Top 10 most frequently asked questions about the automatic Stretch Wrapper
The stretch wrapping system is one of the most widespread and widely used final packaging solutions to protect loads. There is a wide range of wrapping machine types with different applications and complements, depending on the product and the customer’s objective. Therefore, when choosing a pallet stretch wrapper for a packaging project, many questions arise that, as manufacturers of this system, we receive and handle on a daily basis.
In today’s article, we will answer some of these questions and doubts about the automatic wrapping system, continuing our series of Top 10 Frequently Asked Questions.
Top 10 FAQs about Automatic Wrapping Machines
- What types of stretch-wrapping machines are available in the market?
- What is the difference between a semi-automatic and an automatic wrapping machine?
- What type of wrapping machine is recommended based on production?
- What types of cycles can a stretch wrapper perform?
- What type of film and consumables does a stretch wrapper use?
- How much stretch film does a stretch wrapper consume? How can I save on film?
- How does the stretch wrapper offer total protection to the load?
- What wrapping speed can a stretch wrapper achieve?
- Can pallet-less loads be stretch-wrapped?
- Which accessories can be included to improve the stretch wrapping?
1. What types of stretch-wrapping machines are available in the market?
Due to its long extension in the market, there is a multitude of stretch wrapping models according to the needs and functionalities sought in the packaging process. Even so, leaving aside manual wrapping processes, we find large categories such as:
- Wrapping robot: Semi-automatic solution with a vehicle that performs the wrapping by circling the load. Its great advantage consists in the fact that the load does not have to be moved or to be placed on any platform or automatic line. The big disadvantage is the human operation and the time required for wrapping, so it is usually recommended for low production rates.
- Turntable Stretch Wrapper: The next in the range of performance is the turntable wrapping machine, which can be semi-automatic or fully automated and integrated into the conveyor line. The load must be placed on the platform and the wrapper applies the film at different heights by rotating the load. The turntable stretch wrapper is versatile in space and performance for low to medium production and packaging needs. For this reason, it is one of the most common models on the market. This type of wrapping machine can also include accessories to improve the wrapping process, such as the load reinforcement roping system.
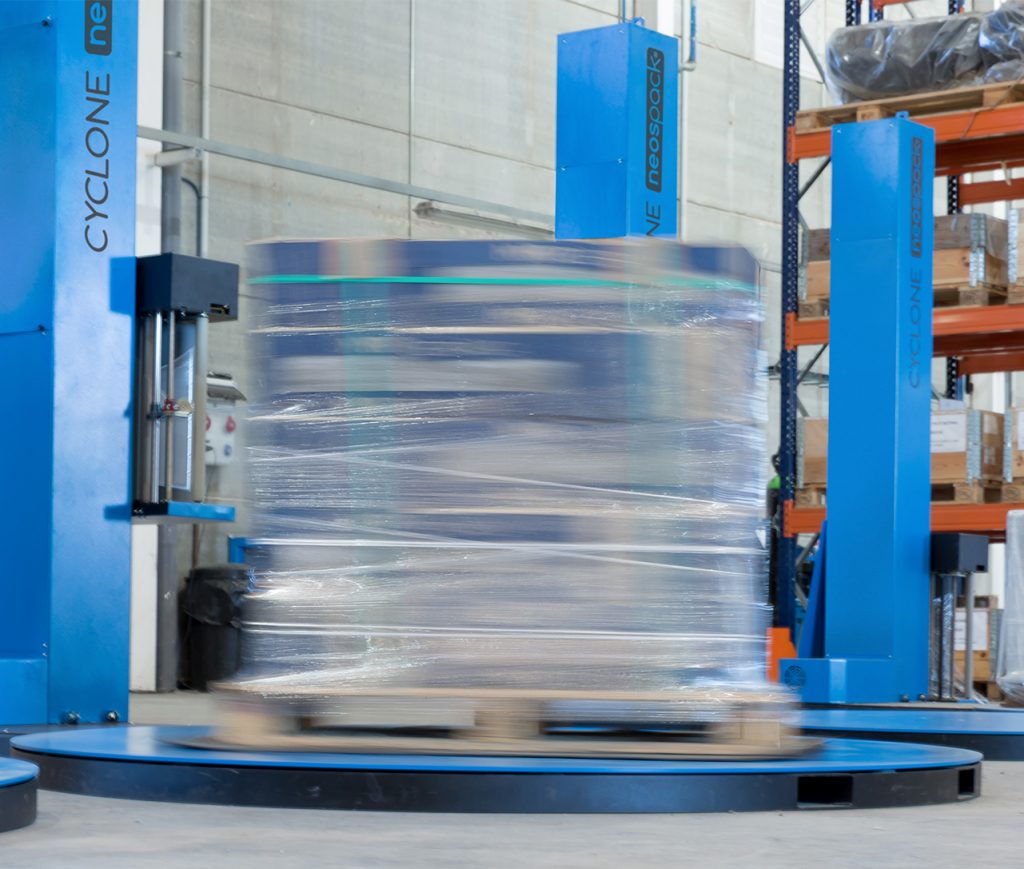
- Rotary arm stretch wrapper: The next level up in stretch wrapping is the rotary arm wrapper, which rotates around the palletized load. Its main advantage over the turntable pallet wrapper is that the goods remain stationary, which makes it ideal for unstable or fragile loads. This type of wrapping machine is commonly offered in automatic mode and integrated into automated lines with conveying and medium to high production.
