How to avoid stretch film breakage in pallet stretch wrapping
One of the most common problems and causes of stoppages in the final packaging is film breakage during pallet stretch wrapping. Although it may seem like a simple error or malfunction, it can cause unnecessary stops in the automatic line and constant intervention, as well as damage to the goods if the breakage occurs afterward.
In today’s post, we will review some tips to avoid film breaks during pallet stretch wrapping and further optimize packaging times and savings in consumables.
Consequences of film breakage
First, we review the problems of film breakage, as they can go beyond a simple line stoppage:
- During stretch wrapping: packaging stoppages, excess and waste film, imperfect wrapping, loss of productivity.
- After wrapping: product losses, breakage of primary packaging, labor or transport accidents, among others.
Tips to prevent stretch film breakage
In most cases, film breaks occur before wrapping even takes place due to problems with the goods themselves, the film itself, or the programming and performance of the pallet stretch wrapper. Therefore, following certain safety steps and wrapping tips can prevent many of these ruptures.
Our checklist to avoid breakages:
1. Prepare the load: palletizing and uniformity
The first key point is to have a good palletizing system that ensures that the load is as homogeneous as possible. Manual palletizing usually results in unstable loads with irregularities and sharp edges that can cause problems in terms of stability and safety later on.
It is always important to check that there are no bulges or sharp corners that could tear the film, as this is the main cause of breakage and accidents.
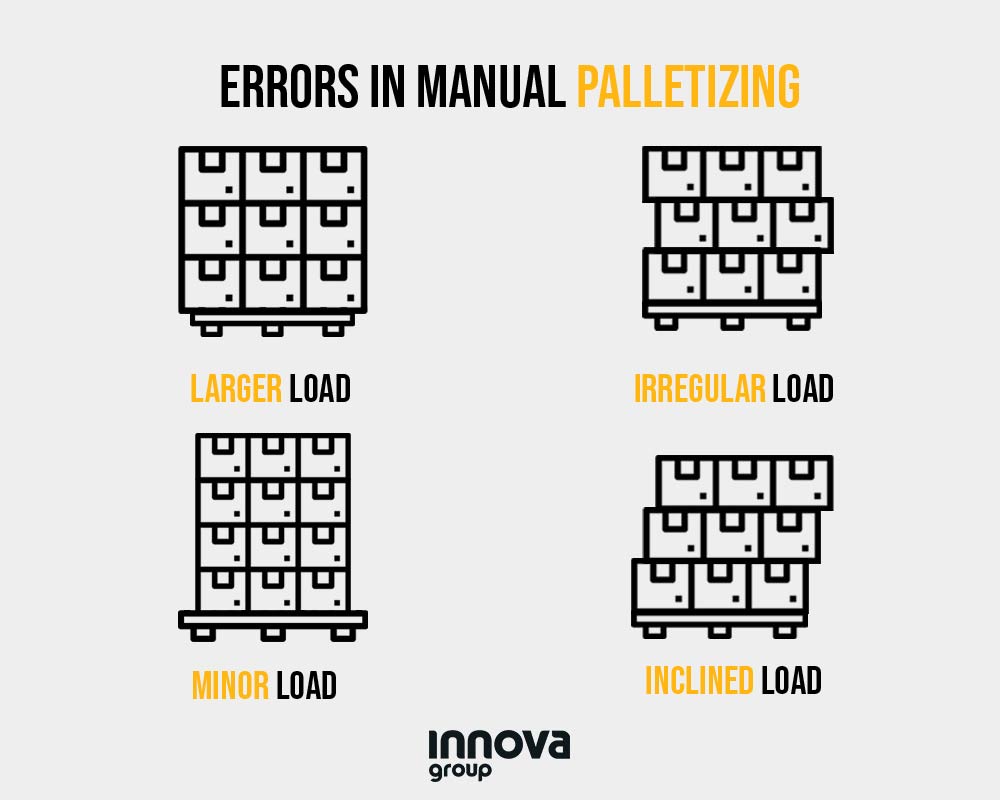
2. Prepare the wrapping cycle: Tension settings
The correct programming of the wrapping cycle is the next step to ensure that there are no breaks. In the case of automatic stretch wrappers, it is usually already programmed by the line manufacturer, but in the case of semi-automatic stretch wrapping, the optimum wrapping tension and pre-stretching must be taken into account.
