How Standardization in Programming Contributes to the Efficiency of Packaging Lines
When designing and programming a packaging system, it is crucial to have a process methodology in place. We have implemented Lean Manufacturing methodology at Innova Group for years, specifically working with continuous improvement and process standardization. Today, we open the doors of our Electrical Technical Office and Programming department to explain how our process standardization method has improved the programming of our machinery and, consequently, the efficiency of our packaging systems.
Standardization in the Design and Programming of Packaging Machinery
What does process standardization mean? As the name implies, it involves establishing clear and consistent standards and procedures for carrying out tasks across various departments of a company.
Standardizing processes is almost mandatory if the company follows a project management methodology, such as Agile or Lean Manufacturing. These are work methodologies based on continuous improvement, where processes are streamlined by continuously working, adapting changes, and procedures as the project takes shape.
Imagine, for instance, our Packaging systems programmers. Consider the number of languages, codes, programming systems, and PLC systems they use. How can we find a language that is universally applicable, maintains pace with work, and also monitors and detects errors or changes? This is where using a standardization method plays a key role.
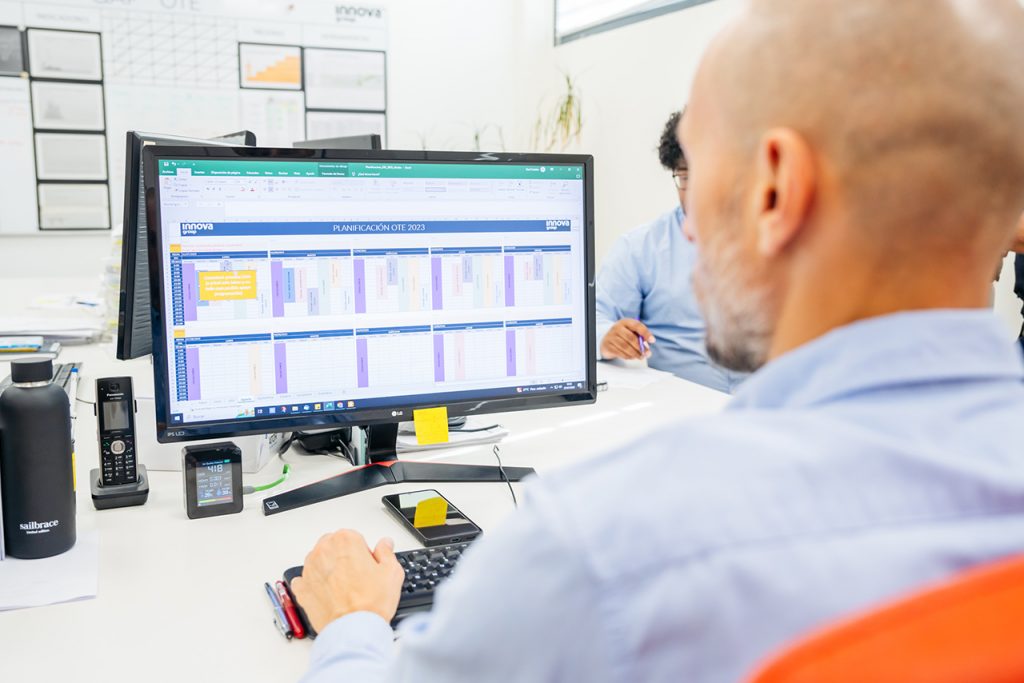
Advantages of Standardization in the Manufacturing of Packaging Systems
“If there is no standard, there is no improvement,” once said Taiichi Ohno, founder of Lean Manufacturing and Toyota engineer. To highlight the truth of this statement, let’s look at some of the benefits standardization brings:
- Improved Efficiency: By clearly defining how tasks should be performed, variability is eliminated, and the time and resources needed to complete them are reduced.
- Error Reduction: Standardization helps identify and eliminate potential error causes, improving the quality of work.
- Better Communication and Collaboration: Having a common reference framework allows people working in different areas of the company to communicate and collaborate more effectively. Communication becomes clearer, and confusion is eliminated.
- Facilitates Innovation: Standardization frees up time and resources that can be used for innovation. Additionally, by creating a solid process base, the company is better prepared to implement new changes.
- Continuous Improvement: Standardization provides a framework for the continuous improvement of processes. By documenting processes, areas that can be improved are easily identified.
Standardization at Innova: The Programming Example
At Innova, we have been implementing Lean Manufacturing methodology for years, based on the Japanese kaizen philosophy of “improvement is infinite.” Applied to the specific area of machinery programming, the department follows a series of processes and performance indicators, aiming to make program developments more agile and take less time.
Our Electrical Technical Office Manager, Raúl Catalán, explains how his department applies Lean methodology and standardization to improve processes: “Lean methodology has been implemented at Innova for some years now, but this practice has evolved as new technologies have been applied. Standardization must always go hand in hand with technological innovation to improve and maximize results in operational processes.”
“We are aware that process standardization, if implemented rigidly, can become an obstacle to innovation. Therefore, at Innova, we seek a balance between efficiency and flexibility,” adds Raúl.
For this reason, Innova has implemented flexible standardization, allowing for adaptation to changes and the incorporation of new ideas without compromising process consistency.
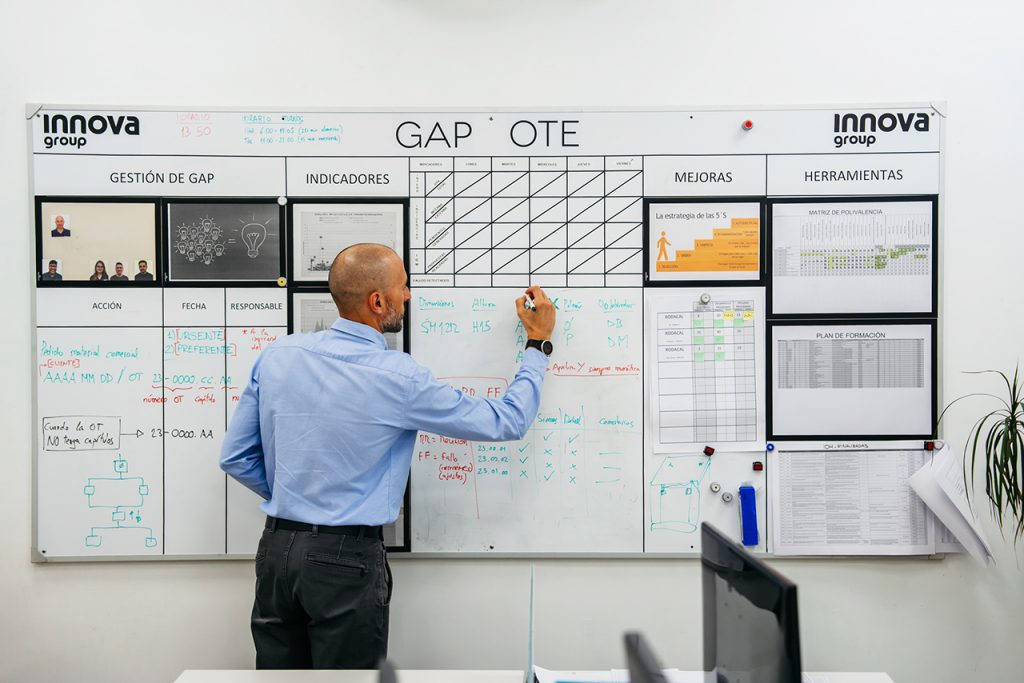
Thanks to this standardization approach, we have achieved different objectives in the programming area:
- Unify different codes, nomenclatures, and languages for the same purpose: this has improved communication and collaboration between programming and machinery design teams.
- Improve communication among all collaborators.
- Enhance the maintenance and service of our machines, increasing the reliability and quality of our products and services.
- Significantly improve the PLC systems of our automatic and semi-automatic packaging machines: this has made packaging machines more efficient and easier to use.
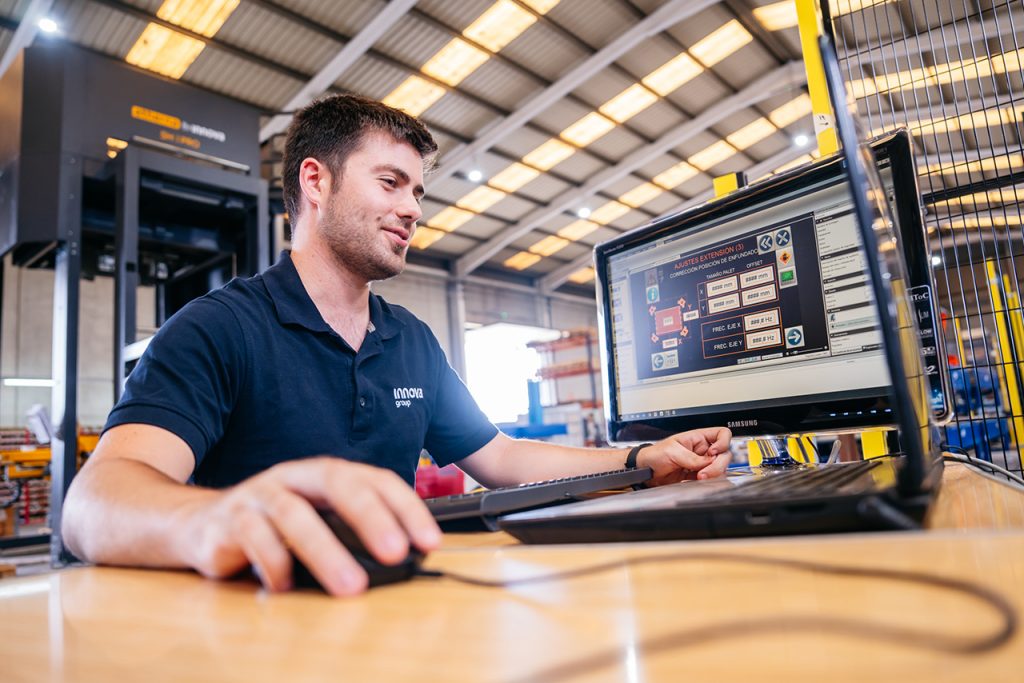
To achieve this standardization in our programming processes, it is essential to be methodical and follow both indicator controls and intra- and interdepartmental communication.
