5 keys points of the Automatic Wrapping Machine: achieve maximum stability of the pallet
When selecting a packaging system for your end of line, it is important to take into account the objectives sought with this system: protection, grip, stability, safety, hygiene… In terms of pallet handling, one of the solutions preferred by many industries is always the wrapping system, either in its automatic or semi-automatic versions. Today, we are outlining the advantages and technical highlights of the automatic wrapping system, as a single packaging solution or used as a holding complement in a Stretch Hood packaging line, a combination commonly used in the ceramics sector.
Why the wrapping system for subjection?
As its name describes, this system wraps the load with a Stretch film that provides support on all four visible sides. It is therefore a system that is highly valued for its stability, as the film stretches and adapts to the load. Usually, the wrapping system includes the option of applying cord to provide extra support similar to that offered by horizontal and vertical strapping systems.
What kind of wrapping machine do I need for my product?
Being one of the most widespread systems, it is also one with the most models and options on the market. From semi-automatic wrapping machines, with rotating or mobile plate, to fully automatic wrapping machines, usually with platform, rotating ring or rotating arm, among other options. Depending on the type of product and production needs, technical managers usually choose a semi-automatic or fully automated system for large productions.
The automatic wrapping system allows to pack an average of 100 pallets/hour, so it is a system widely used at the end of the line in many industrial sectors, offering the total automation of its packaging.
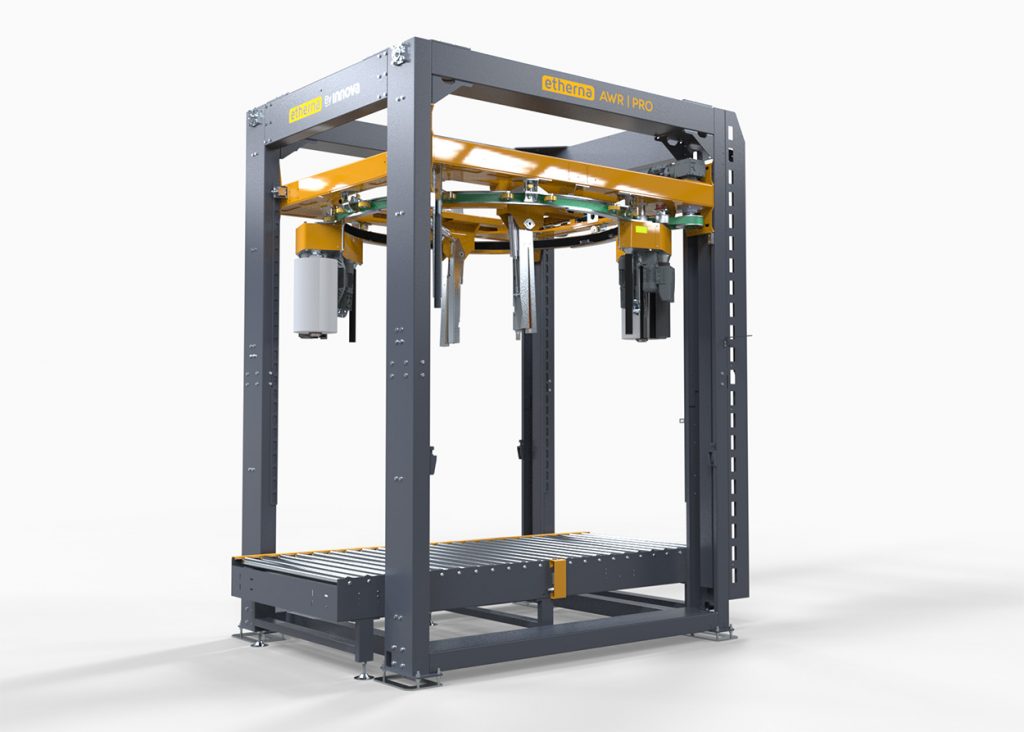
Technical highlights of the automatic pallet wrapping system
As experts in end-of-line solutions, we analyzed the key features of the automatic wrapping machine:
1. Stretch wrapping and stability:
The wrapping system provides support and stability by two factors: on one hand it wraps and compacts the load by stretching and adapting the film to the product, and on the other it holds the load thanks to the application of the elastic cord. In the case of the ring wrapper, the accuracy of the film and cord is higher since it includes a height position control for the application of the film and cord layers.
For light or unstable loads, the automatic wrapping machine can include a top press to hold the pallet while wrapping, thus ensuring efficiency.
