Keys to a Smart Maintenance Plan (or How to Extend the Life of Your Packaging Systems)
Maintenance is one of the main components that ensures the proper functioning of machinery. But how can maintenance be applied to improve its performance further and extend the machine’s life? We often encounter factories where poorly maintained packaging systems lead to inefficient processes and results, creating an outdated appearance despite the relatively new equipment. Conversely, we visit factories with machines over 15 years old from Innova and other manufacturers, where the equipment works as well as it did on the first day. What’s the secret?
In this article, as manufacturers of packaging systems with 25 years of experience in maintenance services, we break down all aspects of preventive maintenance and how to implement it to avoid the degradation and obsolescence of the equipment.
Packaging Systems Like the First Day, with Preventive Maintenance
The goal of preventive maintenance is to detect and correct any potential problems before they cause a failure in the equipment, thus reducing downtime and the need for costly repairs. But it’s not just about preventing breakdowns; it also aims to prolong the equipment’s life cycle.
Implementing preventive maintenance on packaging machinery, such as Stretch Hood machines, stretch wrapping machines, and strapping machines, presents numerous benefits that directly impact the efficiency and productivity of packaging lines:
- Greater equipment reliability: By conducting regular inspections and maintenance tasks, potential problems can be identified and addressed before they cause failures. This helps ensure that equipment operates at maximum capacity and minimizes downtime.
- Extension of equipment life: Implementing a preventive maintenance program for packaging machinery is a smart investment for any company looking to improve equipment reliability, increase productivity, and reduce costs. Regularly inspecting and maintaining equipment ensures that it operates safely and efficiently, extending its lifespan.
- Reduced downtime: By identifying and solving problems before they cause a failure, downtime is minimized, maintaining uninterrupted production and thus avoiding losses for the company.
- Reduction in repair and replacement costs: Identifying and solving problems before they cause failures helps reduce long-term repair and replacement costs.
- Increased productivity: When equipment operates at maximum capacity, productivity increases, improving efficiency and reducing the need for overtime or additional resources.
- Compliance with safety standards: Keeping equipment in good working condition also helps comply with safety regulations, reducing the risk of accidents and incidents.
- Maintenance of product quality: Keeping equipment in optimal condition helps ensure that products meet customer expectations and industry standards.
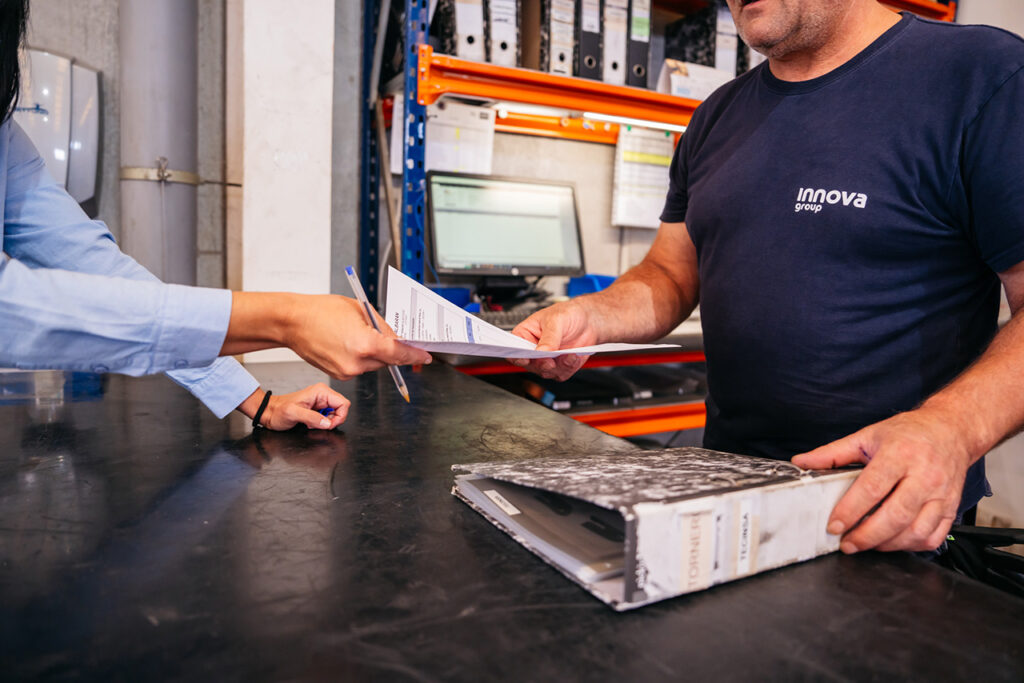
For more information on the efficiency of a packaging line, we recommend reading our article dedicated to measuring the OEE indicator, on equipment performance and efficiency:
How to Implement a Packaging Systems Maintenance Program?
