Types of Cargo Packaging: Choosing a System According to its Protective and Securing Function
Selecting the right packaging system is key for ensuring the complete safety and protection of our valuable cargo. Nowadays, companies that export goods and those with high logistical flows are required to comply with numerous transportation regulations, packaging taxes, supply chain requirements, and other demands. This has led them to review and optimize not only their automatic packaging process but also the equipment they use. In this article, we aim to explore the different types of packaging, their systems and their functions, as well as how to optimize their efficiency to meet these demands.
Types of Packaging: Primary, Secondary, and Tertiary
Before delving into the various types of logistical cargo packaging, it is important to understand the functions of primary, secondary, and tertiary packaging before exploring the types of logistical cargo packaging.
- Primary packaging is in direct contact with the product and is designed to protect it individually and preserve its integrity. It is also known as the container or packing. Examples include bottles, bags, cans, jugs – any initial product wrapping. This primary packaging determines the need for protection and securing during subsequent transportation.
- Secondary packaging groups and protects multiple units, such as product boxing, bagging, or container wrapping. For solid or bulk products, the primary and secondary packaging might be the same, as there is no need for initial wrapping. Choosing secondary packaging is also crucial when selecting one final protection system over another.
- Tertiary packaging protects the entire load for handling and transportation, whether by grouping various units or securing complete pallets of cargo. This includes all palletizing processes and final packaging systems (pallet strapping, pallet stretch wrapping, pallet stretch hooding, etc.).
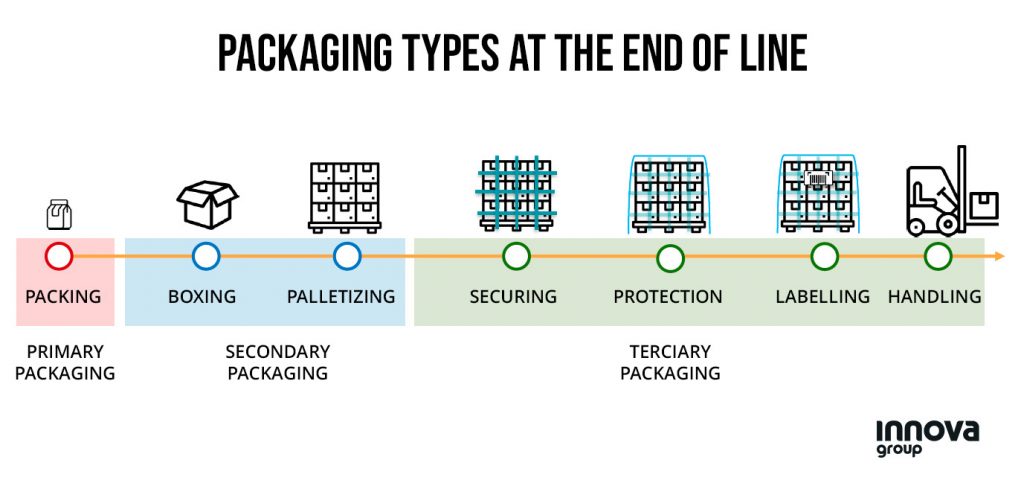
Types of Tertiary Packaging According to Their Function
1. Packaging Systems to Contain the Load:
Depending on the type of product and its primary and secondary packaging (boxes, bags, bottles, etc.), the primary function of tertiary packaging is to contain these units. In this case, packaging systems such as strapping and stretch wrapping are preferred for load containment.
- For all types of loads (from boxes to bags, FIBC, sacks, bottles, etc.), bundling provides a wrap that adds stability and structure to the cargo.
- For heavy box loads, strapping is the preferred system. Using PET or polyester bands, strapping systems secure the load to its pallet base, preventing movements and shifts.
- If the load consists of lightweight and small boxes that do not require significant protection due to minimal handling, box sealing (either manually or automatically) can be applied. This is an effective tool for sealing and uniting boxes, ensuring the integrity of the content during transportation.
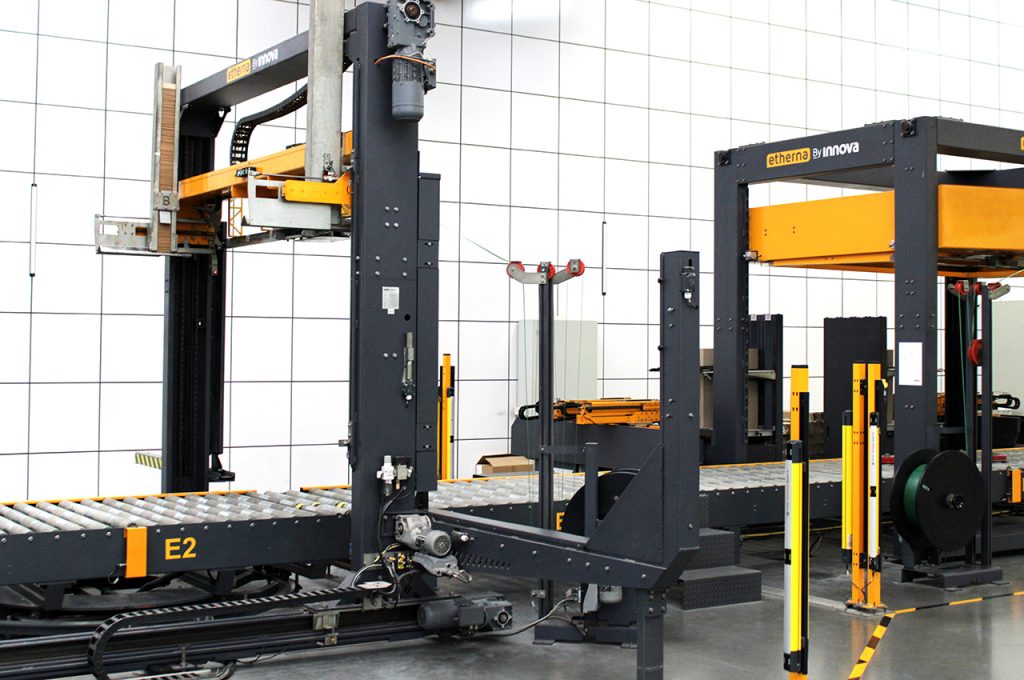
2. Packaging Systems to Protect the Load:
One of the primary purposes of packaging is to protect the products. In this context, two highly effective packaging systems are Stretch Hood and Shrink Hood Wrapping. These systems offer complete protection to the cargo, regardless of its nature or the type of packaging used for secondary protection.
