Pallet strapping: Comparison between vertical and horizontal strapping systems
Is it better to strap the pallets horizontally or vertically? Is vertical strapping required if I have a horizontal strapping machine? And vice versa? When designing a automatic packaging line, different systems are chosen according to the objectives of the project (securing, protection, etc.).These systems may often be substitutes or alternatives, as is the case for protection between the pallet stretch wrapper and the Stretch Hooder. Other times, they may be complementary, as in the case of strapping for securing and the Stretch Hood for protection. Today in this article, from our experience as automatic strapping systems manufacturers, we are going to analyze the two types of automatic horizontal and vertical pallet strapping, comparing them to each other towards their objectives.
Automatic pallet strapping systems
Pallet strapping systems belong to the tertiary industrial packaging of the product on the pallet and are applied to secure and stabilize the load on the pallet. As the name suggests, their application is different depending on the orientation of the strap, but they also differ in load securing objectives:
- Horizontal pallet strapping applies a horizontal strap containing the load at different heights. Its main objective is to hold the load together and consolidate it into a single block to facilitate its transportation.
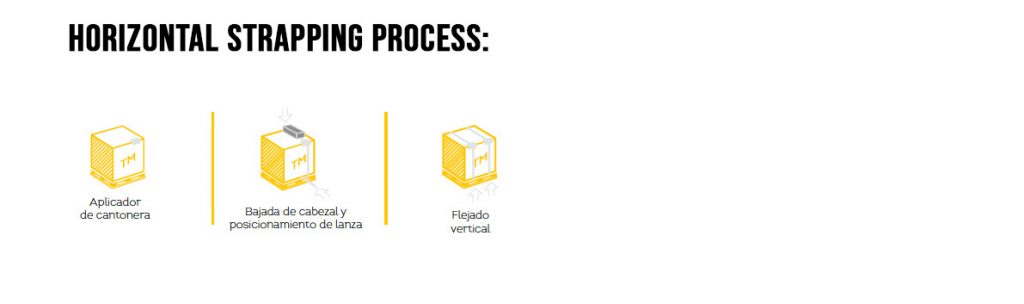
- Vertical pallet strapping applies the strap vertically from the base of the load, underneath the pallet, to the top of the load. This way the load is fixed to the pallet, its transport base, as well as containing the goods vertically.
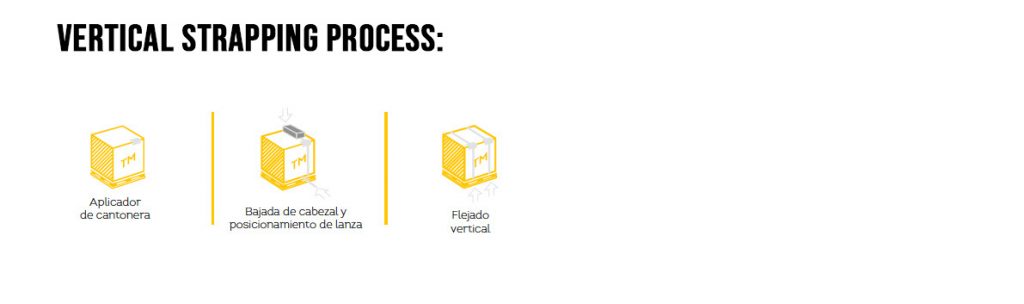
Is it necessary to apply both pallet strapping types?
As we have seen, both types of industrial strapping seek securing and stability and both allow the load to be fixed and unified after palletizing. For this reason, these systems are often used in a complementary way with different objectives.
When only horizontal pallet strapping is required:
In the event of having a very stable load that does not need vertical containment, or using other load securing systems, only the horizontal pallet strapping machine would be needed to compact and secure the goods together. This is the case of using complements such as anti-slip sheets on the base of the pallet, or other additional securing systems such as the stretch wrapping machine.
For instance, in some ceramic lines, horizontal strapping machine is used to unite and compact the load and the automatic pallet wrapping machine is used to fix the boxes to the base of the pallet. Certain heavy-weight products, such as concrete blocks, only require a vertical pallet strapping machine to attach them to the pallet.
