How to Reduce Losses in Freight Transportation Caused by Packaging Damage
In an increasingly globalized and regulated logistics landscape, reducing damage and losses of goods during transportation has become mandatory. With the rise in international requirements and new regulations in the supply chain, ensuring the integrity of products during their transport is the ultimate goal of final packaging systems. But what percentage of losses are caused by problems or failures in the packaging itself? Even though packaging machinery aims to secure the cargo, it often results in failures that lead to not only damaged products but also significant additional costs for the company.
This article will explore how to tackle this logistical challenge, examining the most common cost losses due to packaging failures and how to effectively reduce them.
Common Losses Caused by Packaging Failures
Let’s go over all the aspects where a company could lose profitability due to packaging issues.
1. Damaged or Defective Products
One of the most obvious and costly losses is the damage that products can suffer during transportation. This includes not only products that are spoiled or broken directly due to instability (such as load shifting, spills, product falls, impacts on the packaging, etc.) but also products that have been damaged due to a lack of protection against external agents (rain or snow during transit, humidity, etc.).
How many pallets become unusable at the end of the month? How many product units suffer defects during handling and transportation? The company should analyze this data to determine the performance of the packaging system or logistics processes.
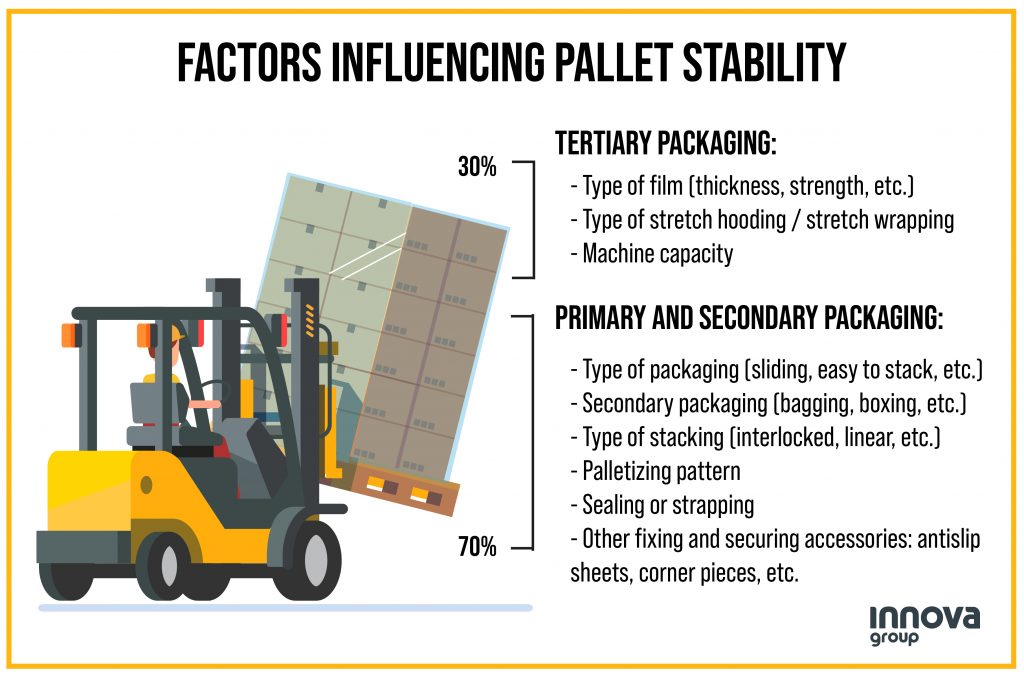
2. Additional Costs for Product Reshipment
It’s important to consider any extra expenses that may arise during the reshipment process when evaluating the financial impact of damaged products. Typically, these losses are linked to an order that must be completed and reshipped. This process involves various expenses, such as additional shipping costs, labor, and time spent on reorganizing and repackaging the damaged products. Reshipping can result in delayed deliveries, impacting customer satisfaction and leading to indirect costs such as canceled orders or reduced future sales.
3. Damaged Packaging Material
The packaging materials can also get damaged, such as stretch film or strapping, adding costs for unused packaging that didn’t fulfill its purpose. It is important to consider the extra amount of film required for repackaging when shipping a product.