- Ring Stretch Wrapping machine: The ultimate high-performance wrapper is the Ring Stretch Wrapper, which can even double the speed of the Rotary Arm wrapper. The concept is the same as with the arm wrapping machine, except that the wrapping is done by a ring with one or two film carriages. This top-of-the-range stretch wrapper is usually used for high production rates.
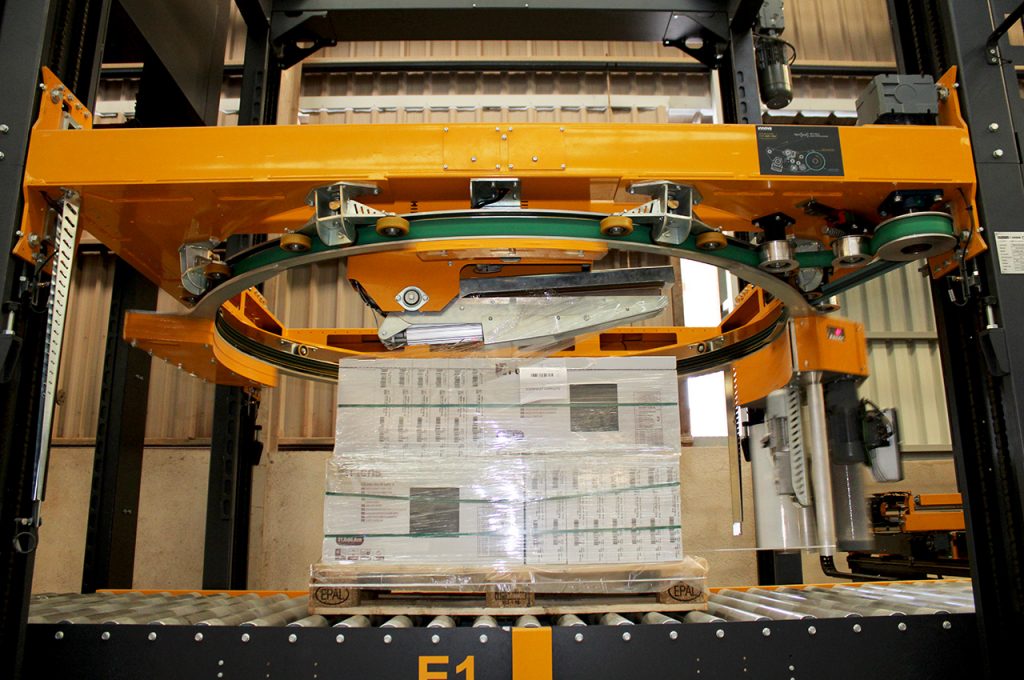
- Horizontal Orbital Wrappers: Finally, also name the orbital wrappers for the horizontal wrapping of extra-long loads, such as panels, construction materials, furniture, etc.). The objective is usually different than the rest of the vertical wrappers, since the load does not have to be palletized.
