Total automation at Argenta Factory 4 with a double packaging line from Innova
A fully automated and connected logistics center. A packaging station to match the increase in production. The safest and most secure ceramic pallets for transport… These were some of the requirements that Grupo Argenta presented us with for the expansion of its Factory 4 and to which Innova provided a solution with a second automatic packaging line, installed at the end of 2021. The project included the relocation of its previous line, installed in 2019, to create a centralized and automated end of line that would respond to its large production.
With the double packaging line in Factoría 4 (Villafamés – Castellón), Grupo Argenta relies once again on Innova as its official packaging supplier, for its reliability and technological performance. Together with this project, the renowned ceramic group has a total of 8 automatic packaging lines with Innova systems.

The double packaging line project
At the Factory 4 packaging station, there are practically no operators. The entire process is automated. The AGVs deposit their loads on one of the two packaging lines, depending on the pallet format, and the packaging process starts: pallet strapping and compacting, stability, protection and shipping label with final weight. Argenta pallets leave the double line station ready to be transported, stored and shipped thousands of miles away.
When Argenta proposed a new line due to the increase in production, Innova designed a project for the two lines to share space and pallet input and output flow. So the project consisted of:
- New line with horizontal strapping, pallet stretch wrapper and Stretch Hood, with pallet infeed for AGV and outfeed for pallet picking and storage.
- Relocation of existing Factory 4 line, installed in 2019 by Innova, with the same layout of automatic packaging systems, entrance for AGV and exit parallel to the new line, to converge in the logistics collection area.
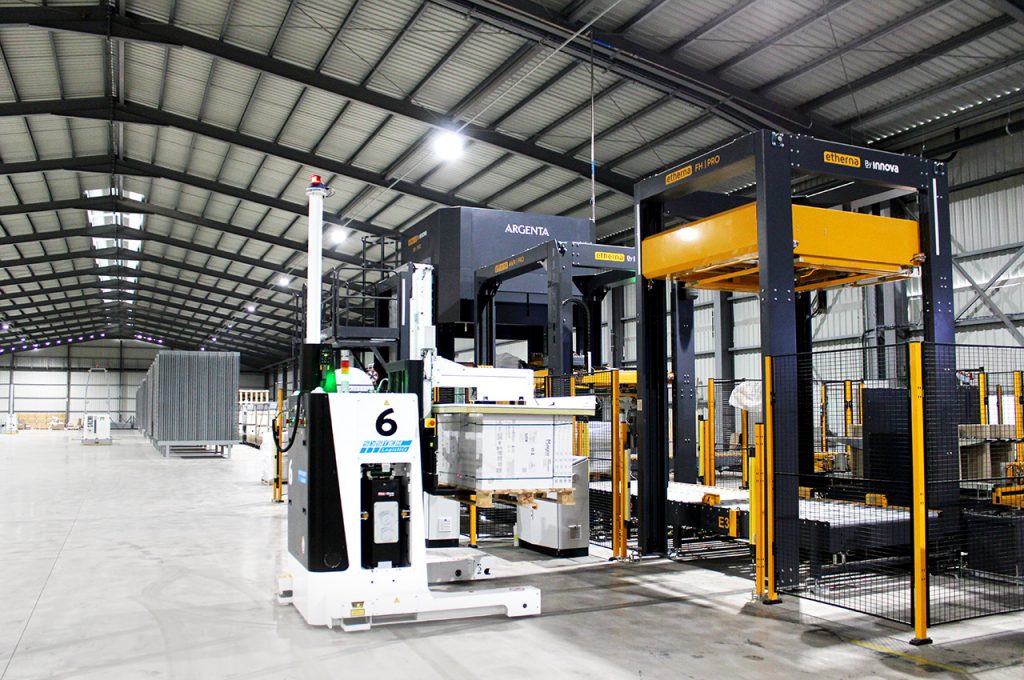
The “Argenta signature” packaging line
The new line presents the same combination that Grupo Argenta uses in all its end-of-line due to the achievement of protection results and maximum pallet safety.
So the new installation is composed of:
- Inbound conveyor by AGV
The entry to the line is done using a conveyor adapted for AGV access, in the same horizontal strapping machine. The AGV deposits the pallet and communicates with the PLC of the line sending the information of the format to be packed automatically.
- Horizontal Strapping System Etherna FH | Pro with Edge Protectors
The first station of the line is always the horizontal strapping, since its purpose is to compact the load just after palletizing and strap it horizontally for its fastening. In addition, this system incorporates the automatic edge protector applicator that adds extra protection to certain ceramic formats.
- Ring Wrapper System Etherna AWR | Pro 2
The pallet is then wrapped with the automatic Stretch Wrapper system, which provides support and greater stability by joining the load to the base of the pallet. The type of pallet stretch wrapping and the roping system help to reinforce this union and homogenize Argenta’s load. In addition, the new automatic stretch wrapper installed at Factoría 4 includes a high production kit for faster and more efficient pallet stretch wrapping, with less film usage.
Why stretch wrapper and not vertical strapping?
Due to Argenta’s ceramic formats, with different palletizing mosaics and special box sizes, wrapping technology is needed to completely secure the load, since certain palletizing distributions do not admit vertical strapping. The wrapping system is also more respectful to the load without the tension that strapping can apply and without the need to also include horizontal corners to protect it from vertical strapping.
- Stretch Hood System Etherna SH – Pro
Finally, the load is wrapped with the Stretch Hood system that offers the final protection and sealing against external agents and weather conditions during storage and transport. The Stretch Hood technology installed at Factoría 4 has 2 film reels for greater autonomy and adaptation to all formats. In addition, this model is designed and programmed to offer faster stretch hooding: while the pallet is in the pallet stretch wrapper, the Stretch Hood has already prepared the film so that in a matter of seconds the pallet is already wrapped.