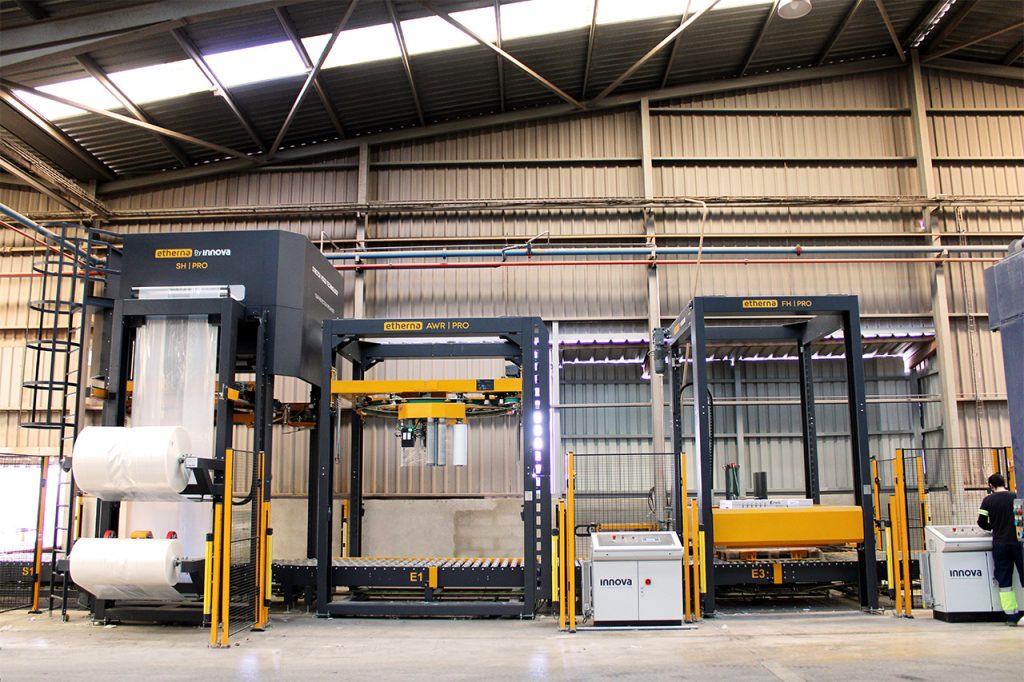
When only vertical pallet strapping is required
Automatic horizontal strapping is not needed if the product does not require horizontal compaction or load unitization. This would be the example of loads that only require securing to the base of the pallet. Some examples would be high loads that need to be stabilized for transport, light loads that need to be unitized to the base, heavy stable bags that need to be fixed vertically, etc. Product packaging formats could be as diverse as bottles, drums, barrels, boxes, paper, cardboard, etc.
Generally, these are combinations of packaging lines with automatic vertical strapping for securing, plus stretch hooding or wrapping with cover for protection.
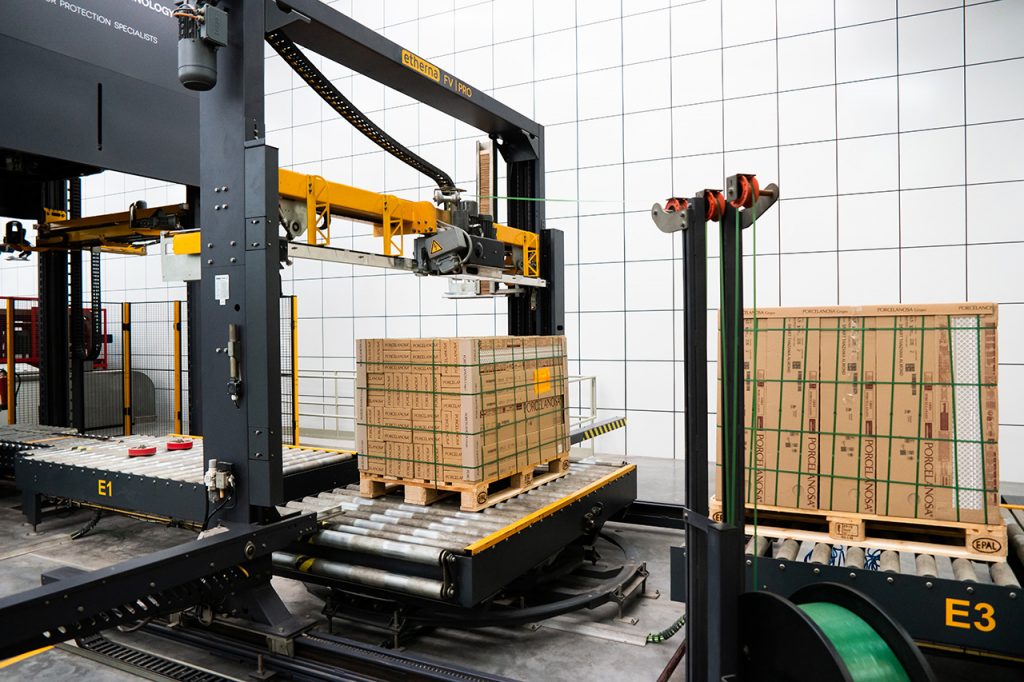
When both types of strapping are necessary
For light, heavy, unstable, special size products, etc., both types of horizontal and vertical containment are always recommended. In the ceramic industry, the product has all these characteristics and needs to be compacted and fixed with the respective automatic strapping systems to secure the product during transportation over thousands of kilometers.
READ MORE:
Most efficient packaging system combinations for your end of line
Additional advantages of automatic pallet strapping
As we have seen, the two systems have slightly different objectives, but what other advantages do they offer respectively?
Further advantages of horizontal pallet strapping
Beyond compaction, horizontal strapping provides:
- First pallet securing at the packaging line: Following palletizing, the load can often be very unstable and requires horizontal strapping for initial compacting and securing before going through other automatic packaging systems such as wrapping, sealing, Stretch Hooding, labeling, etc.).
- Safer packaging process: By compacting and unifying the load, both the application of stretch hood and automatic stretch wrapper is done more safely on an already unified merchandise, without protrusions or deformations.
- No loss or transport damages: The horizontal strapping avoids horizontal product losses and ensures that there is no shifting between the different product levels of the pallet.
