How to protect fragile loads with Automatic Packaging Systems
Achieving maximum protection for fragile products and delicate materials through automated packaging solutions, reducing costs, and promoting sustainability poses a significant challenge for the industry. These types of loads are extremely prone to damage during transport and storage. A breakage or even a slight abrasion can cause significant losses, both for the producing company and the end customer. For this reason, it is essential to work with effective packaging systems that guarantee these materials’ integrity and total protection, from the moment they leave the production line until they reach their destination.
Fragile goods are not only ceramics or glass but also household appliances and electronic equipment that need extra protection. These loads need to be palletized for shipment and may require additional protection using various packaging systems. How can we minimize the extra cost of safeguarding highly sensitive loads? One example involves Innova’s customer ITV Ice Makers, an international manufacturer of ice machines and refrigeration equipment. The company transitioned from using excessive cardboard to secure its loads, to implementing a Stretch Hood packaging system. This change enabled the company to optimize its packaging process, decrease its packaging consumables, and enhance product presentation.
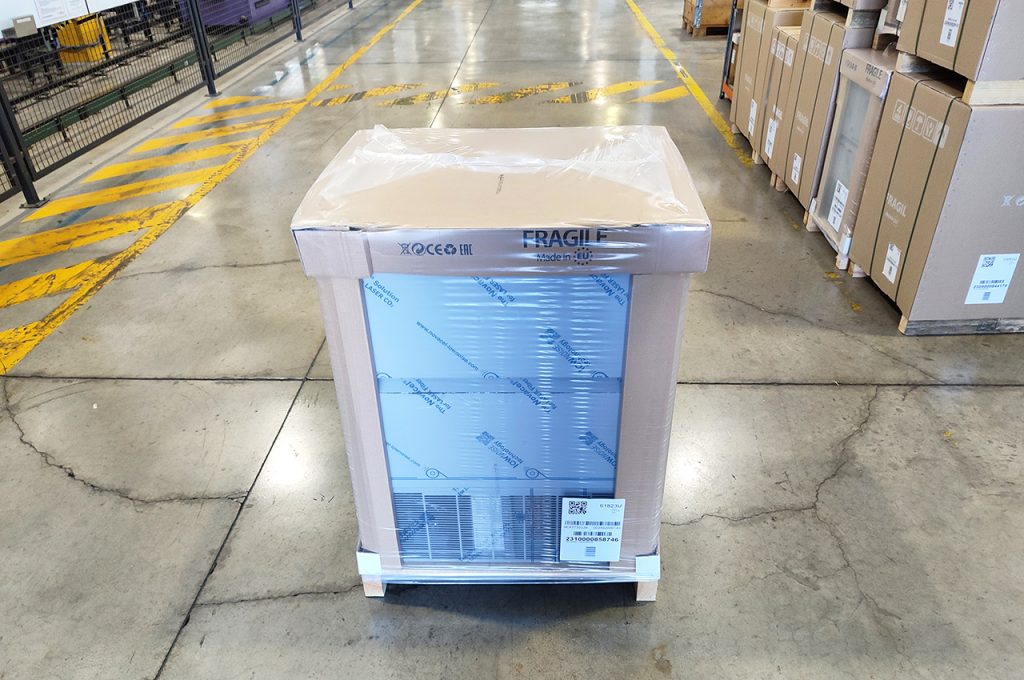
Problems of fragile products in storage and transport
What is considered a fragile product?
A fragile product tends to break rather than deform, i.e. it is the opposite of ductile. Examples of fragile products are glass or ceramic panels, which, although different in composition, both have the characteristic that when they reach their resistance limit, they break completely. Household appliances or electronic products, such as refrigerators or televisions, are also considered fragile, as they are also delicate and prone to damage if they receive a bad shock.
