Why Does Stretch Hood Provide Greater Savings Compared to Other Packaging Systems?
Why do we often say Stretch Hood offers savings compared to other packaging solutions? In the logistics sector, efficiency is not only measured in terms of load protection but also by the economic and operational impact of the chosen system. Among the many options available, the Stretch Hood system has become a key solution for pallet packaging in recent years, thanks to its ability to save costs and deliver superior performance compared to traditional systems like automatic stretch wrapping or shrink hooding.
In this article, we explore the key differences between these packaging systems and analyze how Stretch Hood optimizes costs while enhancing packaging quality.
The Differences Between Stretch Hood and Other Systems
Stretch Hood vs. Shrink Hood systems
Shrink hooding involves using heat to seal and shape plastic film around a load. This process requires ovens or heat generators, which consume considerable amounts of electricity or gas. Additionally, the application process tends to be slower and may result in increased wear and tear on machinery due to the high temperatures involved.
The Stretch Hood method applies film without using heat. It utilizes a clamping system to stretch the tubular film, allowing it to conform to the shape of the pallet. This approach not only reduces energy consumption but also decreases the risk of damage to heat-sensitive products.
Furthermore, the type of film used in Stretch Hood is thinner than shrink film, offering additional savings.
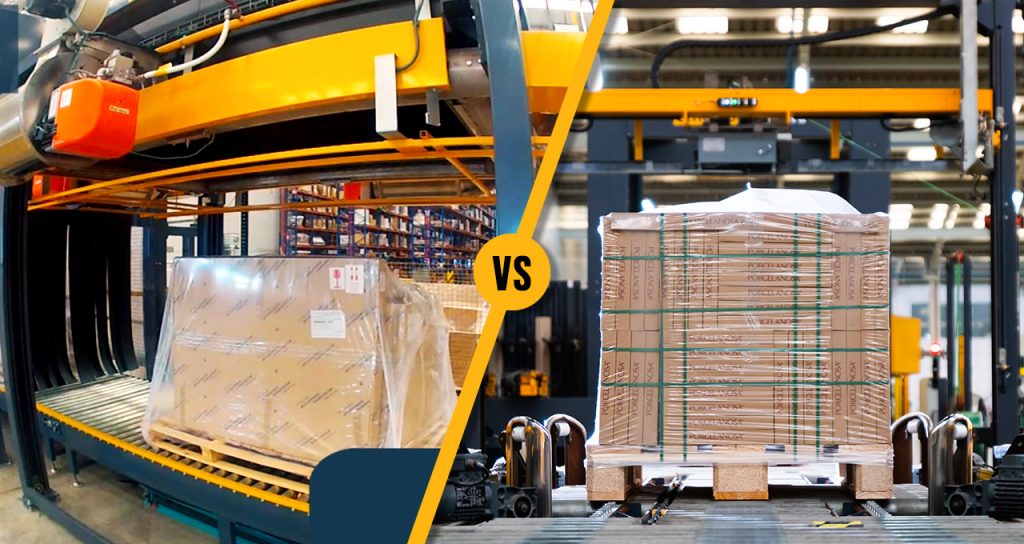
Stretch Hood vs. Stretch Wrapping Systems
Stretch Wrapping machines use stretch film to encase the pallet in multiple layers. While they offer good protection, they tend to consume more material due to the film overlap necessary for load stability. To ensure complete load protection, these systems often require a top cover, which increases consumable costs. Additionally, most standard wrapping machines available on the market have longer cycle times since they must perform multiple rotations around the pallet to complete the wrapping process.
Stretch Hood provides stability and protection through a single layer application, which significantly reduces plastic consumption and accelerates operation times.