The Stretch Hood automatic packaging system employs a highly stretchable film hood that conforms perfectly around the load, providing a highly effective barrier against moisture, dust, and mechanical damage.The Shrink Hood system, thermo-shrinks a film cover around the cargo, offering a tight and resistant layer.
The pallet Stretch Wrapping system can also be used for total protection by adding a top cover, applied automatically in automatic wrapping systems.
3. Packaging Systems to Unite the Load:
For products where the load must remain fully united and cohesive on the pallet, specific packaging systems are necessary for this purpose. In this case, strapping is essential for containment and uniting different elements. This may be the case for unstable or very light loads.
The Stretch Wrapping system can provide extra securing, acting as an alternative to strapping for specific cargo types, with the help of a reinforcement roping system and extra hold and wrapping containment force.
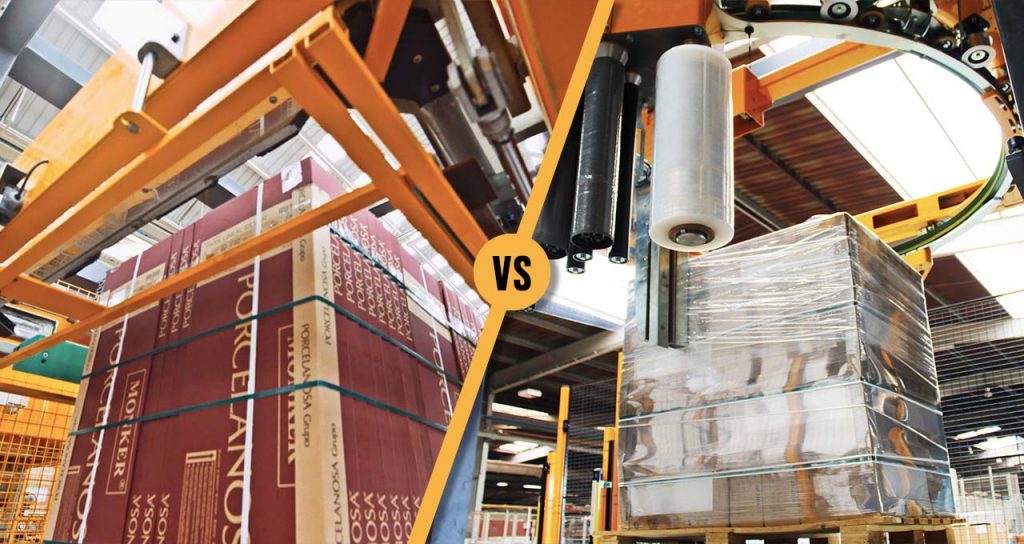
4. Packaging Systems for Securing in Transport:
Ensuring the safety of goods during transportation is of utmost importance for any packaging system. However, simply selecting a packaging type may not be enough to achieve this goal effectively. Through our experience, we have found that it is essential to optimize the film or strapping used and make the most of the system’s capabilities to ensure maximum protection and minimize losses or damages.
In the case of strapping, it is essential to configure packaging with optimal tension to prevent accidental opening and cargo collapse.
In the case of stretch wrapping, it is recommended to analyze the containment force being exerted and reinforce it with greater tension, film pre-stretch adjustments, and, if necessary, a roping reinforcement system.
When it comes to Stretch Hood wrapping, with its dual function of protecting and containing, it is important to use the right film that can adapt to the shape of the cargo, while also providing maximum protection and containment. This can be achieved by using specialized Stretch Hood films that offer better containment, or by applying the hooding more tightly in specific areas of the cargo that require extra security.
In a nutshell, choosing the right packaging type and equipment is crucial for both protecting products and optimizing logistical efficiency. From strapping that guarantees stability to Stretch Hood that provides a protective layer, each system plays a vital role. The industry is constantly innovating by adopting more sustainable materials and advanced connected technologies. This has led to process optimization and renewal of final packaging systems to meet logistical demands and requirements.
At Innova Group, with over two decades of experience in manufacturing packaging systems, we can advise you on choosing and optimizing your end-of-line system. Contact us without obligation and discover how we can optimize your supply chain with efficient and secure packaging.