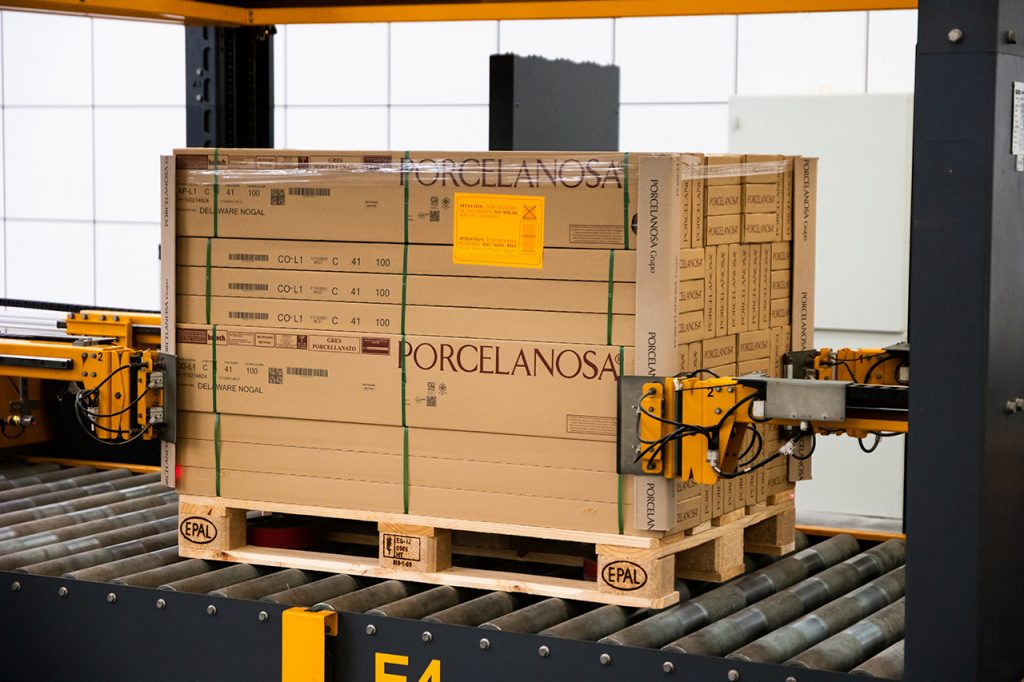
Problems and challenges of fragile products
During the transportation and storage of delicate products, various issues can arise. The following are some of the most common challenges that must be addressed through suitable packaging systems:
- Securing the load to the pallet
Fragile products are extremely susceptible to damage from impact and vibration during transport. Pallet securing is essential to keep the load compact and avoid sudden shocks.
- Instability and shifting of pallet content
Instability can cause tipping and shifting, causing irreparable damage to the load. It is necessary to use a suitable packaging system that provides a firm hold to prevent this.
- Manual application: Weak securing
Manual application of pallet securing can result in weak or inconsistent securing, increasing the risk of damage. A single error can influence the overall safety of the load and cause irreparable losses.
- High cost of packaging
Excessive use of additional materials such as wood, metal frames, or other protective systems can significantly increase the final price of packaging. For this reason, it is essential to implement palletizing systems that are efficient and minimize the use of other reinforcement materials.
- Lack of automation
Any company with a high level of production needs an automated end-of-line process to respond to the production flow. Manual packaging processes, often involving additional product protection, become a bottleneck in the factory, limiting production capacity and delaying the shipment of loads.
Packaging systems for fragile loads
Fragile goods need a robust packaging to mitigate the potential for breakage during transit. Adequate fixation of the material is crucial to counteract the friction generated by movement and prevent loss of the entire load. At Innova, with more than 20 years of experience in the manufacture of packaging systems, we present you the most effective solutions for the total protection of these materials.
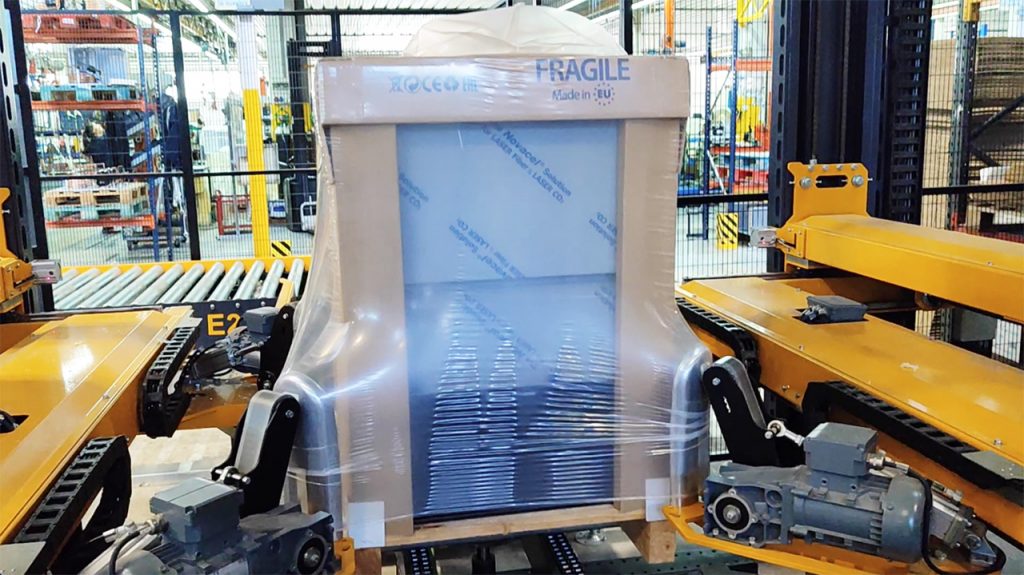
1. Strapping systems: securing and compaction
Automatic pallet strapping systems are and will continue to be one of the most versatile and commonly used solutions for securing and stabilizing loads, due to their ease of application and multitude of versions, from manual to fully automated equipment.