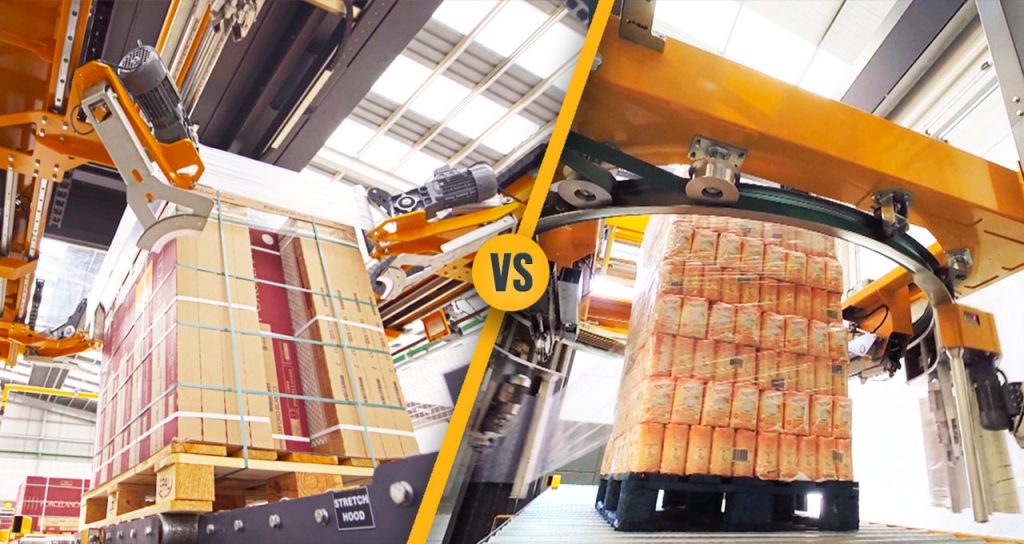
Key Savings with Stretch Hood
Let’s dive into the specific areas where Stretch Hood allows optimization and cost reduction. Based on our experience with hundreds of projects and installations, making the switch to this technology typically leads to cost savings. However, in some cases, the overall savings may not be as significant as anticipated. Nevertheless, transitioning to Stretch Hood provides additional benefits, including improved presentation, enhanced safety, and consistent packaging quality.
1. Energy Savings
Since Stretch Hood does not require heat to apply the film, it can reduce energy consumption by up to 50% compared to shrink-wrap systems. This not only positively impacts operational costs but also enhances sustainability by lowering the carbon footprint of operations.
2. Savings on Consumables
Thanks to the elasticity and durability of Stretch Hood film, less plastic is needed to secure the load compared to stretch wrapping systems. This reduction in the use of consumables can lead to significant cost savings, particularly for companies managing large quantities of pallets and using extensive amounts of stretch film.
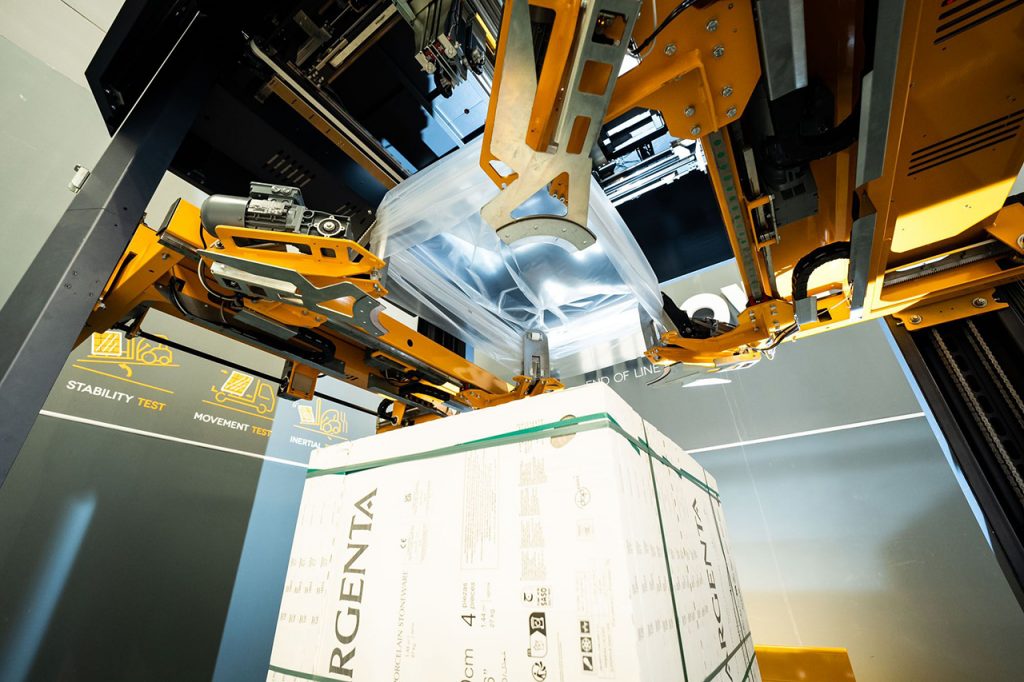
4. Savings Through Automation
Stretch Hood systems are designed to operate fully automatically, eliminating the need for manual intervention during the packaging process. This contrasts with semi-automatic or manual systems, which require personnel to apply the film, adjust machines, or supervise the process. Automation reduces labor costs and minimizes the risk of human errors, ensuring consistent and high-quality packaging.
5. Savings Through Greater Autonomy
One of the major advantages of Stretch Hood is its high autonomy. A single Stretch Hood film reel can wrap approximately 1,000 standard-size pallets, whereas a stretch film reel in an automatic wrapping system typically wraps around 200–300 pallets. This significant difference means that operators using Stretch Hood will change film reels far less often, leading to:Increased operational efficiency: Fewer interruptions in the packaging line.
