How to choose between a semiautomatic and an automatic Stretch Wrapper
What type of stretch wrapping machine do I need for my product? Should I opt for an automatic option? Are the features offered by a semi-automatic pallet wrapper sufficient for my packaging needs? The choice between a semi-automatic and an automatic pallet stretch wrapper is not just a matter of budget, it is a strategic decision for every company that wants to improve its packaging process. At the time to choose between a semiautomatic or automatic system, it is necessary to consider factors like packaging objectives, our industry requirements, and the specific characteristics of our product (and our automatic packaging line). In this article, we will analyze the differences between both types of wrapping machines and we will address specific recommendations according to the industry and the type of product.
There is a wide range of wrapping machines in the market, with different functionalities and objectives. Both automatic and semiautomatic stretch wrappers have features and accessories according to the wrapping needs. How can we determine which option is more efficient for our product, in addition to the budget? We have to consider variables like production, workforce availability or working time, among others.
Packaging objectives and stretch wrapper features
It is essential to begin with a company evaluation and identify the objectives that our wrapping machine will have. We believe there are three key aspects to consider:
- Production: If production is less than 10 pallets/hour, a semiautomatic wrapping machine is a good option.
- Budget: In the case that the budget is limited, we also recommend a semiautomatic machine, even though the price varies according to the equipment characteristics.
- Objectives of packaging (securing and protection): When the needs of the packaging are to achieve greater support and protection, it is recommended to look for wrappers with more features such as a pre-stretch system, adjustable tension, and cover application, among others.
In addition to these three essentials, there are also other secondary factors to consider, such as the installation process, factory automation level, adaptability needs, and more.
- The available working space: The available space at the facility or warehouse is an importante factor for the selection of the type of wrapping machine. If the space is limited, a semiautomatic stretch wrapping system may be the best option.
- Need for automation: This is when a company opts for an automatic stretch wrapper solution to increase production, productivity, and efficiency, or reduce manual and semi-automatic workload.
