:
Results: Innovation and Efficiency in a Benchmark Chemical Plant
Innova Group’s packaging line implementation has significantly enhanced efficiency and security in Younexa’s packaging process. This advancement ensures optimal load stability during international shipments and throughout storage at various distribution facilities. Additionally, the Stretch Hood technology has optimized material consumption, substantially reducing plastic usage per load—generating cost savings on consumables while supporting environmental sustainability initiatives in alignment with corporate environmental commitments.
This packaging system reinforces Younexa’s strategic focus on quality and innovation while ensuring consistent, professional product presentation throughout distribution channels, thereby strengthening their market position. Furthermore, the enhanced efficiency of the new system boosts productivity and minimizes end-of-line processing duration, delivering substantial value to Younexa’s logistics operations.
In summary, Innova Group is proud to collaborate with leading companies like Younexa, delivering innovative and efficient solutions that address the current needs of the industry and contribute to the advancement of the packaging sector.
Thank you, Younexa for trusting Innova on this project!