- Outbound conveyor line
The new automatic packaging line ends with an outbound conveyor with two rotating systems and a weighing station incorporated in the conveyor that communicates in real-time with the labeling machine and prints the final weight of the already packed pallet. This conveyor line takes the pallets to the external logistics station where they are picked up for storage.
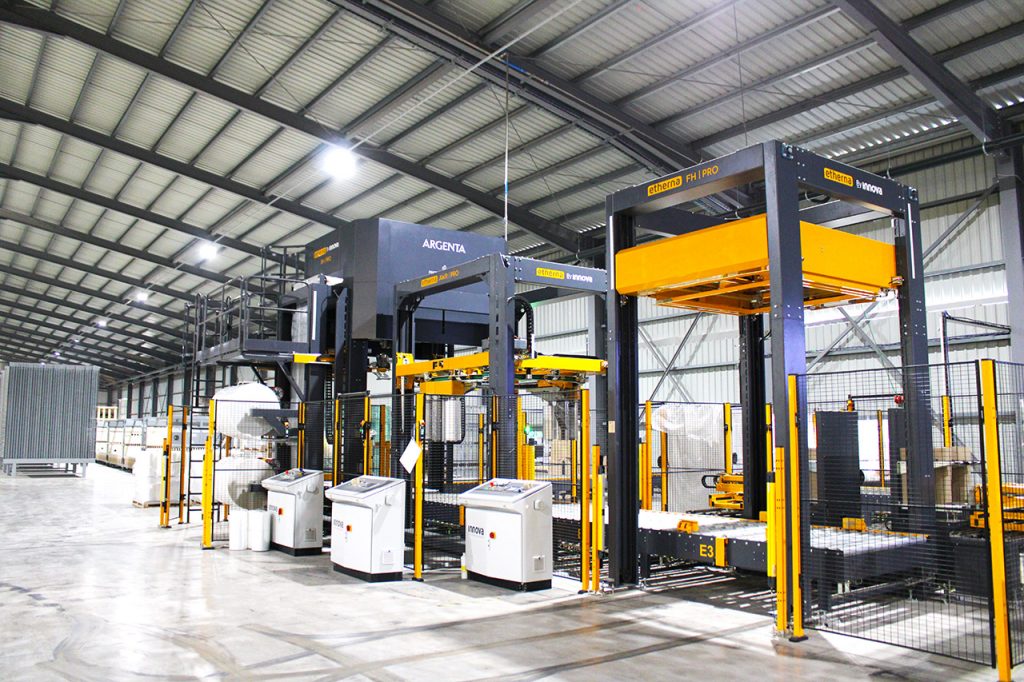
Results and future of the packaging project
The new packaging station provides Argenta with a considerable improvement in the packaging process by centralizing it in a single location and fully automating it. The new line is also designed to be more energy efficient with minimal consumption of film, fewer stops in the packaging flow for reel changes and reducing the plastic of the final packaging, in line with the company’s productivity and sustainability goals.
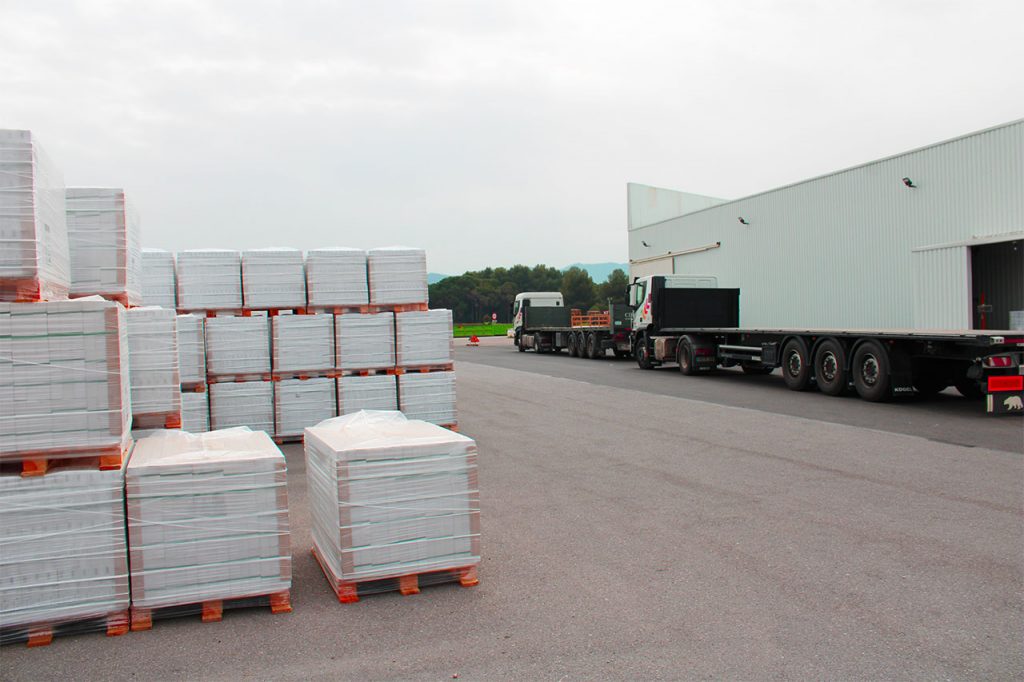
This new line of Factoría 4 is part of a sure commitment of Grupo Argenta to automation and technological advancement in all its factories, of which Innova is proud to be a part. The company has expressed its satisfaction with the project at all levels and its commitment to new joint projects in the future.
For Innova, working again with Argenta is a pleasure, as it is more than a partner and a client with whom we hope to continue working together for many years to come.
We follow the heart
Thank you Argenta for trusting Innova once again!