If the tension is too high it can cause constant breakage. Therefore, depending on the type of film and product, different tensions and wrapping forces should be tested to determine the best setting. The optimum wrapping tension will be the point at which the film does not break and there is no deformation or crushing of the load.
This point is essential to avoid rips and tears and achieve better pallet containment in all parts of the load.
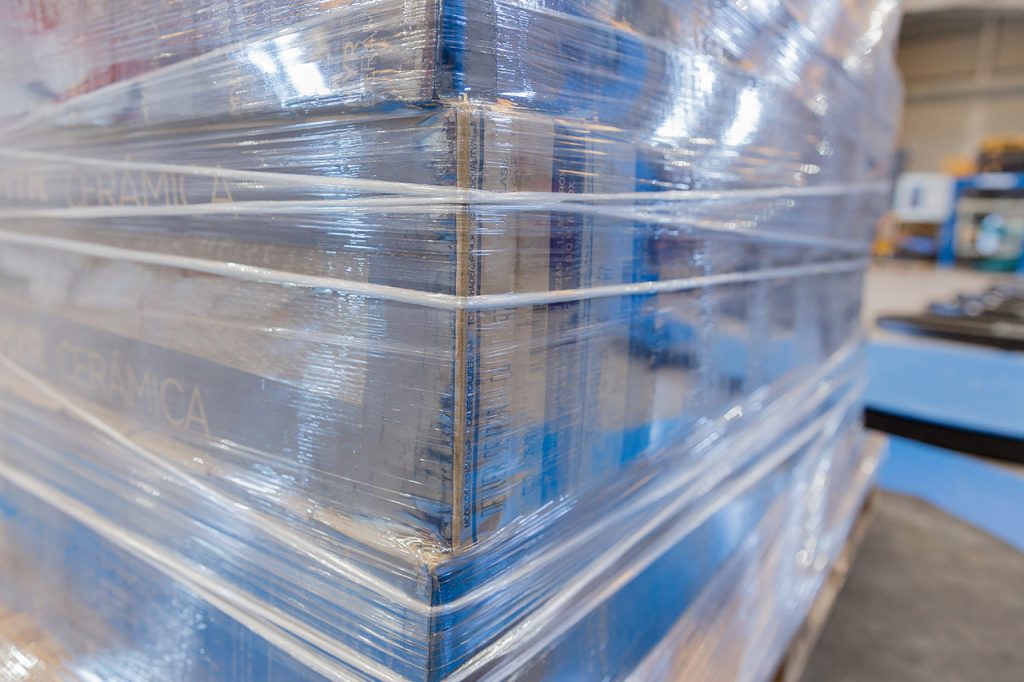
3. Specialized technicians: personnel training
In the case of automatic stretch wrappers on a packaging line as well as semi-automatic wrappers, it is essential that machine operators are trained in basic operation, alarm reporting, and, above all, correct film handling.
Even with automatic pallet wrapping solutions, specialized personnel must know how to handle the film and place it correctly on the wrapping machine carriage. Incorrect film positioning is one of the main causes of film breakage.
In addition, if a film reel is dropped or handled incorrectly, dents can occur on the edge of the reel. These flaws can be film breaks about to happen.
4. Use of quality film: Cheap is expensive
Another important point is the quality of the film itself and even its gauge. Low-quality, or “cheap” films are more prone to cracking, tearing, defects, etc. In fact, these cheap films tend to be less tear resistant and have lower stretchability than high-performance films.
In the end, the savings that can be achieved with this type of film simply disappear with only one damaged load and product losses.
5. Choosing the right film and machine for your product type
In line with the previous point, the type of film is essential, but so is the pallet wrapping machine employed. It is important to study the needs of the product in order to determine the film gauge, its pre-stretching characteristics, and the performance of the wrapping machine itself. Some examples:
- For light loads, such as empty PET containers, gauge ratings of less than 15 microns / 0.60 Mil can be used so as not to crush the load with too much tension.
- For heavy loads, where extra stability is needed, higher gauges provide greater tension to the load and greater stability, as well as the possibility of applying the reinforcement cord.
The best way to determine the type of film, its gauge, and pre-stretch capacity is to consult with the stretch wrapper manufacturer as they can offer advice on how to best optimize the film.