- Reduced downtime: Operators can focus on other critical tasks instead of frequently replacing consumables.
- Lower operational costs: Reduced need for manual intervention decreases the total cost of the process.
6. Savings on Maintenance
Stretch Hood systems have fewer components subject to wear and tear since they do not use heat or constant rotational movement. This translates to fewer line stoppages for maintenance and lower repair costs.
7. Operation Time Savings
Stretch Hood applies the film in a single step, enabling faster cycles compared to traditional systems. This results in increased productivity, especially in high-demand production lines.
Not Just Savings: The Unseen Advantages of Stretch Hood
In addition to economic savings, the Stretch Hood system offers additional advantages that reinforce its position as a leading packaging solution. As mentioned, the expected savings may not always be the primary driver for companies adopting Stretch Hood. Instead, they often choose it for the other benefits where Stretch Hood outperforms other systems. Some of these include:
- Complete Protection Against External Elements: Total waterproof protection is one of Stretch Hood’s standout benefits. The hermetic seal provided by the film ensures that pallets are fully protected from water, dust, and other external factors.
- Impeccable Presentation: The total transparency of Stretch Hood film enhances product visibility and reinforces the brand image. This transparency also facilitates logistical traceability by protecting and enabling easy scanning of labels and barcodes.
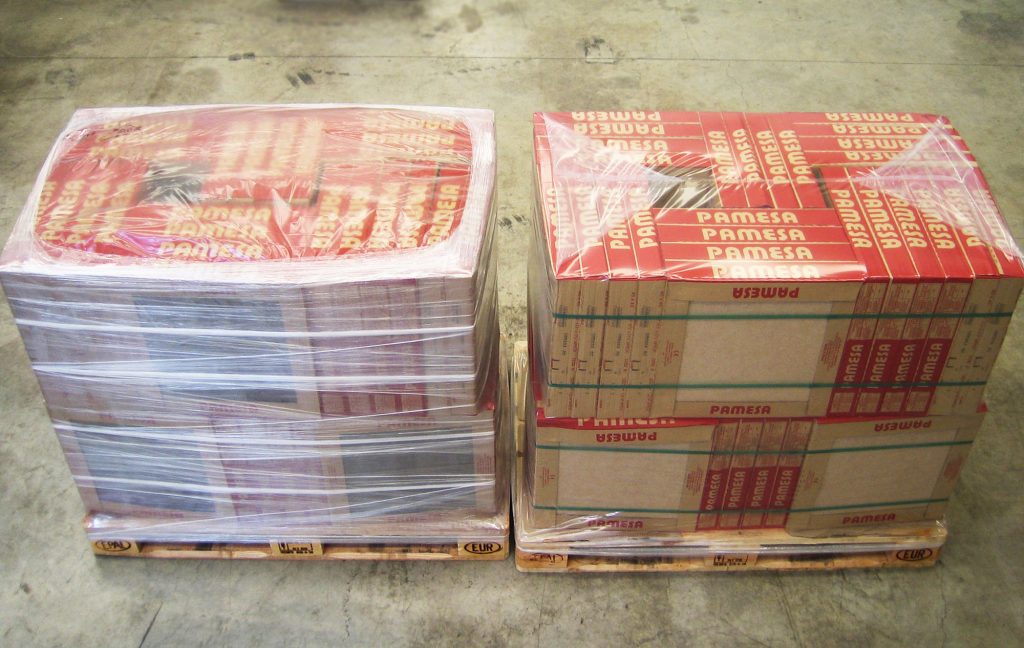
- Versatility: Stretch Hood adapts to various pallet sizes and shapes, making it ideal for diverse industries such as food, beverages, construction materials, and more. In comparison to stretch wrapping, it enables the packaging of very small loads, where automatic wrapping would be nearly impossible. An example of this is using Stretch Hood for picking loads.
- Sustainability: By using less plastic and energy, Stretch Hood aligns with the sustainability goals of many companies. Moreover, Stretch Hood systems from Innova Group are developed with high-efficiency motors and components, further reducing their carbon footprint.
In summary, Stretch Hood optimizes packaging processes and provides significant savings compared to other systems like shrink hooding or stretch wrapping. Its capability to decrease energy, material, and time consumption makes it an ideal solution for companies aiming for operational efficiency and sustainability.
At Innova Group, we specialize in providing Stretch Hood systems that combine advanced technology with complete customization to meet the needs of each client. Would you like to know whether Stretch Hood is the right packaging solution for your company? Contact us today and discover how we can help you reduce costs and improve your packaging line.