2. What is the difference between a semi-automatic and an automatic wrapping machine?
The main differentiation is the automation component. While a semi-automatic (turntable or robot) pallet stretch wrapper needs human intervention to start the cycle, the automatic pallet stretch wrapper is part of a fully automated line. On the other hand, while the semi-automatic platform stretch wrapper can be installed anywhere in the factory, its automatic variant needs a conveyor line that allows pallets to flow in and out.
Finally, automatic stretch wrappers usually offer more features such as safety extras, higher speed, accessories, etc.
3. What type of wrapping machine is recommended based on production?
Usually, for low production (less than 20 pallets/hour), we recommend semi-automatic pallet stretch wrappers, as they offer versatility yet higher wrapping quality than a robot stretch wrapper.
For a range of 30 – 40 pallets/hour, we can already recommend an automatic stretch wrapper which can be either a rotary arm or a low-production ring wrapper.
For higher outputs of 40 pallets/hour or specific wrapping requirements, the reliable choice will be a high-performance ring wrapper. High outputs of 80 – 100 pallets/hour typically use double film carriage stretch wrappers for higher speed.
4. What types of cycles can a stretch wrapper perform?
Depending on the product and packaging objectives, different types of cycles can be designed. The versatility of stretch wrapping is precisely the fact that it is possible to program a wrapper with different tension and reinforcements in the various areas of the load. Some examples of these can be:
- Base reinforcement, for light loads: The cycle will focus on reinforcing the bundle at the base for transport, either with film or with the help of the reinforcing roping device.
- Reinforcement in the upper overlap, for very high loads: The cycle will cover the entire high load, with additional support in different areas and in particular in the overlap of the upper film.
- Rope application for extra support: On heavy but fragile loads, the rope is used to generate extra support similar to strapping. The roping also serves to compact the load and can be programmed to reinforce specific areas depending on the shape of the load.
5. What type of film and consumables does a stretch wrapper use?
Usually, the pallet wrapping machines use stretch film, but they can also employ pre-stretched film or other new consumables on the market, such as kraft paper with stretching capabilities.
The standard stretch film is composed of low-density line polyethylene (LLDPE) which is what gives it its high stretch capacity. Depending on the characteristics of the plastic and the stretch wrapper (and its pre-stretching system) this type of film can stretch between 25 and 300%. If both the film and the stretch wrapper allow a higher stretching (more than 150%), allowing also a higher saving.
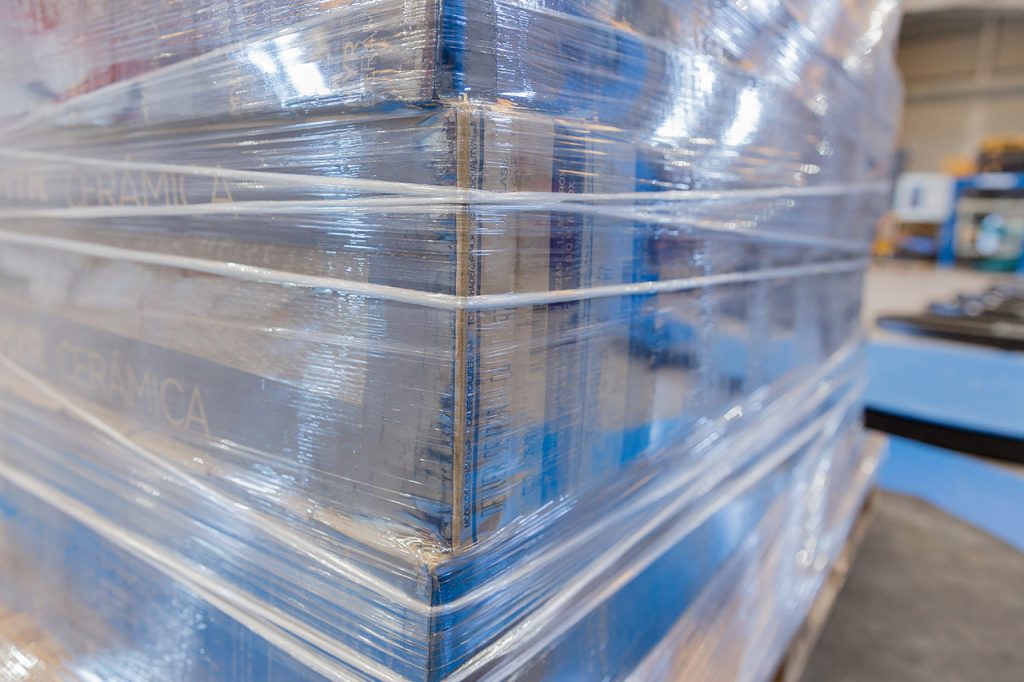
The pre-stretched film is a film that has already been stretched to its shrinkage limit (which is usually 100%) and is normally used in manual or semi-automatic applications without pre-stretching and low tension. It is a non-stretch film recommended for loads that need slight protection or restraint.