2. Wrapping with custom finish
The automatic wrapping machines provides customized packaging finishes according to the needs of fastening and protection. In the case of the ring wrapping machine, it provides different types of upward or downward wrapping or both to ensure the best hold and finish. The wrapping cycle is also carried out at any height defined, according to the needs. Optionally it also includes the option of applying a plastic cover to protect the top of the load for storage outdoors or in adverse conditions.
3. Adapted to different types of load
Stretch wrapping is a very versatile system that can be adapted to different pallet heights and load shapes. The film reel is easily replaceable and can be adapted to different sizes according to production requirements. This makes it the system that adapts to more industries and products, and even recommended for picking or logistics pallets, as it allows a more suitable grip than other systems such as automatic strapping.
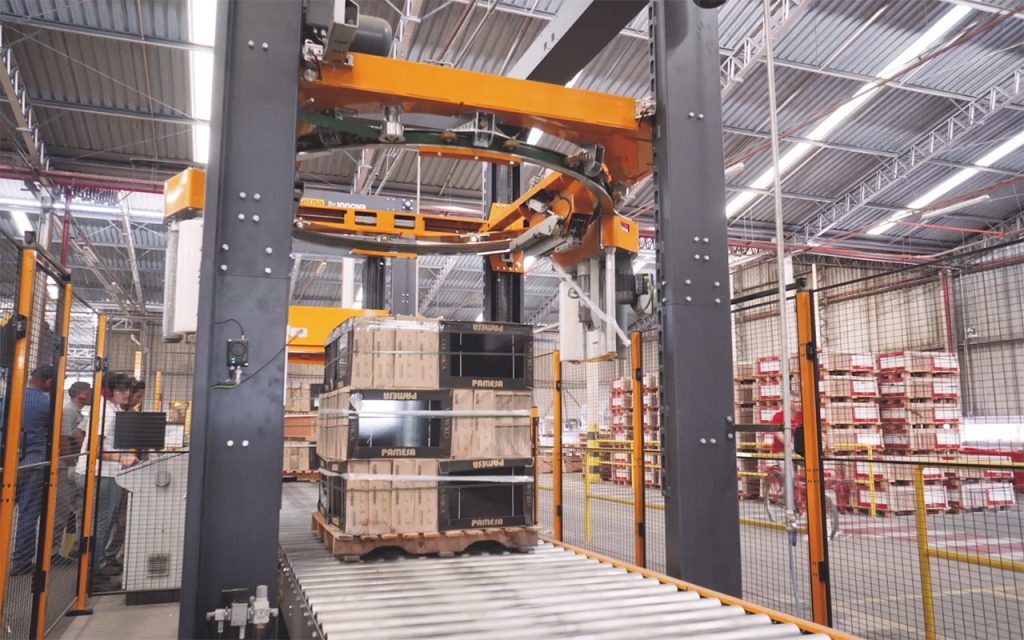
4. The extra holding option in a packaging line
The wrapping system can be used to provide extra hold on a Stretch Hood packaging line. This is a solution that meets the needs of total product protection, for which the Stretch Hood system is recommended, with the wrap-around fastening provided by the wrapping machine.
For the ceramics sector this is a common combination, using strapping and wrapping to hold and Stretch Hood to protect the pallet. With special loads, or composed of small boxes, the wrapping system provides a hold that adapts to the load without applying excessive pressure. The wrapping machine’s cord acts as the strapping, joining the load to the pallet and offering greater stability. This type of line includes the horizontal strapping system before the wrapping machine, with or without edge protectors. The horizontal strapping helps to compact the ceramic load, turning it into a block before it reaches the wrapping machine. The final objective of this type of line is that the ceramic load reaches the customer as safely and flawlessly as possible, thanks to this specialized packaging combination.