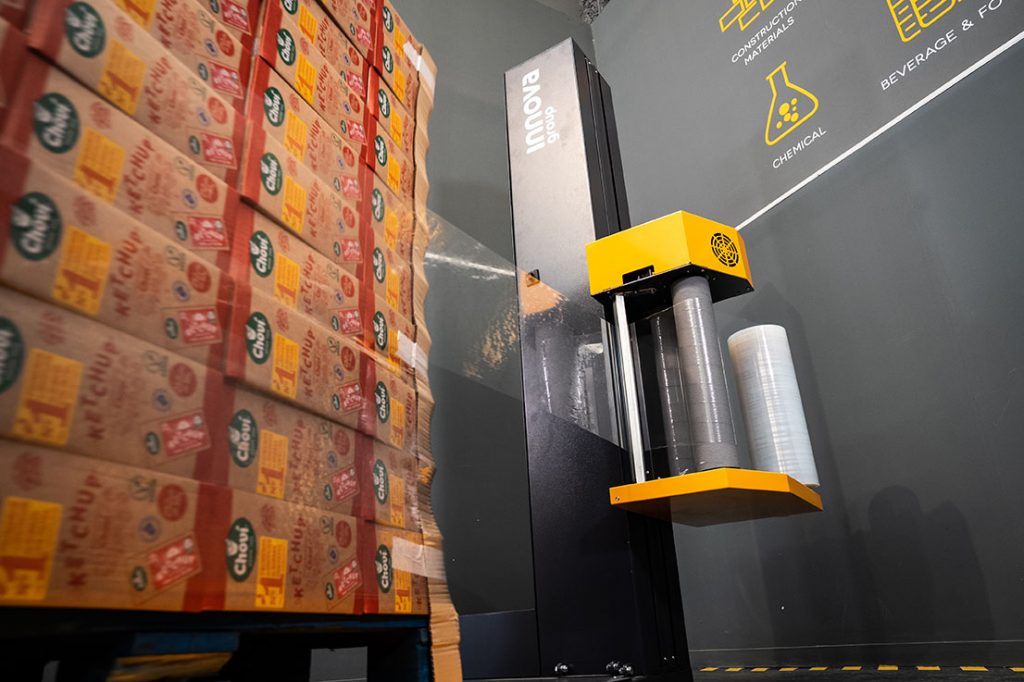
6. Specialized stretch wrapping accessories
Another important consideration is to consider wrapping machine accessories to improve stretch wrapping and load protection. Some of these accessories improve the wrapping and prevent breakage:
- Reinforcement roping device: It holds and compacts the load without having to give extra tension to the usual wrapping. It is a compact rope similar to a strap that is very difficult to break.
- Edge protector Applicator: For loads needing uniformity and edge protection, or simply so their corners do not break the film. In the case of laminated or stacked products with a sharp or edged finish, it is necessary to include these types of safety edge protectors, usually made of cardboard or steel. With Innova’s automatic ring wrapper, we precisely incorporate an automatic vertical edge protector applicator system for this casuistry.
- Vertical trop press for added stability during wrapping: In the case of very light loads, the top press offers stability and security to the wrapping, preventing the load from tilting or moving and causing tears in the film.