Although the maintenance plan is often the manufacturer’s responsibility, the client or user of the equipment needs to know how these plans are carried out to better monitor and demand results.
Aspects to Implement a Maintenance Plan:
- Establish a time-based schedule: The frequency of maintenance for packaging equipment depends on the type of equipment, its usage environment, and usage level, and it can be based on a fixed schedule (weekly, monthly, quarterly, or annual…) or the actual use of the equipment by monitoring key performance indicators (KPIs). While the time-based approach establishes regular tasks such as inspection, cleaning, lubrication, and parts replacement, the usage-based approach allows for resource optimization by performing maintenance only when necessary, based on the equipment’s operational data.
- Define the maintenance plan: Specify the specific tasks that must be performed at each stage or interval of maintenance: cleaning, lubrication, adjustments, calibration, parts replacement, etc., or based on the results, as we have mentioned.
- Adapt the program to factory conditions: Environmental factors like humidity, dust, and chemicals can impact packaging machinery. Implement specific programs with protective coatings, special seals, or corrosion-resistant materials.
- Documentation and reporting: It is necessary to document all maintenance tasks performed, including the date, time, and any problems identified or resolved. This information is crucial for identifying failure patterns and evaluating the effectiveness of the maintenance program.
- Inventory management of parts: Maintain an inventory of spare parts and consumables available so that maintenance tasks can be carried out quickly and efficiently, minimizing downtime. For instance, at Innova, our spare parts service is managed by an advanced warehouse system that enhances the efficiency of support and maintenance services.
- Reporting 4.0 and predictive maintenance: Use data and 4.0 technology to monitor equipment performance and wear and predict when maintenance will be needed.
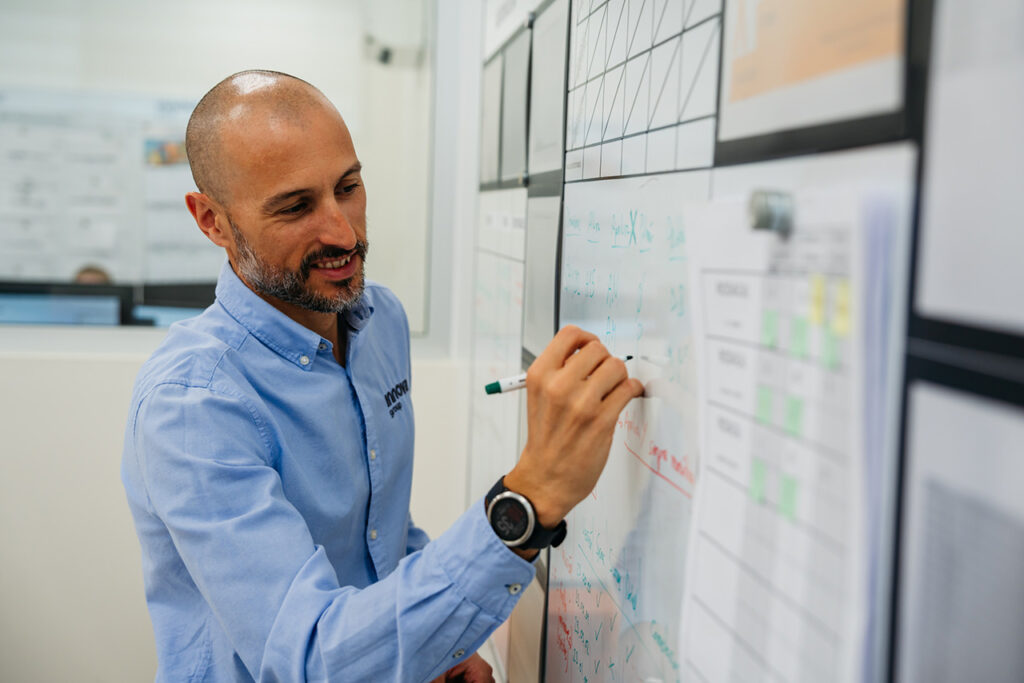
What Are the Typical Maintenance Tasks for Packaging Machinery?
In preventive maintenance of packaging systems and lines, it is important to carry out a series of essential tasks, such as:
- Cleaning: Removal of dirt, dust, and debris from the equipment to prevent buildup that could cause corrosion or other problems.