- Extra security with edge protectors: Applying vertical edge protectors during industrial strapping provides extra protection for the load with boxes; so that they are not damaged by strapping or handling during transport.
- Safer depalletizing: By strapping horizontally at different heights, the process of removing packaging and strapping can be carried out by area according to the customer’s needs.
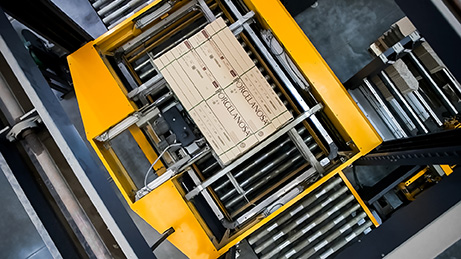
Advantages of vertical pallet strapping
As we have seen, industrial pallet strapping is done vertically to offer unification with the base and greater height stability for fragile, unstable, or high loads. Other key advantages:
- First securing after palletizing: In case there is no horizontal strapping, the vertical pallet strapping will be used for the first securing of the load to provide greater stability and safety before stretch wrapping or hooding.
- Prevents load shifting: In the case of a very turbulent transport (for instance by ferry or ship), the unification of the load to the pallet will prevent it from sliding or shifting.
- Safety in unpacking: The vertical strap will be the last packaging element to be removed, allowing to offer that extra safety before the load is completely unpacked.
- Flawless presentation at the point of sale: Compared to the automatic wrapping machine used to secure and fix the load to the pallet, strapping offers a cleaner presentation at the point of sale.
In short, it is important to know all the possibilities offered by the different automatic packaging systems to obtain protection and security fully adapted to your product. In the case of pallet strapping, we have seen that the two types of securing are not always necessary and that each type offers different benefits.
At Innova Group we rely on the experience of hundreds of installations of packaging lines with automatic strapping for customers from a wide variety of industries. Do not hesitate to contact our technical team, we will be pleased to offer you customized consultancy and free quotation for your packaging project.