The horizontal strapping machine compacts and laterally secures loads, while the vertical strapping machine provides stability and total fixation to the base of the pallet for transport and storage. The strapping of the vertical and horizontal strapping machines does not negatively affect the loading of this type of products, since they are usually placed inside boxes. In addition, the strapping machine can apply cardboard corners to make the load more secure and avoid possible damage.
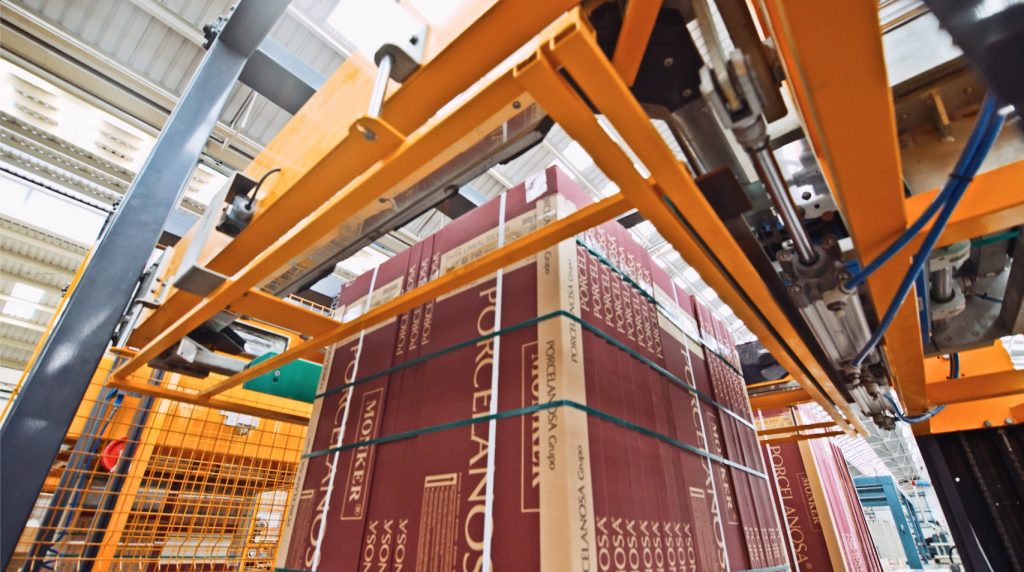
2. Stretch wrapping systems: Uniform protection of the load
Pallet wrapping machines ensure uniform protection around the entire load, which greatly reduces the risk of damage during transport and storage. It is essential that pallets carrying fragile loads are stable and that there is no movement inside the pallet. For example, if a load of ceramic boxes is not completely fixed, they could collide with each other and break, completely wasting the product.
This is why pallet stretch wrappers are such a useful solution, as they also have the possibility of adding additional accessories, such as a top cover applicator, cardboard edge protectors for increased protection, or the elastic cord or reinforcement roping system. The latter offers an extra fixation similar to the strapping application and helps to compact delicate loads into a single block.