- Lubrication: Application of lubricants to moving parts to reduce friction and wear, and prevent oxidation and corrosion.
- Mechanical adjustments: Adjustment of components and loose connections to prevent equipment from vibrating and becoming misaligned.
- Inspection: Check the equipment for signs of wear and tear, such as cracks, leaks, or other damage.
- Calibration: Ensuring that each equipment component is calibrated according to the manufacturer’s specifications (e.g., bearings, motors, drivers, etc.).
- Replacement of parts: Obviously, the replacement of worn or damaged parts before they cause equipment failures.
- Updating Control Software (PLC): PLC updates by the manufacturer can include new features, security patches, user interface improvements, and optimizations in operational efficiency.
- Verification of safety systems: It is also important to regularly check safety systems, such as emergency switches, light barriers, and automatic stop systems, to ensure personnel safety and prevent equipment damage during operation.
- Quality control of consumables and materials: Using quality packaging materials and appropriate specifications, such as films and strapping, is also essential to ensure the proper functioning of packaging machines. Poor quality materials can cause jams, premature wear, or even damage to the machinery.
- Maintenance of conveyor systems: Conveyors are not part of the equipment itself, but it is important to conduct regular visual inspections for wear, cuts, or misalignments. Additionally, regular lubrication is necessary to maintain system efficiency and prevent unplanned stoppages. Keeping conveying systems clean and free of debris buildup is also vital for their proper functioning.
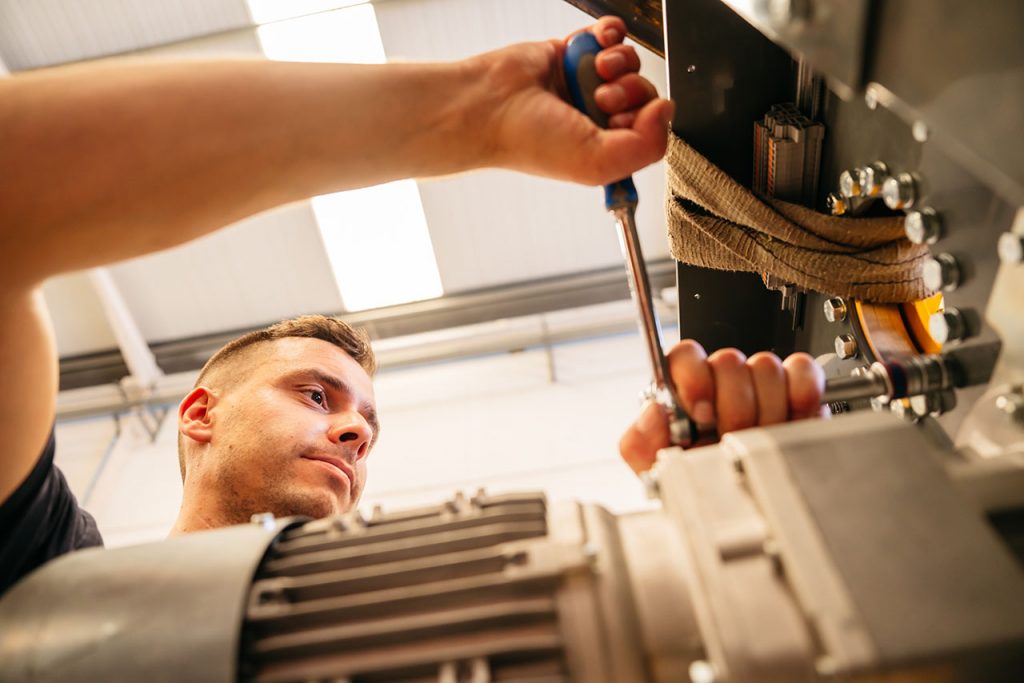
In short, it is important to rely on the manufacturer to maintain our packaging machinery. It is crucial to know not only the basic maintenance tasks such as cleaning and lubrication that we should perform on the equipment, but also be aware of all the maintenance services that the manufacturer can provide.
At Innova Group, we understand that good preventive maintenance is key to keeping packaging systems operational and productive at the highest level. As manufacturers with over two decades of experience, we offer personalized advice to ensure your machinery works “like the first day.” Contact us without obligation to design a maintenance plan tailored to your needs.
Do you like our technical packaging posts? Subscribe to our monthly newsletter for the latest tips, news, and trends in the logistics and packaging sector.