- Factory safety: One of the main reasons for choosing an automatic packaging system is the need to improve safety, both in the factory and for the personnel, depending on the level of risk associated with handling the equipment and the workload of the staff.
- Adaptability to sizes and formats: It is important to take into account the shape and size of the products to choose a stretch wrapper with more or less features. For instance, in situations where loads are heavy, fragile, or unstable, it is recommended to use a robust automatic stretch wrapper that can provide a more secure wrapping.
- Industry requirements: The logistical and regulatory needs a company faces may require a packaging system with higher performance and automation. For example, cargo transport regulations require greater pallet securing, or certain sectors must use a cover system to protect the goods, etc.
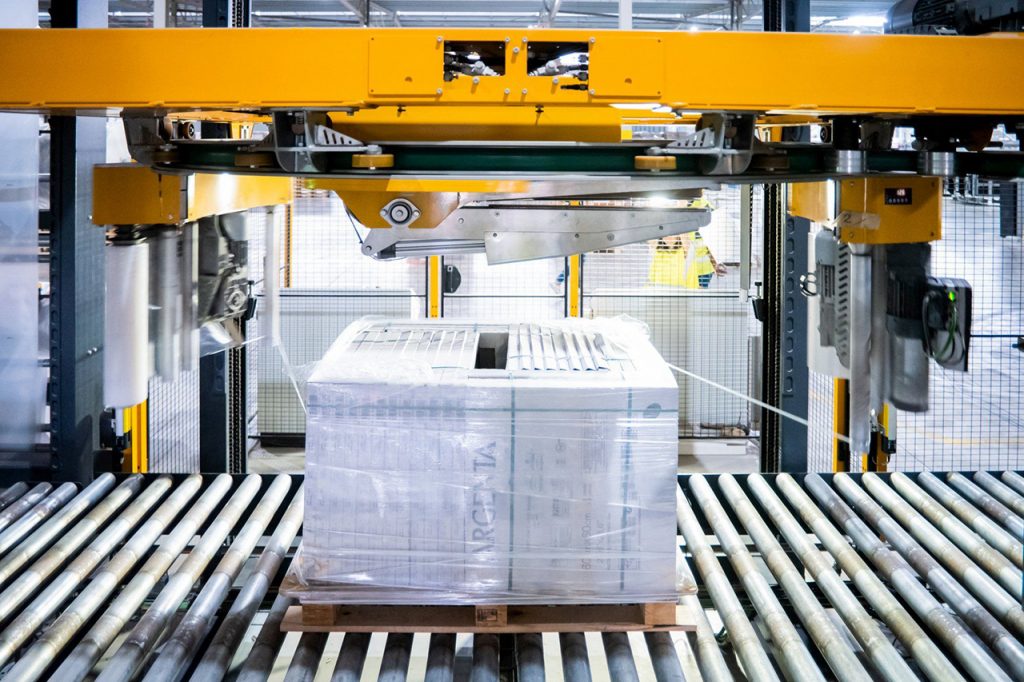
Wrapping machine types and use cases
Let’s delve into more specific cases in which a semiautomatic or automatic stretch wrapper is recommended, according to our experience of more than 20 years of manufacturing and installing wrapping machines of all types.
When to use a semiautomatic stretch wrapper
A semiautomatic stretch wrapper is perfect for small companies with low production. They can be installed anywhere in the factory and allow to wrap pallets quickly and efficiently without the need for a large investment.
This type of semiautomatic stretch wrapper is very versatile in terms of different types and shapes of loads. For example, wrapping all types of goods, with or without pallets, is possible with a semiautomatic wrapper without an automated line or a palletized load.
The semiautomatic wrapper machine is suitable for all types of products, and is particularly suitable for:
- Products of different sizes and shapes: It adapts to the specific contour of the loads.
- Picking loads: For uneven loads, without standard formats, semiautomatic stretch wrapping can be a good option in cases of low production, as it allows greater flexibility.
- Light loads transported with a pallet truck: These types of loads cannot usually be placed on an automated conveyor line or the conveyors must be adapted to these loading vehicles. For this reason, many companies opt for a semiautomatic stretch wrapper with low-profile access.
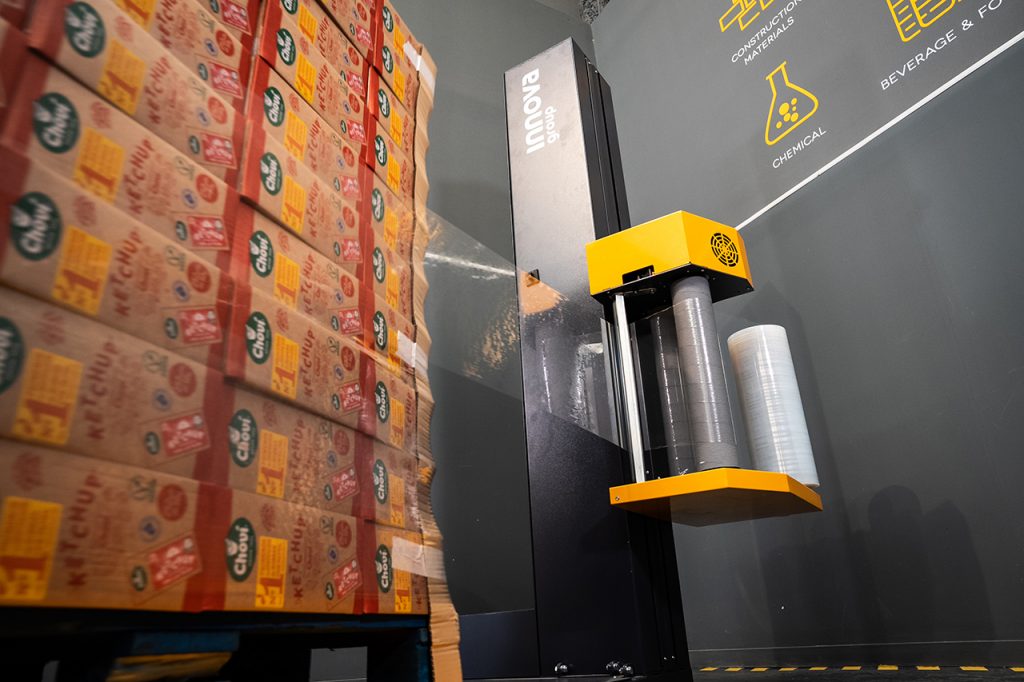
In terms of flexibility, semiautomatic stretch wrappers come usually with a wide range of accessories and options that make them highly suitable for variable production environments. Their ability for manual adjustments, quick format changes, and compatibility with a variety of packaging materials make them a versatile option for companies that require adaptability in their packaging processes.