In automated packaging systems, repackaging may not be costly as they’re designed to use minimal film/strapping. However, in processes that are either manual or semi-automated, there is a higher probability of errors occurring.
4. Additional Labor and Productivity Costs
Damaged products require additional resources and time for handling, repackaging, or repair. Once again, in automated end-of-line processes, occasional losses may not result in high costs. However, in semi-automated or older automated packaging systems, the cost of personnel and productivity for replenishing and repackaging can be much higher.
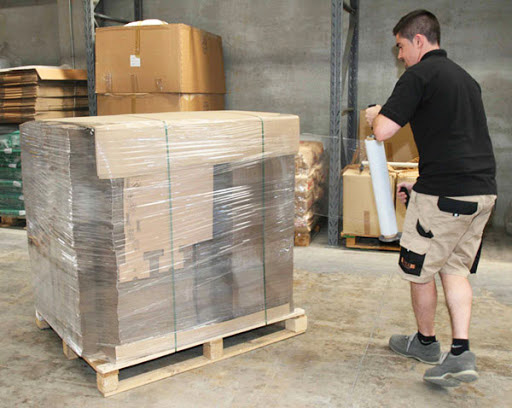
At this point, it’s crucial to review the entire packaging process to identify areas for optimization, whether it’s the packaging system itself or the packaging process.
5. Increased Shipping Insurance Costs for Products
The potential increase in shipping insurance costs due to frequent losses during transportation is another secondary cost. Insurance companies may view a company as a higher risk as claims for losses become more frequent.
6. Canceled Deliveries and Dissatisfied Customers
It’s important to consider not only the direct costs of product damage, but also the potential impact on customer satisfaction, cancellations, and the company’s reputation and future sales. When a customer receives a damaged product or experiences delayed delivery due to incidents during transport, their satisfaction level is compromised.
Therefore, minimizing losses during transportation not only results in immediate savings and operational efficiency but also plays a crucial role in preserving the company’s image and its ability to maintain and expand its customer base over time.
Calculating the Costs of Losses in Shipments
It is crucial to calculate the true cost of shipment losses to grasp the financial impact and implement effective reduction strategies. This involves considering all direct and indirect costs associated with damaged products, as mentioned earlier:
- Cost of damaged products
- Cost of affected transportation and the secondary transportation of reshipped products
- Cost of repackaging and preparing the goods again: consumables and used packaging systems, productivity time, etc.
- Cost of labor involved in the rework tasks
- Other secondary costs (increased insurance, order cancellations, etc.)
How to Reduce Losses with current or new Packaging Systems?
To enhance the protection of goods and mitigate losses, it is imperative to improve the packaging process. An evaluation of the current machinery should be conducted, and packaging systems should be renewed where necessary. This step will ensure that goods are transported with minimal damage, ultimately enhancing the efficiency and cost-effectiveness of the entire supply chain.