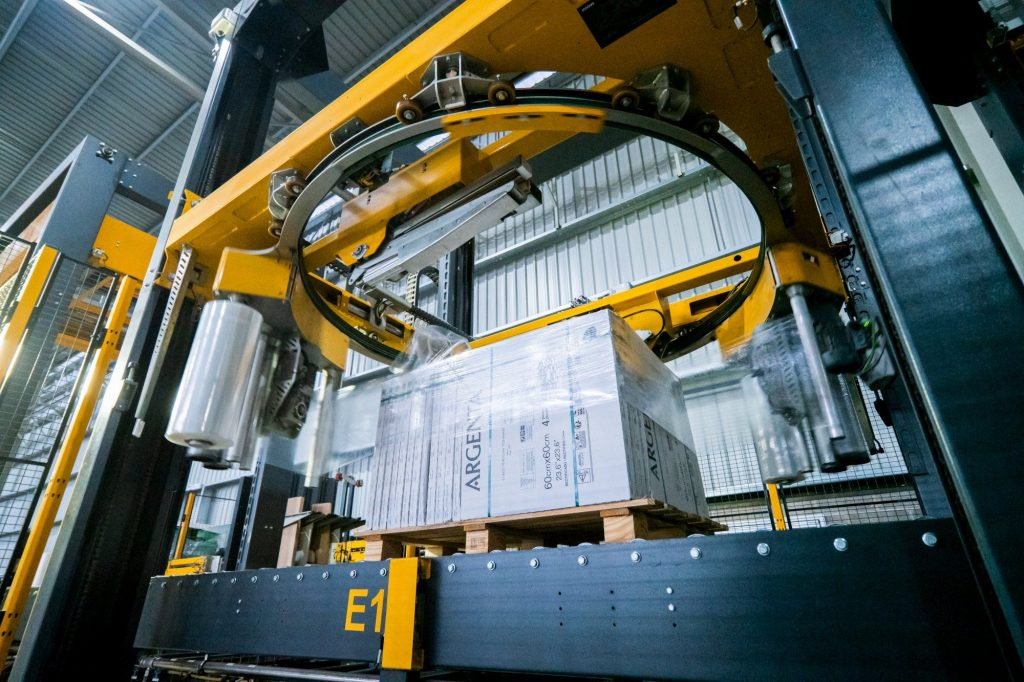
3. Stretch Hood: protection and securing
“Various packaging systems are available on the market, all of which provide excellent protection for delicate materials and fragile products. However, at Innova, as packaging system experts, we consider the Stretch Hood packaging system to be superior to all others.”
The Stretch Hood wrapping system guarantees the best protection for any type of load, including those that are extremely delicate. The film’s hooding and characteristics allow it to adapt perfectly to the load. This provides a firm hold, minimizing pallet movement and reducing the risk of tipping or shifting during transport. While the application and result may differ, the Stretch Hood system offers similar stability to the stretch wrapper.
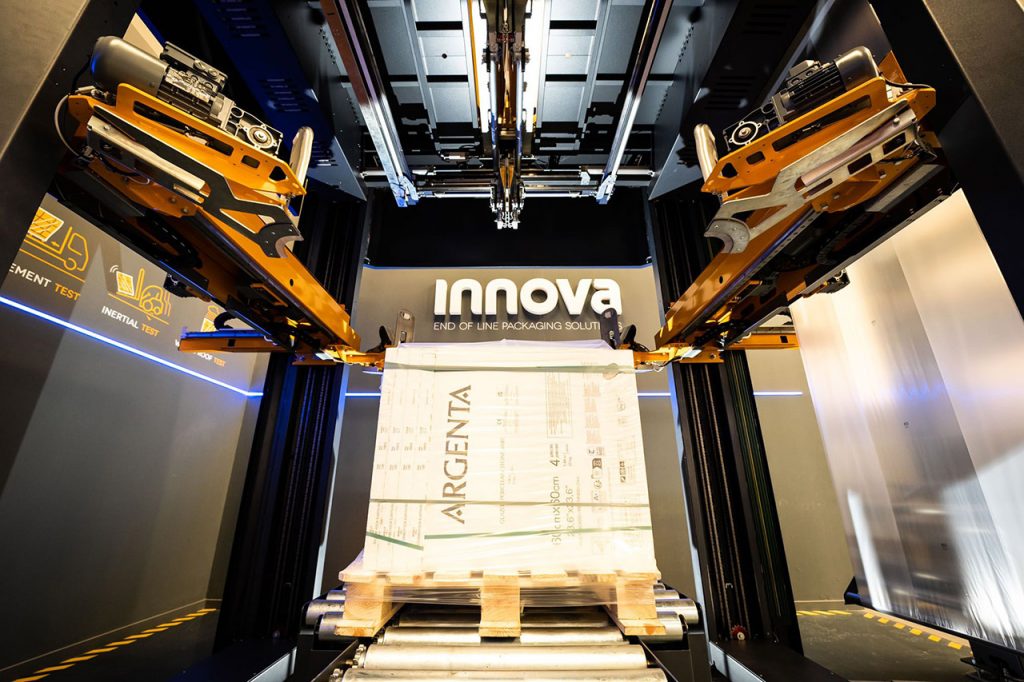
One of the most differential points of the Stretch Hood compared to the wrapping machine is that the Stretch Hood guarantees total watertightness and protection against external agents such as dust or humidity, which is very important to prevent these fragile products from being damaged. For example, in the case of a glass load, as demonstrated by our customer Crisa Libbey Mexico, who specializes in glassware, dinnerware, flatware, and others.