Lastly, stretch kraft paper fulfills a similar function to pre-stretched film, with the great difference that it has a lower stretching capacity and does not allow the application of a rope system. Even so, it has recently appeared on the market as a more sustainable alternative to film, since it is 100% recyclable.
6. How much stretch film does a stretch wrapper consume? How can I save on film?
Film usage in a pallet stretch wrapper depends on many factors: type of stretch film, if it is stretchable, pre-stretched, or not, and its stretching capacity, but also the features of the stretch wrapper, the wrapping cycle, rope application, cover, load size… the list is almost endless. Even so, several factors make it possible to economize and optimize the film to the maximum:
- Use stretch film with a high stretch capacity of up to 400%.
- Use a pallet wrapping machine that allows this type of pre-stretching.
- Design a wrapping cycle that uses only the strictly necessary film, with tensioning points for better fastening.
- Use high-performance stretch wrappers, since, in addition to using torque control technology, they usually have a double stretch film cart to wrap the load in less time, with fewer wraps and more precise tensioning.
7. How does the stretch wrapper offer total protection to the load?
The automatic stretch wrapper system can run a cycle that covers from the base to the top of the pallet, where a cover is placed to fully protect the load. The cycle can be programmed with higher tension to ensure that no layer is detached and that the wrapping is compact and sealed.
However, an alternative for total protection in automated productions with medium-high production is usually Stretch Hood wrapping, which covers the entire load with a single layer of film.
8. What wrapping speed can a stretch wrapper achieve?
In the case of automatic stretch wrappers, a standard wrapping can perform between 60-80 pallets/hour. For speeds of 80-100 pallets/hour, ring wrapping with two reel carriages is recommended. And more than 100 pallets/hour and up to 200 p/h are achieved with high-performance stretch wrappers but also depending on the type of load and wrapping requirements.
As this is such a broadly defined aspect, we recommend consulting with an expert team in packaging, such as Innova’s, to determine which type of stretch wrapper or packaging system is best suited to your production.
9. Can pallet-less loads be stretch-wrapped?
Although most stretch wrapping equipment works with palletized loads, pallets loads can also be packaged employing a special accessory. In automatic stretch wrappers, a conveyor-lift system is usually included to raise the load so that the wrapping carriage can reach its base and protect it.
10. Which accessories can be included to improve the stretch wrapping?
The pallet wrapping system is one of the most extensive and technologically evolved solutions in recent years. For this reason, it is a very versatile system that allows to include a multitude of accessories to improve the wrapping according to the wrapping objectives.
Some of the most common accessories of automatic wrapping machines:
- Roping device: The wrapping carriage converts the film into a rope that is applied around the load to reinforce its hold and compaction. It acts as a horizontal strapping.
- Top press: For light or unstable loads the wrapper can include a top press to hold the load while wrapping.
- Cover application: Automatic systems usually include an also automatic accessory to apply the top cover for those loads that require total protection. The cover uses a different consumable than the stretch film, being a film with protective properties that overlaps with the film.
- Edge protector applicator: For special loads that require edge protection, vertical cardboard edge protectors can be included. This is the case for goods with boxes, blocks, or products such as home appliances that need to protect their edges from film application.
At Innova we have developed an accessory to include the edge protectors automatically during stretch wrapping:
In short, although pallet wrapping systems are the most widely used to protect loads, they still raise many questions regarding their large variety, multitude of features, and accessories. Do not hesitate to contact our Technical Consulting team, which specializes in end-of-line projects. We will be happy to advise you on your packaging project without obligation.