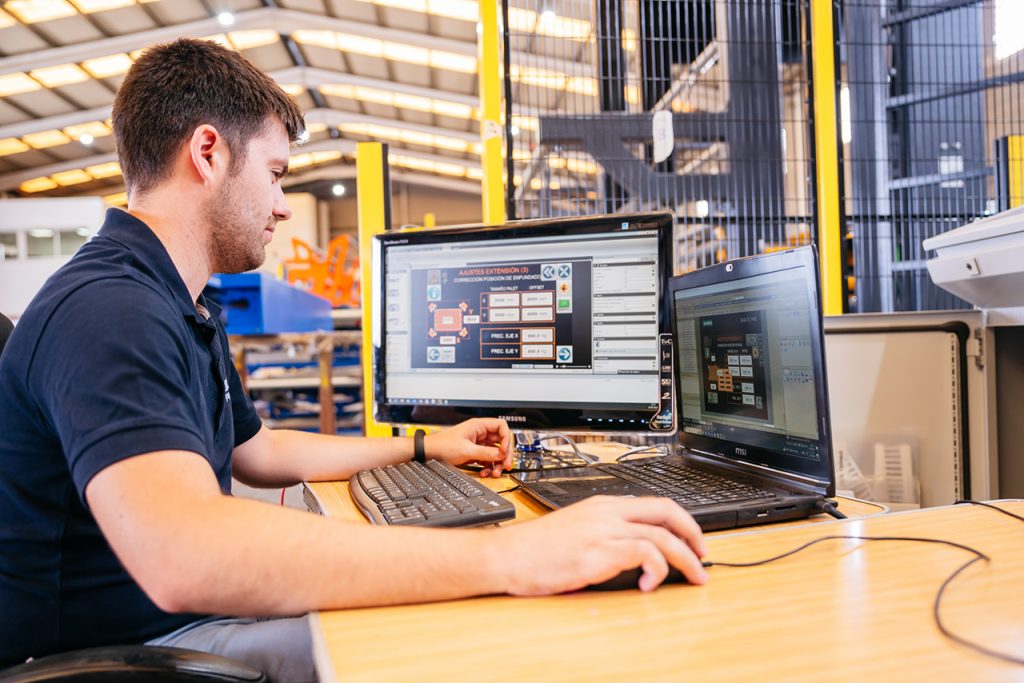
Evaluate and Optimize Existing Packaging Machinery
The first step is to analyze the current packaging process and systems to identify where pallet security is failing. Consider multiple aspects:
1. Evaluation of the packaging process:
Start by assessing the effectiveness of the packaging systems in use, whether they are semi-automated or automated. Maintenance, cleaning, programming updates, and packaging adjustments should be carried out as necessary.
2. Analysis of cargo securing and consumables used:
At this point, evaluate whether the tension of the consumable (whether strapping or stretch film used) is correct. Additionally, it’s important to assess whether the consumables being utilized are appropriate for the specific item being wrapped. For instance: Is strapping necessary if the product is already wrapped? Do we need additional protection if only a wrapping machine is used?
For this point we recommend you to read the following article in which we discuss types of packaging according to the protection objectives:
3. Determining the appropriate strapping or film specifications for the product
Choose the appropriate consumable specifications that best suit the packaging requirements of each product. This includes considering the characteristics of the film itself (if stretchable, pre-stretched, etc.), weight, recycled components, etc.
4. Regular Preventive Maintenance of Packaging Systems
It is important to schedule regular maintenance for packaging machines and equipment to ensure proper functioning and extend their lifespan. Two of every four packaging process failures are caused by inadequate maintenance and lack of lubrication.
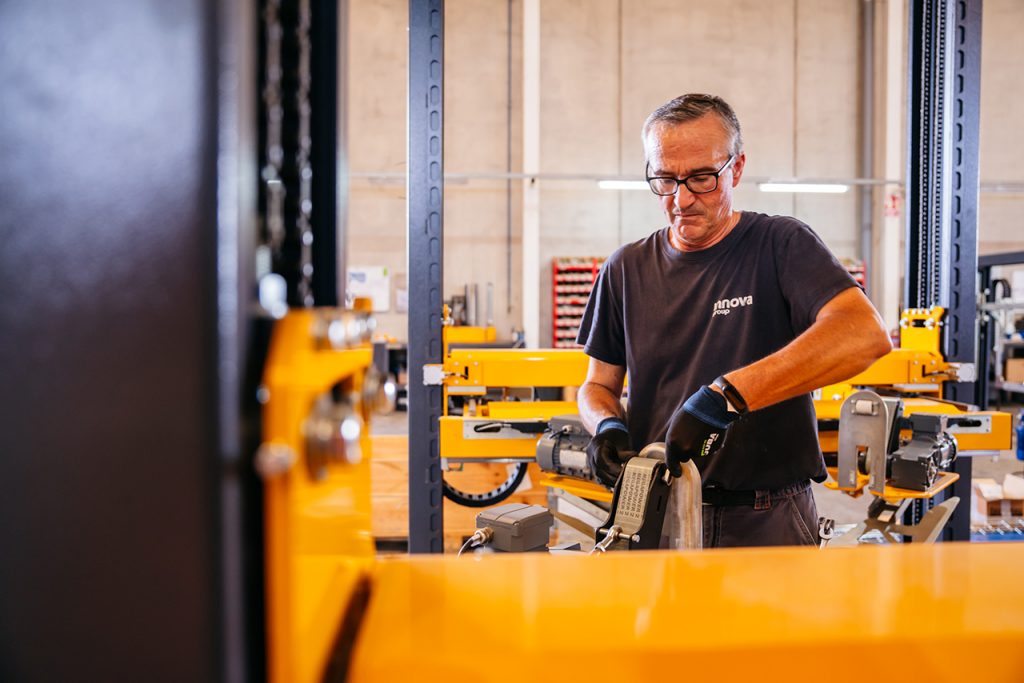
5. Tracking and Data Analysis at the End of the Line
To ensure the utmost accuracy and efficiency, it is highly recommended to incorporate tracking and data analysis systems at the end of the line, in conjunction with the measures already discussed. These systems allow for monitoring the packaging performance and collecting valuable information on damage incidents during transportation.