When to use an automatic stretch wrapper
Automatic wrappers are designed to withstand high levels of load and work. Of course, they will require a higher initial investment, but the results, ROI, and benefits in time and workforce will be much greater in the medium and long term.
Automatic stretch wrappers are widely used by large companies in the food, chemical, and construction sectors, where automation, speed, and safety are required. They are particularly efficient for the handling of:
- Heavy products: The automatic stretch wrapper can handle heavier weights than the semiautomatic one, as it comes with a more robust workframe.
- Bulky products: It enables a secure, quick and effecting wrapping of large loads.
- Fragile products: The automatic Rotary Arm or Ring stretch wrappers provide greater stability for fragile products since the wrapping film carriage rotates around the load, and it is not the load itself that rotates, as in the case of turntable stretch wrappers.
- High production: Precisely the main key of the automatic solutions is to respond to the high production of the company at the end of the line.
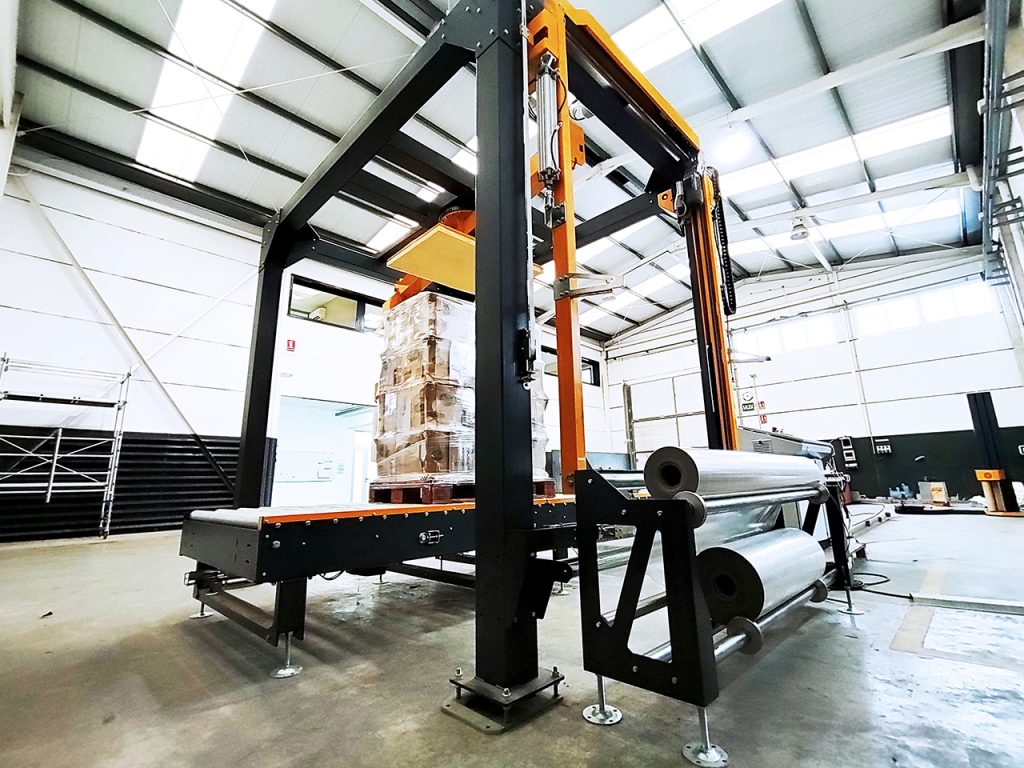
Automatic stretch wrappers usually require less specific skills by the facility personnel to operate them, as most functions are automated and usually only human input is required for film changeovers. This can be beneficial if the company aims to simplify the packaging process, reduce human error, and avoid workplace accidents that can harm workers’ health, cause product loss, and damage.
Another very important aspect to consider is film consumption. Automatic wrappers tend to be more efficient since they use less film with precise control, parameter programming, and optimal film cutting and welding systems. In the case of Innova’s automatic stretch wrappers, for example, they have a torque control system that optimizes and reduces film consumption to a minimum. Moreover, all automatic stretch wrappers usually include a film pre-stretching system of about 200-300%, allowing further savings in consumables.
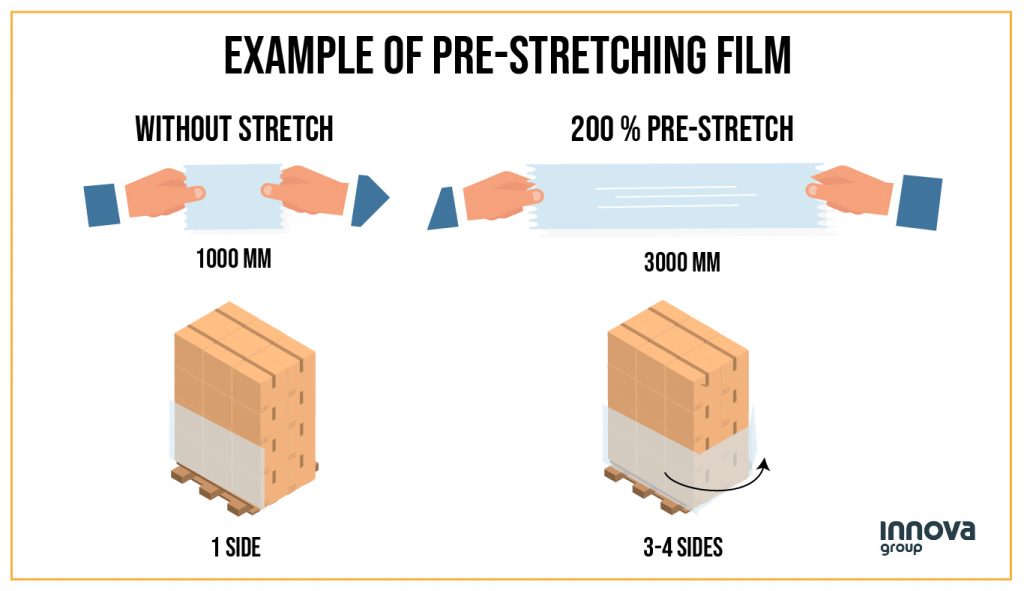
Film reduction in wrapping is a key feature of automatic systems, as they are more sustainable from an economic and environmental point of view.
In summary, the choice between a semiautomatic and an automatic wrapper is a strategic decision that must be based on a careful assessment of the company’s needs, as well as considerations about the type of product, available workspace, personnel safety, and flexibility required in the packaging processes. Both options have their advantages and disadvantages, and the final decision must take into account the balance between efficiency, productivity, operating costs, and specific business requirements.
At Innova, with more than 20 years of experience designing, manufacturing, and installing all types pallet wrappers, we can offer you a consultation without commitment regarding the best option for your product. Contact our technical team, we will be happy to hear and assist about your packaging project!
Do you like this technical article? Don’t hesitate to subscribe to our monthly newsletter for more articles, news and trends in packaging and logistics.
SUBSCRIBE