For instance, within our Technical Office department, we conduct regular meetings, keep records, and oversee the maintenance of machinery, systems, and interdepartmental communication.. “This allows us to maximize final results with impeccable efficiency, as well as implement updates or make modifications to the machines much faster and cleaner, and ultimately create a more conducive environment for innovation,” says Raúl, one of those responsible for ensuring the continuity of this methodology at Innova.
Advantages of Standardization for the Final Client
And how does this affect the final client company or the operator who must handle our packaging systems? There is a vast difference between systems and packaging lines designed with a specific methodology or without processes.
For example, the advantages of systems developed in a standardized manner:
- During Machinery Startup and Comissioning: Faster and clearer consensus with the client’s system.
- During Line Operation: Easier and more agile communication with the client’s own systems, including management systems and ERPs.
- Faster and More Efficient Troubleshooting: All our operators follow a standard system and have access to all the documentation methodically stored for each system.
- Easier Maintenance, Spare Parts, and Technical Support: Thanks to the same documentation and standard systems procedure.
- Longer Machinery Life: Ultimately, this type of methodology contributes to extending the useful life of the equipment, thanks to more effective maintenance and problem resolution.
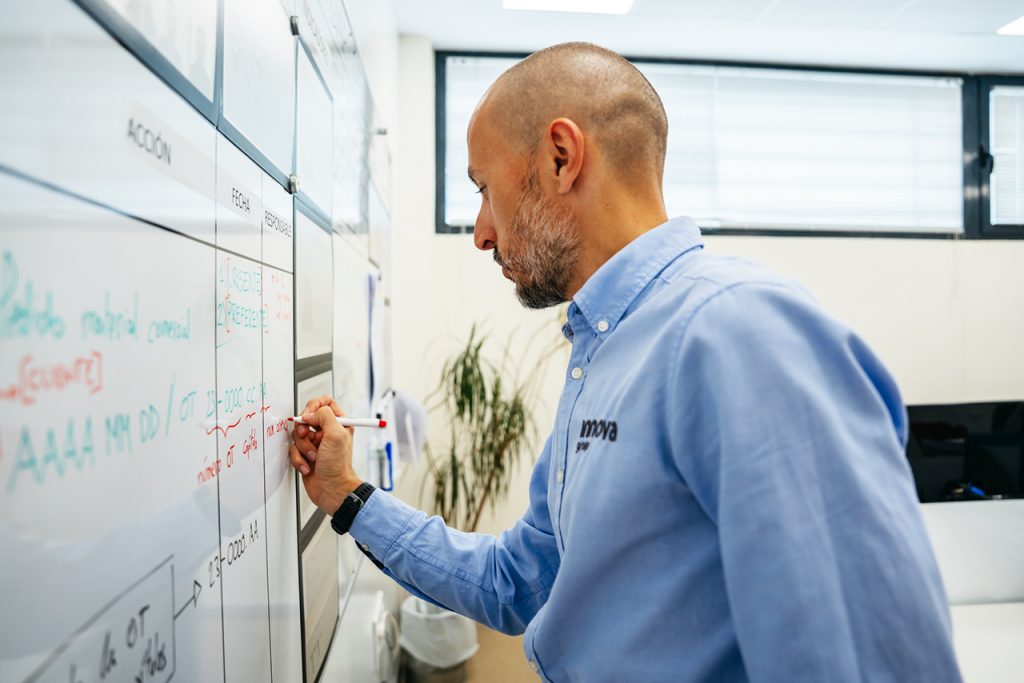
In summary, Innova’s experience with process standardization has shown us that this tool can be a powerful ally for companies seeking to improve efficiency and drive innovation. We are convinced that standardization, when implemented intelligently and strategically, can be a key factor in the growth and competitiveness of any organization.
At Innova, with over 20 years of experience in designing and developing packaging machinery, we can advise you on how to choose the end-of-line system that best suits your company. Feel free to consult our technical sales team without obligation.
Do you like our technical posts about trends and methodologies in packaging systems? We invite you to subscribe to our monthly technical Newsletter!