By keeping a comprehensive record of all issues encountered during transportation, we can identify patterns and trends and use the data collected to make continuous improvements to our packaging and transportation process. This will help us ensure that our products are delivered safely and efficiently to their intended destination.
Reducing Losses with New Packaging Systems
When end-of-line processes and packaging systems have become outdated or cause more problems than they solve, it’s undoubtedly time to change and upgrade the packaging systems. The shift toward complete automation and/or the renewal of more advanced systems is challenging to make, but the investment pays off quickly since it helps prevent damage and losses from the outset.
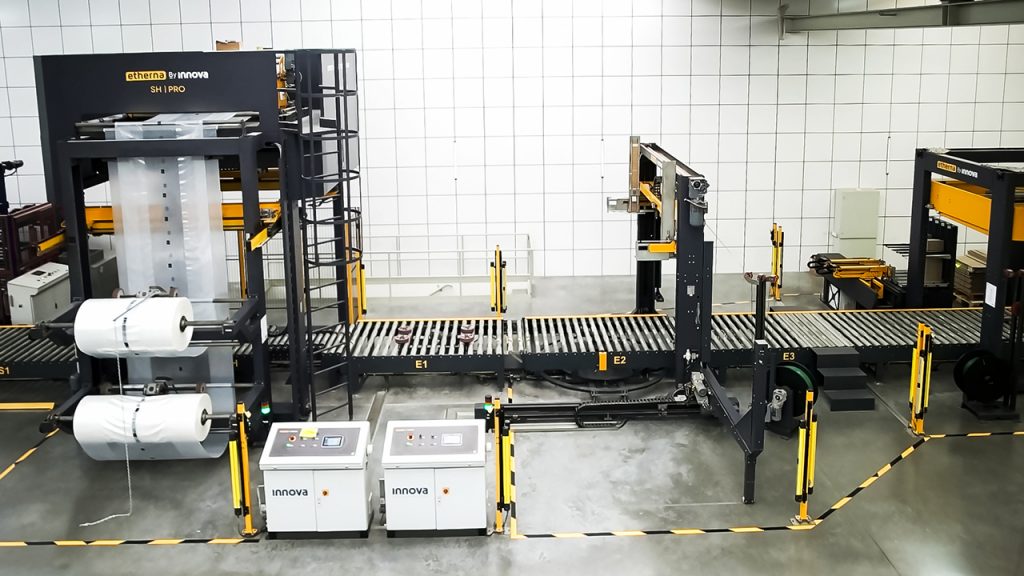
Examples of more modern packaging systems include high-performance stretch wrappers, such as automatic ring wrappers, and Stretch Hood systems, which offer greater protection and efficiency in packaging. At Innova, with over 20 years of experience as end-of-line equipment manufacturers, we can assist you in the process of upgrading your packaging systems.
Reducing losses in freight transportation due to packaging damage is essential for optimizing the supply chain and minimizing unnecessary costs. Evaluating and improving the packaging process, as well as investing in state-of-the-art packaging machinery and data tracking systems, are fundamental steps in achieving this goal and keeping customers satisfied. Please do not hesitate to contact us for guidance on how to optimize your packaging processes; we will be delighted to assist you.