Grupo Argenta trusts Innova once again with a complete automatic packaging line in its Factory 3
Automation 4.0, logistics security, product protection and brand image, these were some of the objectives that Grupo Argenta was looking for with its new end-of-line project and to which Innova responded with a complete end-of-line packaging line. The leading ceramic group continues growing and investing in the latest automatic packaging technologies. Proof of this was this new packaging line installed in its Factory 3 and Logistics Center.
The new automatic packaging line went into full production in September 2020, providing service to its Logistics Center and Factory 3 in Onda. Through this new installation, Argenta once again confirms Innova Maquinaria as its chosen partner in packaging technology, with whom it already has projects in Factory 1 (Vall d’Alba), Factory 2 (Onda) and Factory 4 (Villafamés).
Renovation of the automatic pallet packaging system with the latest technologies
Grupo Argenta was clear that they needed a final packaging line to match their intelligent factory and their quality product. Therefore, they asked us to renew their previous stretch packaging system with a new Stretch Hood installation that would provide greater speed, efficiency and, above all, protection for their product.
Why switch from Heat Shrink packaging to Stretch Hood?
Although the packaging results may seem similar, many ceramic companies have already made the switch from heat shrink packaging to Stretch Hood for various reasons of safety, system renewal, speed, but also economy and sustainability of consumables. The heat shrink packaging system has gradually given way to the Stretch Hood, which has become its successor in the case of renovation of old systems.
See more: Hooding systems comparison: Stretch Hood or Shrink Hood?
In the case of Grupo Argenta, the company was not only looking for a renovation of the automatic stretch wrapping system itself. They also required other additional protection elements that were more respectful of the ceramic product, such as the combination of the pallet strapping machine with corner protectors and the ring pallet wrapper. Let’s see next what the project consisted of.
The Argenta Signature automatic packaging line
The line installed in Factoría 3 has the design and signature by Argenta, as they were one of the first ceramic companies to incorporate this successful combination of pallet packaging systems aimed at total protection and holding: horizontal strapping machine, stretch wrapping machine and Stretch Hood.
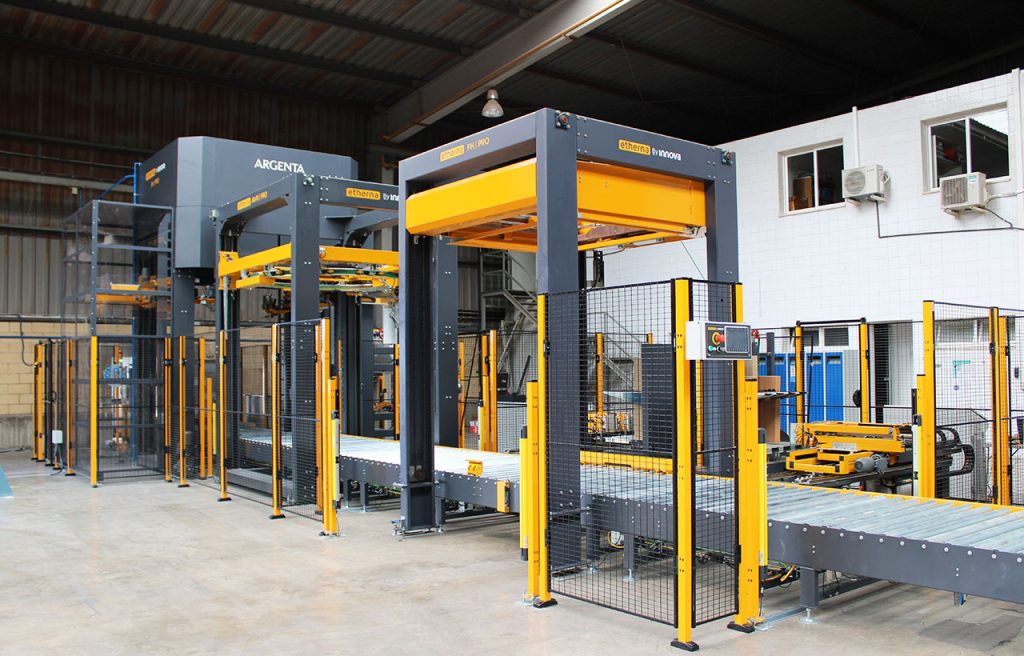
1. Horizontal strapping machine with edge protector applicator
The first station of the line is the horizontal strapping system that first compacts the ceramic load into a block and then applies the protective corners. The edge protection system is used to protect the loads from the application of the strap and is one of the most widely used options in the ceramic industry to preserve and protect the boxes.
Once the edge protectors have been placed, the horizontal strapping is carried out, applying as many straps as the height of the boxes in the palletizing system. In the case of Argenta’s automatic strapping machine, it also incorporates a strapping head developed by Argenta with high precision and state-of-the-art components.