The Stretch Hood has the capability to handle the high production rates of the household appliance industry, wrapping 120 pallets per hour. Additionally, it is an efficient and environmentally friendly solution, reducing consumables and energy costs by up to 50%.
In the following video, you can see how this system reduced the packaging for our refrigerator and ice machine customer, ITV – Ice Makers.
4. Shrink-Hood System: Adhesion and Protection
Another packaging solution for products with fragile characteristics is the heat shrink system, which is an automatic pallet wrapper presented as an alternative to the Stretch Hood as the final finish is similar.
This packaging solution includes a hooding machine and a film heat-shrinking system at 280ºC, which securely fixes and attaches the load to the pallet, facilitating transportation and handling. The film adheres to the pallet with the application of heat, protecting it from external agents. Although the heat shrink system is not as sustainable as the Stretch Hood, due to the installation of the shrink oven and the use of thicker consumables, its final finish also protects and secures fragile loads excellently.
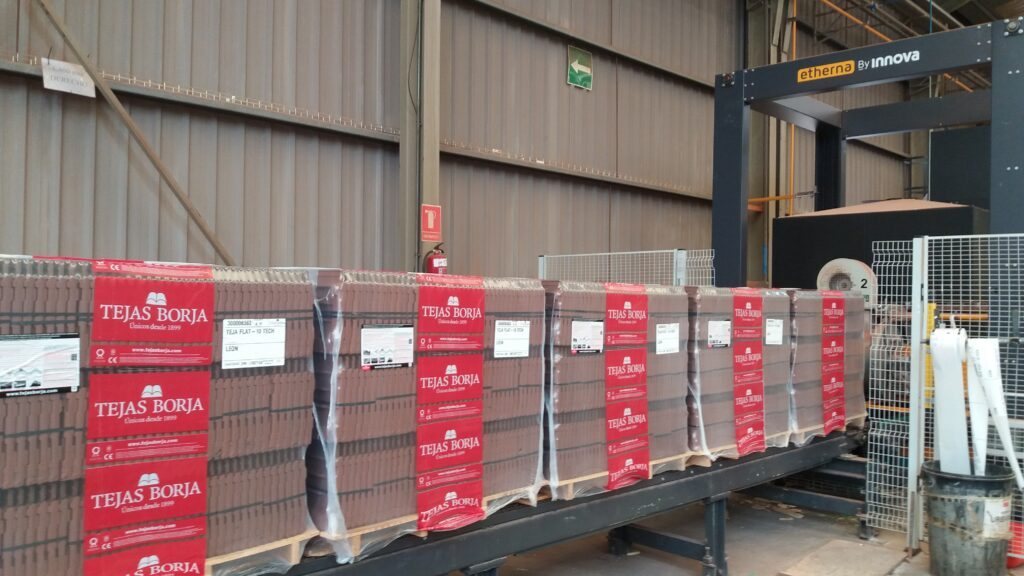
In summary, to protect fragile product loads correctly, it is essential to choose the right packaging system. Good packaging can protect goods from the time they leave the factory until they are received by the end consumer. This helps avoid displacement, falls, and vibrations during transport. In this article, we have shown some of the most advanced end-of-line solutions, which ensure the total protection of this type of delicate material.
At Innova, with over 20 years of experience in the manufacture of packaging systems, we can advise you on the choice and optimization of your end-of-line system. Our team of experts is ready to help you protect your fragile products with innovative and customized solutions. Contact us without obligation and find out how we can optimize your supply chain with efficient and secure packaging, ensuring the integrity of your goods from production to final delivery.