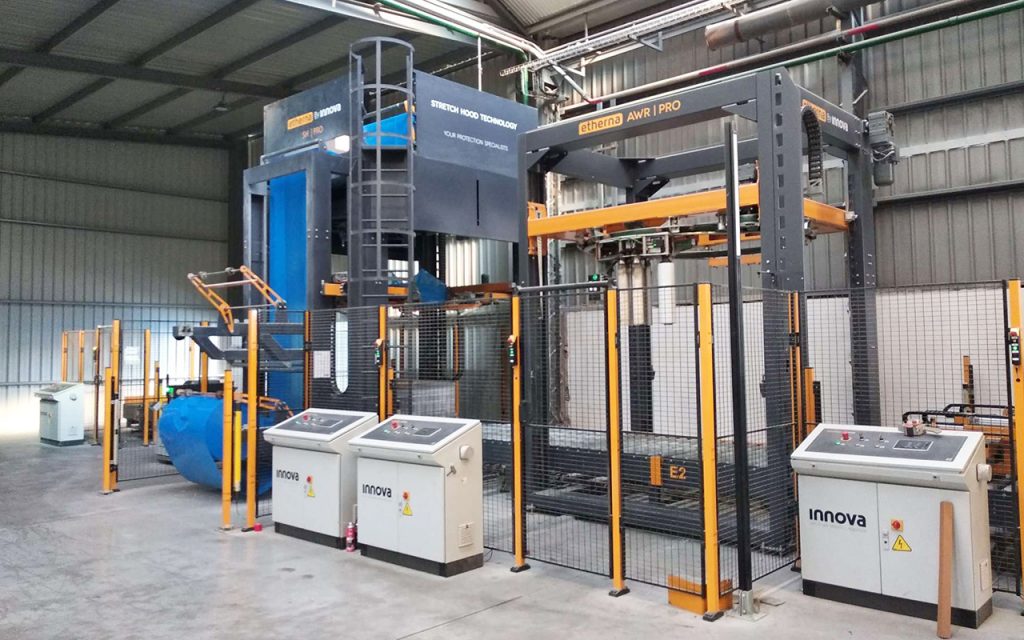
5. Sustainability and reduced film consumption
Finally, the most advanced wrapping systems, like the case of the ring wrapper Etherna from Innova, have a very precise control of the film used, thus contributing to reduce costs and film waste, in a more sustainable line of work. Thanks to its electronic system with a Torque control, the wrapper uses the exact amount of stretch film needed according to the load and dimensions of the pallet. The stretch wrappers developed by Innova use low energy consumption and have a low maintenance cost, as well as reducing CO2 emissions compared to pallet wrapping systems such as Shrink Hood wrapping.
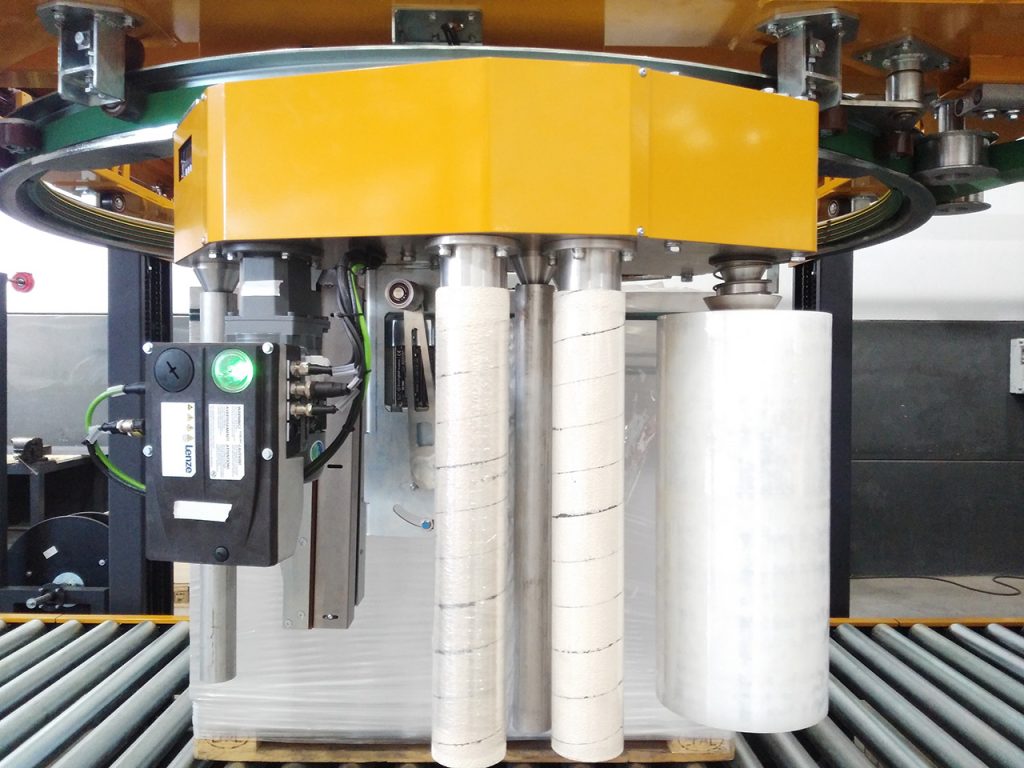
In summary, the automatic wrapping system is one of the best solutions to provide safety and stability in the handling of pallets. Many customers from different industries already trust Innova with this type of solution, either as a unique packaging system or as a complement to their end of line. Consult our technical department without obligation about the possibilities and advantages of this solution for your product.