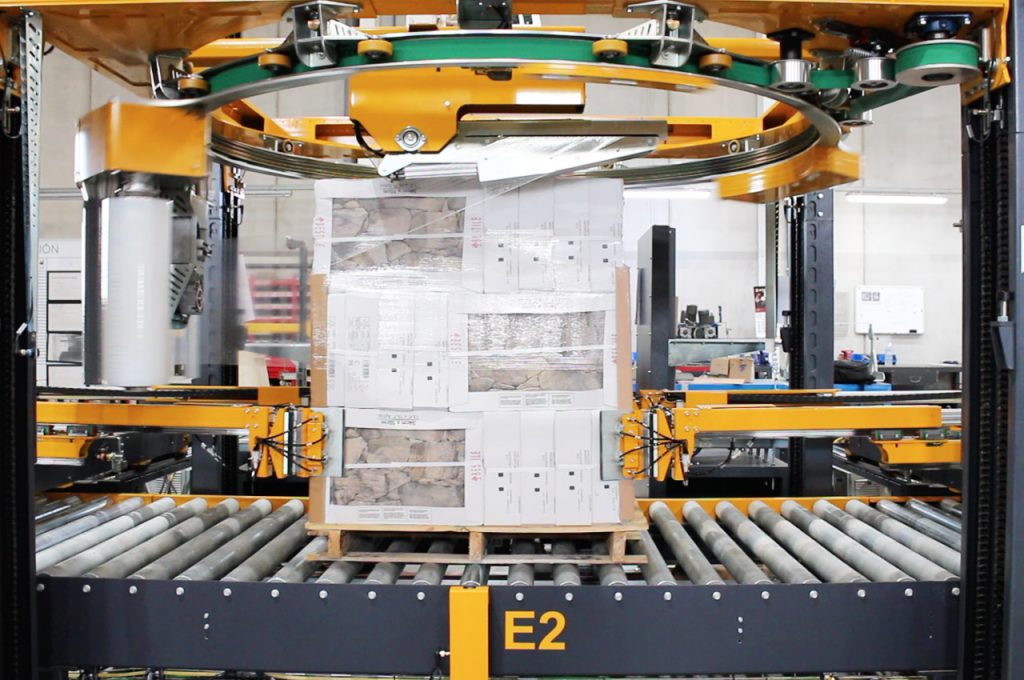
7. Cargo handling after wrapping
Finally, an aspect that is often forgotten is the handling of the load itself afterward: during transport in the factory, loading in the warehouse, stacking and reassembling of pallets, loading on trucks, etc. This is where the remaining large percentage of film breakage occurs, caused by careless handling by the operator.
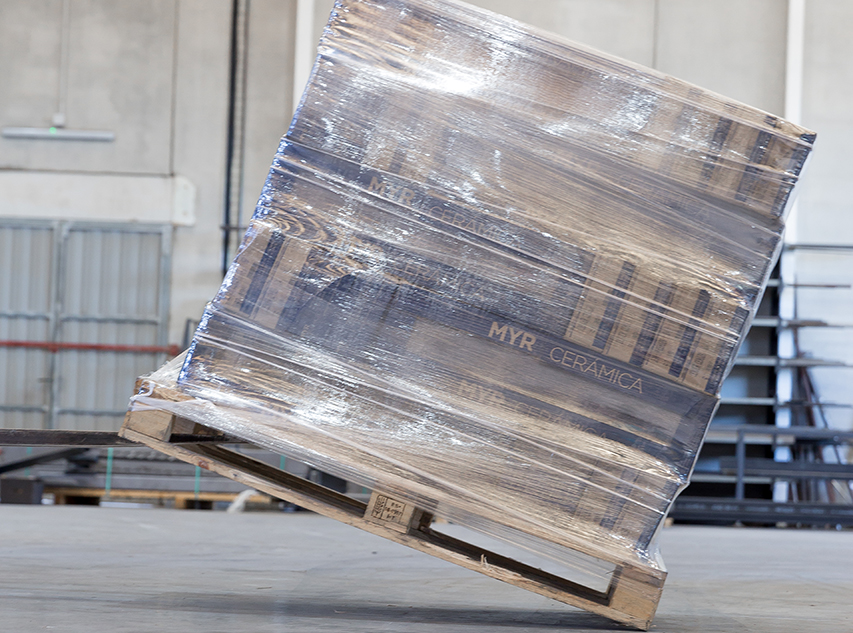
The solution involves thorough training and quality controls in the factory and warehouse so that the pallet loaded on the truck leaves in perfect condition. In the case of fully automated lines, the use of AGVs also provides greater safety in the internal transport of pallets within the facility.
As we have seen, there are many factors to consider in solving this common pallet wrapping problem. When we talk about breakage, it is often attributed to film or stretch wrapper tensioning, but there are many other checkpoints and organizational steps that have an important role to play in pallet wrapping safety.
At Innova, we have more than 20 years of experience in the design and installation of automatic and semi-automatic wrapping machines and we can offer you free advice on wrapping and film types. Do not hesitate to check with our technical sales team, we will be happy to assist you.
Do you like our technical articles? Subscribe to our monthly newsletter for packaging and logistics news.
SUBSCRIBE TO THE BLOG: