Top tips to improve your ROI with pallet packaging automation
The packaging line is undoubtedly one of the pillars for the productivity and success of a manufacturing company, as it is responsible for the protection and safe delivery of the product to customers. The total automation of the end-of-line plays a fundamental role here since it guarantees its performance and eliminates problems and rework of manual packaging. Yet many companies ask us, when is it profitable to automate? What is an automated packaging systems ROI (return on investment)? Although the initial costs of automating may seem high, assessing the ROI always makes it a smart investment.
In today’s article, we review the keys to improving the ROI of automating the end of line.
The relationship between ROI and automation
Regardless of how simple or complex is the automatic packaging system purchased, all types of end-of-line automation always provide a return on investment. This includes factors such as labor cost savings, reduced use of materials and consumables, improved worker safety and equipment efficiency, among others. All in all, automating the final packaging allows to achieve a quite remarkable ROI and on many occasions even to pay off equipment such as the Stretch Hood system in just 6-9 months, according to studies comparing with manual or semi-automatic systems.
Savings in labor costs
Did you know that 60% of total packaging costs are directly related to labor? According to the U.S. Bureau of Labor Statistics, this number is even growing, and all indications are that labor costs will continue to rise. What can your company do to mitigate these ever-increasing costs? The answer lies in automation.
For example, just comparing manual versus automatic packaging process packaging times, according to studies conducted by Innova:
- A company that wraps about 300 pallets daily would need between 6-8 employees performing manual wrapping (2-3 employees per 8h shift, for a total of 3 shifts per day).
- Performing the same packaging of 300 pallets with a system such as Stretch Hood would require only 1 employee supervising the machine each shift.
Packaging automation allows line personnel to focus on more complex and supervisory work, rather than routine, repetitive tasks that can lead to physical injury during manual pallet wrapping or strapping.
Reduction in packaging consumables
The great key point of automatic packaging systems is that they reduce the use of consumables to a minimum thanks to the precision of the technology. The cost of consumables must also be taken into account, depending on whether the format is for manual or automatic packaging. Film, strap, or sealing tape reels for manual application tend to be smaller and have a higher cost per kg /lb than consumables for automatic systems. Shorter consumable life also means that consumables need to be changed more often, wasting time and resources.
A clear example of technology versus the human factor is the stretch wrapper film:
- One person can manually pre-stretch 10-15%.
- A standard pallet stretch wrapper would pre-stretch 300% or more.
At Innova, we conduct packaging consumption studies to determine the ROI of automating this process. According to a study conducted with Innova customers, with a pallet of stacked boxes measuring 35 x 35 x 66 inches (900 x 900 x 1700 mm) and a production of 300 pallets/day:
- Applying manual strapping had a daily cost of $270 / €255.
- By using an automatic strapping system, the cost of strapping was reduced by up to 45%, i.e. $154 / €145 per day.
And in the case of film, the savings are even greater:
- Applying film and manual heat shrinking had a daily cost of $1,378 / €1,300 (between film and gas).
- Using the Stretch Hood system, the cost of the film was reduced by 51% to only $680 / €640 per day.
As we can see, automatic packaging systems are more efficient and accurate than manual packaging, where human error also counts and where less material is required to achieve the same result. By reducing the total amount of material used by the company on a daily basis, the company will be able to increase that expected ROI.
Elimination of work-related accidents
Another key point of automation is the safety of workers and the reduction of occupational accidents, worker injuries, and other consequences. This aspect clearly has a double aspect for the company: the worker’s own physical safety, where an accident or physical injury can result in sick leave for the company (and consequently the consequences of such sick leave for the company), and in the production losses generated by accidents on the packaging line, in the case of damage to the goods.
Automated packaging equipment helps reduce workplace accidents by keeping workers out of the most dangerous areas of the line and avoiding manual tasks that can lead to injuries or accidents.