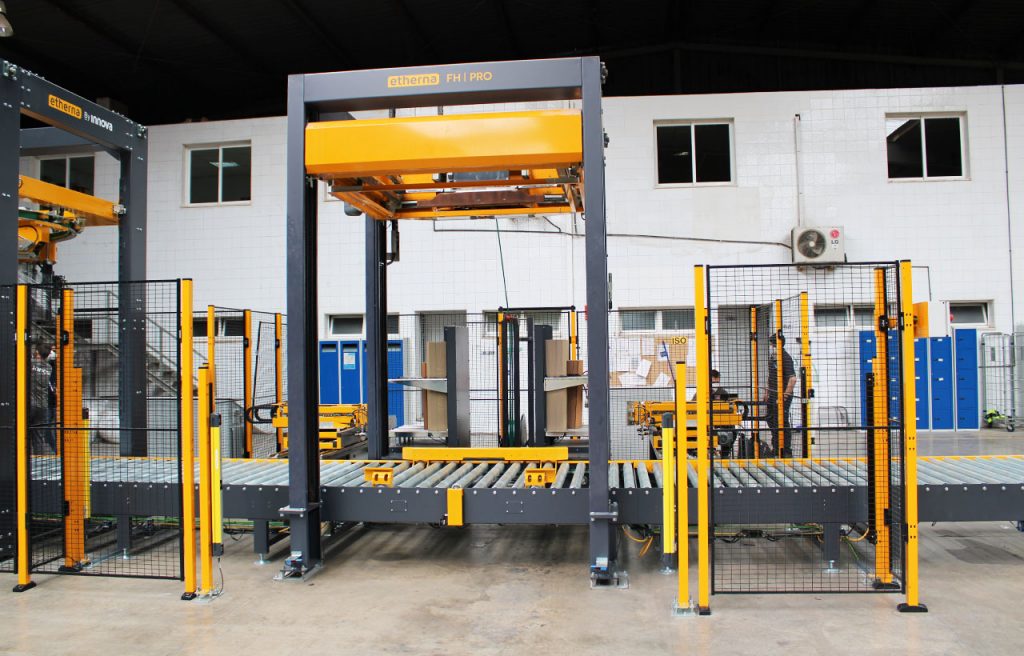
3. Automatic ring wrapping machine
Next stop of the pallet wrapping is the automatic ring wrapping machine, which wraps and secures the load with the application of the cord system.
Why a stretch wrapper instead of a vertical strapping machine?
In many ceramic packaging lines the automatic wrapping system replaces the vertical strapping machine with the objective of joining the load to the base of the pallet. In Grupo Argenta’s lines, the ring pallet wrapper was chosen because it performs a special holding that is more respectful with the ceramic product than the strapping itself. By wrapping the load, the boxes do not suffer as much tension as with the application of strapping. In addition, the reinforcing cord system of the automatic wrapping machine provides a similar hold to that of strapping, thus increasing the hold provided by the wrapping itself.
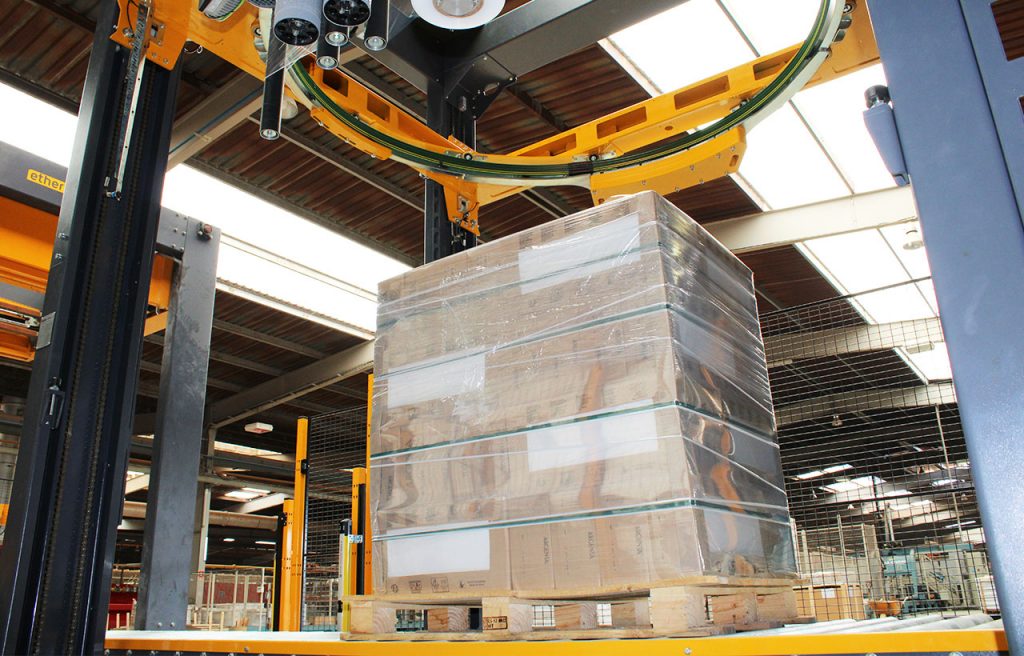
4. Stretch Hood System
Finally, Argenta’s pallet receives full protection thanks to the Stretch Hood System wrapping that covers the load with a tubular stretch film. In this case, a Stretch Hood SH1 Pro 2 system was installed with two film reels to adapt to the different pallet formats in its Factory 3.
The Stretch Hood film provides impermeability and protection against dust, humidity and UV rays, so that Argenta’s ceramic product arrives flawlessly at its export destination.
5. Roller conveyor line
The entire packaging facility is connected to a conveyor line adapted to Argenta AGVs. This line includes roller conveyors, weighing system, link conveyors, buffer and pallet pick-up and retrieval.
Complete line in operation (vídeo in Spanish):
Results: higher efficiency at Argenta end-of-line
With the new Factoría 3 line, Grupo Argenta once again achieves its objectives of improving the protection and safety of the logistics of its products. With this new installation, the ceramic group standardizes most of its plants with the same packaging process, gaining in logistic efficiency.
Argenta has expressed its satisfaction with the project and the trust placed in Innova for this and future projects. Innova is proud to be able to work with a group that has already become more than a partner and with whom we share a philosophy of innovation and sustainability and our most human values.
#WeFollowTheHeart
#WeAreYourPartner