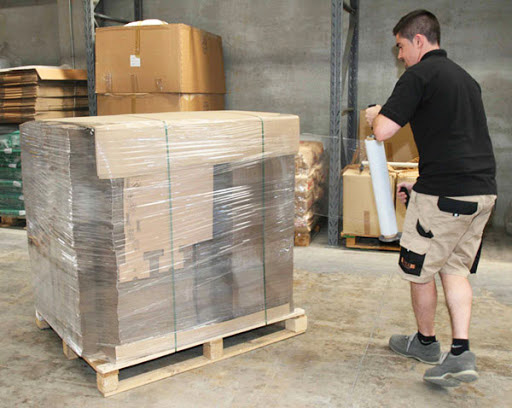
Instead, the new technician for the automated line is a profile specialized in operating the packaging equipment and performing tasks such as consumable changeovers and essential maintenance.
Resolving industrial accidents related to end-of-line and logistics is in the hands of the companies, and together with the Workplace Risk Plan, end-of-line automation is key to reducing and improving the safety of workers and the company.
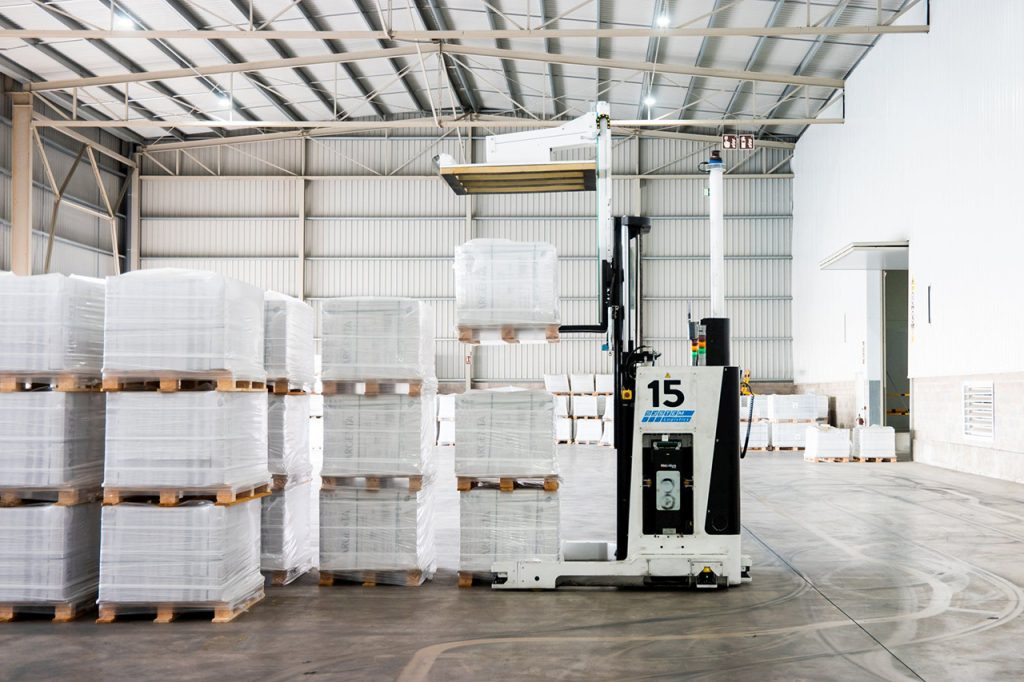
Improve equipment efficiency
Finally, a further step in packaging automation is to review and improve the efficiency of the equipment, in order to obtain even better ROI from them. In this case, we are talking about continuous improvement indicators such as OEE (Overall Equipment Effectiveness) and obvious measures such as a reliable preventive maintenance plan, which every company with automated equipment should take into account.
Some of the essential actions to obtain a better performance of the equipment:
1. Reduction of avoidable downtime:
We are talking about consumable changes, personnel shift changes, etc. An automated system that allows consumable replacements to be carried out in less time, or that directly has a greater packaging autonomy. This would be the example of the Stretch Hood system that allows wrapping around 1,000 pallets without changing the film reel (versus a standard stretch wrapper that needs film changes every 150-200 pallets).
2. Reduction of failures due to the packaging system:
Either through a preventive maintenance plan or by renewing the system itself in the case of obsolete or underperforming equipment. Investing in automated packaging systems with greater functionality and reliability, and a good maintenance plan that accompanies them throughout their useful life, will yield a higher ROI than investing in low performance equipment (and usually lower price).
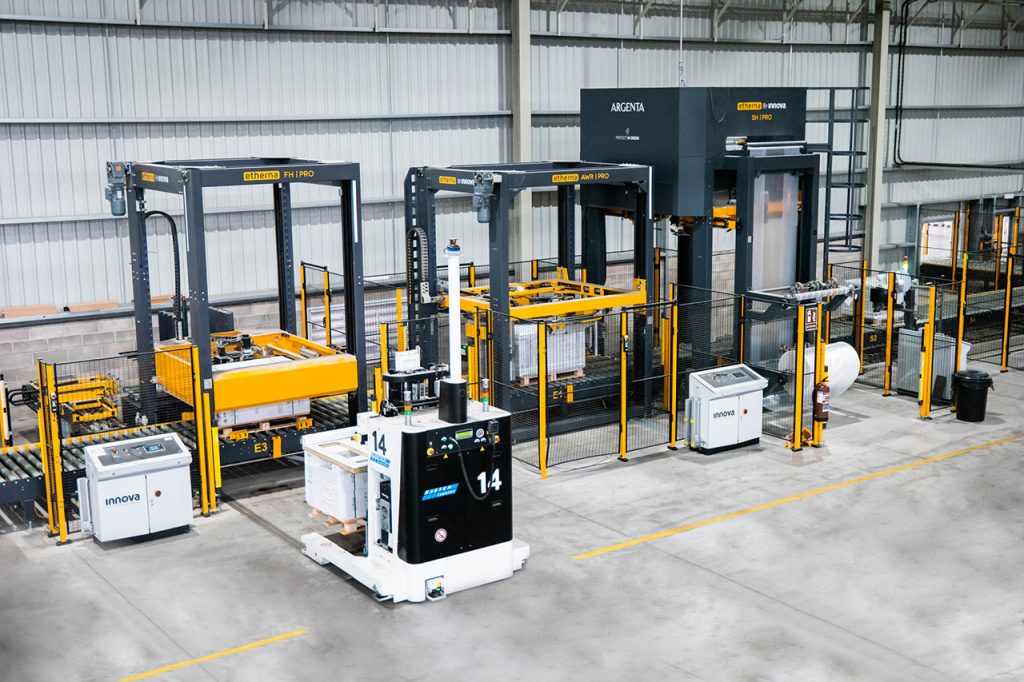
3. Packaging project prepared for forecasted productive growth:
Another interesting aspect is to invest in packaging line equipment that responds to the company’s production needs in the future. Either with a planned production increase or simply to adapt to different formats of the line or different needs.
Some examples of packaging lines with production forecasts:
- A system with a higher packaging capacity, even if it is lower at the moment.
- Conveyor lines adapted to different pallet vehicles such as forklifts, AGV, etc.
- Packaging systems that allow multi-format pallets with different sizes, different types of film, etc. (such as our Stretch Hood XL for Large Formats which can use 3-4 reels to adapt to different formats).
For more information on how to improve machinery performance, and in particular the OEE indicator, we recommend our article on the subject:
In short, the arguments in favor of automation in packaging are extensive and the benefits of doing so are very visible to the production company. When making an investment in machinery it is important to look at all these aspects and calculate the ROI that it can provide, both the one that is visible at first sight (savings in consumables for example) and the one that is not (reduction of accidents at work, better delivery of goods to the customer, preparation for the growth development of the company, etc.).
At Innova Group we have experience with hundreds of automated end-of-line projects and we have a team specialized in carrying out studies of consumables and savings in automation. Do not hesitate to contact our team for a quote and/or study without obligation, we will be happy to assist you.
Interested in our technical articles? Subscribe to our monthly technical newsletter on logistics and packaging:
SUBSCRIBE: